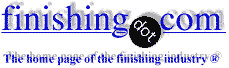
-----
Increasing ASF in barrel plating
Hi We have been Bright Ni plating jewelry items(about 1.5 Sq Ft surface) in small barrels
(Sterling 56) at 20 ASF or about 30 ASF per barrel. We attempted to plate 3 times as much, about
4.5 sq inches in a Sterling 612 barrel and could only plate at a maximum of 10 ASF which affects our brightness and time in the tank.
Presuming that we are at maximum efficiency of the bath and are agitating as much as possible, is there a way to get more ASF out of this situation.
We use rectifiers that seem to max out at 10 volts and 100 amps under a full rack load. Is there something I should know about the relationship of voltage to amperage available. Would a higher voltage/amperage rectifier allow me to plate at a higher ASF. Thanks.
- Harwood Hts, Illinois
1999
Unfortunately, I don't know how big a Sterling 56 or a Sterling
612 is. Is the first one 5" dia. x 6" long and the second one 6" dia. x 12" long?
I suppose it's possible that, given the perforation size of the barrel wall or barrel cloth, and the anode spacing, that 10 volts isn't enough (although that sounds pretty conventional for small barrels). Have you looked inside the 612 barrels to make sure that the holes are not peened almost shut? A barrel can look right from the outside when the holes are actually nearly closed on the inside.
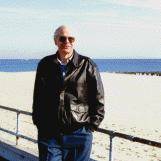
Ted Mooney, P.E.
Striving to live Aloha
finishing.com - Pine Beach, New Jersey
1999
Hi Ken ,
The whole secret to Barrel plating is solution exchange within the barrel , Sterling Barrels have reinforced Mesh panels which come in various sizes of mesh , check the mesh size that you are using , a larger ( more open ) mesh maybe more suitable , also if you are using the same bath for rack work then turn off the air agitation when plating barrels , it is possible that the air is being trapped around the barrels and preventing or inhibiting the free exchange of solution . Also check the mesh panels on the inside to make sure that they are not worn as suggested by Ted , one of the beauties of Sterling barrels is that the individual panels are replaceable .
Best regards

John Tenison - Woods
- Victoria Australia
1999
On the small barrels we also use a solid rod dangler. This gives us much more surface area to make contact and reduces damage to the delicate parts. They don't seem to twist and break as easily as the ball danglers either. A 100 amp/10 volt rectifier should give you more current than just 10 ASF at maximum output. Look at all the connections and check the anode and cathode bars with a multimeter to see what the rectifier is putting out. You also have to be sure not to have an anode/cathode imbalance with the higher barrel loads.
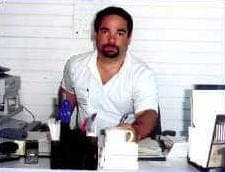
Jim Conner
Mabank, Texas USA
1999
1999
Thank you Ted, John, Jim
I am using the largest holes that I can in the sterling barrel. We put an extra pump on the tank just for circulation without change. We tried pumping the solution directly into the barrel and showed no improvement.
I believe Jim's thought may be the next thing to look at.It brings up the question of how to approximate the anode surface area. We use titanium baskets with small crowns or S rounds. It is easy enough to calculate the square inches of surface area on the front plane. Should I include any area factor for sides, back, or additional surface because chunks are used?
The supplier of the Nickel Bath
(EPI / Electrochemical Products Inc. [a finishing.com supporting advertiser],Wisconsin) suggests an anode area of 2-4 times the cathode area. Any comments
It may not add to this discussion, but I can get 100 amps in this tank with a 2 sq ft dummy plate.
Thanks
- Harwood Hts, Illinois
1999
Here are two experiences of mine that may or may not have anything to do with your problem, but think about them:
1). A chemical supplier had an absolutely impossible 'rectifier problem' in trying to start up a wheel plating line. When he and the customer and the rectifier service man could not get the amperage up in the copper or nickel tank they called me in. It turns out the problem was that, to avoid ruining wheels, they kept trying the same one over and over and over. After countless times through the line it built up such a passivated skin (maybe an anodized surface) that the surface barely conducted electricity! (Sorry to say, I can't take credit for solving the problem, it was solved by accident). I really doubt the applicability, since you are working with jewelry not aluminum, but if you are trying to solve this problem with scrap parts, it could just vaguely be that they are part of the problem.
2). The second experience was a rack plating line where 18 volts, believe it or not, was insufficient for bright nickel plating. See, plating solutions actually have far more resistance than experience leads us to believe. If you look up the resistivity-conductivity of the solution, then apply Ohm's law, you'll ask yourself how it is possible to plate at the voltages we are used to. The answer is that we usually luck out due to the geometry.
In my problematic case, we were nickel plating huge sheets of steel, and the resistance of the solution was 'by the book'. But more usually, we plate individual smaller pieces, and the cross-sectional area of the solution through which the electricity passes is far greater than the area of the part. While resistance = resistivity x length / Area, the area is not the area of the part, it's the cross-sectional area of the solution available to carry ions to that part. A sparsely populated rack or lightly loaded barrel can enjoy a very large cross-sectional area of solution feeding it, and have low solution resistance. Double the parts on the rack or in the barrel and in the worst case you could nearly halve the cross-sectional area of solution feeding each part.
The point being that when we increase the plated area, the cross sectional area of the solution may not increase proportionately and therefore the effective resistance increases, and the voltage required to support a given ASF can increase. Without seeing your barrel, anodes, and tank it's hard to say for sure but I'm starting to think what you are seeing is not some weird phenomenon but just the fact that you'll need a higher voltage rectifier to plate more parts.
If you view the situation the way I just described it, you'll see that the surface area of the anode is basically the surface area of the face of the basket, plus some portion of the sides of the basket, not the total surface area of the S-rounds.
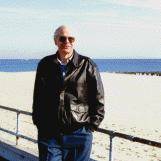
Ted Mooney, P.E.
Striving to live Aloha
finishing.com - Pine Beach, New Jersey
For anode baskets, I never assumed any more surface area than the front of the basket.
Other things not mentioned yet, are move the anode baskets closer to the barrel and shove all of the anodes in a box directly in front of the barrel. The basket that is a foot away carries virtually no current relative to the one closest to the barrel. Not totally true, but it is a good starting point.
- Navarre, Florida
1999
There is a wealth of good information contained in the above responses. I would merely add that power supplies won't put out more than 10% less of their rated amperage. Therefore your 100 amp rectifier will only put out a theoretical 90 amps. If you have 1.5 sq ft in your small barrel and you are applying 20 ASF then 30 amps total per barrel sounds right. If you then attempt to plate 3 times as much then you are looking at 4.5 sq ft at 20 ASF which then becomes 90 amps and your rectifier is now maxed out. If you consider that the above reasoning does not include other items such as bussing current carrying capacity, total circuit resistance, and all of the facts as noted in the previous responses, then your situation as described is no surprise. Spec. out your bussing, tank, etc. to match and get a bigger rectifier.
Ward Barcafer, CEFaerospace - Wichita, Kansas
1999
Q, A, or Comment on THIS thread -or- Start a NEW Thread