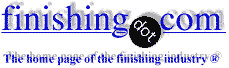
-----
Black Oxide Coating Thickness
Q. Hello Sirs,
I saw the answer you gave about the µm thickness of zinc, starting from the value of g/m2. My question is the same but I'm considering the black oxide coating of the guns.
On DIN 50934 "Black oxide coatings on ferrous metal components - Requirements and test methods" I read this coating can have from 2.5 g/m2 to 8 g/m2.
So how many µm of thickness?
Matteo Virgo
- Italy
November 18, 2022
A. Hi Matteo, there was a typo in your question, the correct spec number is DIN 50938. If your question reflects a concern about tolerances, you can probably dismiss your worries: the thickness is usually millionths of an inch rather than thousandths.
Zinc plating & galvanizing are essentially additive coatings where the thickness may be quite significant. Black oxide is a conversion coating where steel/iron on the surface of the substrate is converted to black oxide, and the reason it is given in g/m2 is because the thickness change, if even measurable, tells you little about what you have achieved.
Luck & Regards,
Ted Mooney, P.E. RET
Striving to live Aloha
(Ted can offer longterm or instant help)
finishing.com - Pine Beach, New Jersey
⇩ Related postings, oldest first ⇩
Q. I am outsourcing some components from Taiwan, and they have a difficult time maintaining a consistent plating thickness using zinc/chromate on the steel parts. I would like to consider using black oxide, but need to know more about the capabilities of the process. Will it build up on sharp corners like the chromate? Can the thickness be held to a tolerance of ± 0.0002"? What about color variation? Thanks,
Doug M [surname deleted for privacy by Editor]
- Radford, Virginia
1999
A. Hi Doug. Black oxide has virtually no thickness at all; it doesn't begin to approach 0.0002", so ± 0.0002" tolerance is no problem. And it will not build up on the corners either. But it will offer almost no corrosion protection.
As for color variation, that should be no problem unless you outsource the parts to a shop in Taiwan which doesn't have a good QA system tightly controlling any variations
It strikes me that the problem might be QA rather than inherent difficulties in zinc plating which you hope will be absent in black oxiding. Switching horses in midstream is a poor idea, the more so if the horses are unbroken :-)
Sorry for trying to be colorful in my answer, just trying to get across the idea that difficulties encountered in metal finishing usually aren't due due to the technical limitations of the process -- but simply poor practice. Best of luck.
Ted Mooney, P.E.
Striving to live Aloha
(Ted can offer longterm or instant help)
finishing.com - Pine Beach, New Jersey
A. Doug - Black oxide is a conversion coating, not a deposit type coating, so there is no dimensional change to the part and no potential for "build up". However, there is potential for color variation caused by inadequate cleaning before the black oxiding step. Complete removal of all soils and other oxides (rust, etc.) are critical to achieving un-mottled parts. Some black oxide products tolerate imperfect cleaning better than others - be sure to see samples of finished parts.
Dan Brewer
chemical process supplier - Gurnee, Illinois
Q. We are considering use of Black Oxide coating for the first time. For our ultra-clean needs, we need to know just how thick the oxide is on carbon steel. This info. doesn't seem to be presented anywhere. Does the thickness depend on the specification used?
DARREL LEMON
AEROSPACE - BOULDER, Colorado, US
2004
A. DARREL
Black Oxide is not a deposit, it is a Chemical Oxidation of the Steel, making the surface turn Black. It has almost no thickness, or at least any value as such.
This is one of the reasons it is used in gun barrels, because it doesn't change the dimensions of the parts to be covered. Also, It's of no protective value if it's not finished with a wax or oil.
I hope this helps,
Carlos
Carlos Cielak
plating shop - Mexico City, DF, Mexico
A. Hi Darrel. Please don't consider cold blackening, as this is the application of a smutty selenium coating which sounds highly unsatisfactory for ultra-clean needs.
Regards,
Ted Mooney, P.E.
Striving to live Aloha
(Ted can offer longterm or instant help)
finishing.com - Pine Beach, New Jersey
April 2018
Multiple threads merged: please forgive chronology errors and repetition 🙂
Q. Does black oxide on steel add to the thickness of the part? If so how much.
Thanks,
Ray Paolini
Medical products - Orchard Park, New York
2004
A. Hi Ray. It's somewhere between unmeasurable and a few millionths of an inch.
Ted Mooney, P.E.
Striving to live Aloha
(Ted can offer longterm or instant help)
finishing.com - Pine Beach, New Jersey
A. I also agree with Ted Mooney
The black oxide coating is a very thin layer.
T.S.N. Sankara Narayanan
- Chennai, Tamilnadu, India
(ed.note: The good doctor offers a fascinating blog, "Advancement in Science" )
Q. I need to plate spring steel parts. I have tried zinc plating with baking but it is making it brittle. Is black oxide plating a good solution. These parts are being used in fire panels. Will the parts last over a long period of time.
Neville
J. N. Wadia - Karachi, Pakistan
2005
A. I'm not familiar with 'fire panels', Neville, but black oxide offers no corrosion resistance beyond the oil that is used on it. Other options include dip-spin coating, autophoretic coatings, and mechanical plating. Hydrogen embrittlement can certainly come from zinc electroplating, but it can also come from an acid pickle or any cathodic process, and except in the case of ultra-hard steel it can almost always be relieved if the parts are baked immediately after the processing.
Ted Mooney, P.E.
Striving to live Aloha
(Ted can offer longterm or instant help)
finishing.com - Pine Beach, New Jersey
Multiple threads merged: please forgive chronology errors and repetition 🙂
Q. We recently just made some parts and sent them out to be black oxidized. Will this coating change the thickness of the part? Thanks.
Ben Knight
engineer - Birmingham, Alabama
September 24, 2008
A. No, Ben, it won't. The thickness is measured in millionths of an inch rather than thousandths or ten thousandths.
Regards,
Ted Mooney, P.E.
Striving to live Aloha
(Ted can offer longterm or instant help)
finishing.com - Pine Beach, New Jersey
Q. If there is no build-up how robust is the plating with regards to wear? My company is finding some parts look good at the beginning of the line and the coating wears off by the time it gets to the end of the line. This is just by handling and it's not excessive. Is there a test that can be done?
Thanks,
Bob
Robert Trottier
- Chester, New Hampshire, USA
April 27, 2011
A. Hi, Robert.
Black oxiding imparts color but not much else. The parts are oiled or waxed after the black oxide, and this is what gives some very minimal wear resistance and corrosion resistance. Still, if the coating is coming off, it may be a selenium-based cold blackening process rather than a true hot black oxide. These room temperature processes tend to be smuttier than real black oxide.
Firearms are often hot black oxided and, although it is not a robust finish, it doesn't come off quickly in that application. Many people have rifles that are decades old, as long as they are lovingly maintained.
Regards,
Ted Mooney, P.E.
Striving to live Aloha
(Ted can offer longterm or instant help)
finishing.com - Pine Beach, New Jersey
Q. How can we check if black oxide is okay or not?
Can we measure black oxide thickness by using DFT meter??
if not which instrument can we use to check black oxide thickness?
Please clarify.
Asha G
Quality engineer - Pune, Maharashtra
June 19, 2014
A. Hi Asha. Black oxide has virtually no thickness, but to my knowledge there is no need and no practical way to measure the thickness. The only QA measure I'm aware of offhand is visual checks and the oxalic acid spot test; but read the spec which you are processing to as it may have additional quality requirements. But if you apply a specific post treatment oil or wax or clearcoat, the finish can survive a short salt spray test, and you can require passing that test as a QA requirement. Good luck.
Regards,
Ted Mooney, P.E.
Striving to live Aloha
(Ted can offer longterm or instant help)
finishing.com - Pine Beach, New Jersey
A. Hi Asha,
In my experience I don't know regarding thickness of black oxide coating. I think thickness is not applicable.
Applicable two qualitative tests for black oxide coating are:
1. Oxalic acid spot test
2. Smut test.
One more Environmental test (salt spray test)
Regards,
Surya Narayana
Process Engineer - Tumkur , Karnataka , India.
Thanks Surya. It looks like the Oxalic acid spot test and smut test are included in AMS2485 and MIL-DTL-13924
[⇦ this spec on DLA]. The salt spray test only applies to type 3XX stainless steels, not carbon steel.
Regards,
Ted Mooney, P.E.
Striving to live Aloha
(Ted can offer longterm or instant help)
finishing.com - Pine Beach, New Jersey
Q. Dear seniors,
After blackening on steel metal how many microns dimension layer forms, or no dimension change after the process?
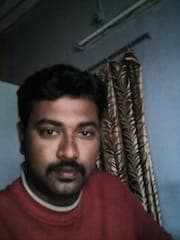
Hemanth kumar
- Karnataka, India
July 31, 2015
A. Hi Hemanth. We appended your inquiry to a thread which answers it: no significant dimensional change.
Regards,
Ted Mooney, P.E.
Striving to live Aloha
(Ted can offer longterm or instant help)
finishing.com - Pine Beach, New Jersey
Thank you sir. I got solution to my problem from your reply.
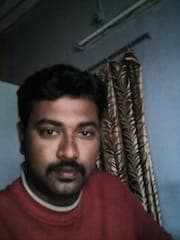
Hemanth kumar [returning]
- Karnataka, India
Black Oxide Smut Test
Q. Hello ,
I am come from Shanghai China , I have a problem about the standard of MIL-DTL-13924
[⇦ this spec on DLA] rev. D 18 March 1999, I don't know what is the SMUT TEST; I'm looking forward to have experts give me some professional explanation, thank you !
4.4 Test procedures.
4.4.1 Smut test. The test shall be made prior to application of corrosion preventive compound or after vapor degreasing. Each black oxide coated piece shall be inspected visually under strong light to assure a satisfactory appearance. Each sample shall also be wiped with a clean white cloth for indications of smut (see 3.7).
A slight amount of smut which is inherent in the process is acceptable for all classes of coatings and shall not be cause for rejection.
Ariven Chen
technical company - Shanghai , China
March 30, 2017
A. Hi Ariven,
Abnormal black oxide growing will easily cause smut formation affect reliability such as potential short between fine traces on printed wiring board if any smut particles fall off and stick between.
There's 2 easy ways to detect smut formation. One is use cotton rag to wipe black oxide coating gently to observe how significant darkish smut particles left on cotton rag. The other way is to immerse black oxide coated article into ultrasonic bath with DI water to observe how significant darkish smut particle escape from article and spread into DI water.
Regards,
David
David Shiu
- Singapore
A. After black Oxide coating (prior to application of rust protection oil), each sample shall also be wiped with a clean white cloth for indications of smut/ black color on white cloth. A slight amount of smut/ blackish strains on white cloth which is inherent in the process is acceptable for all classes of coatings and shall not be cause for rejection.
T. Chandra Sekhar Reddy
- Bangalore, India
Q. What equipment can be used to measure the thickness of BO?
Vasile DAN
- Romania, Ploiesti
February 26, 2018
by Biestek & Weber
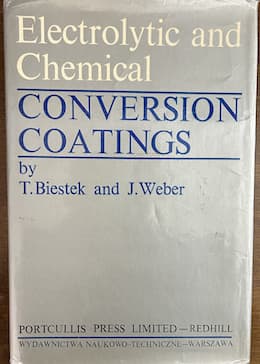
on Amazon
on AbeBooks
(affil link)
A. Hi Dan. I guess as we increasingly move towards micro-minaturization, the old answer of "negligible thickness" may prove inadequate.
Actually, Robert Farrell asserts in the 2002 Metal Finishing Guidebook, that "The actual dimensional change that does occur has been measured and is approximately 5 millionths of an inch [0.13 µm]".
Biestek & Weber's Conversion Coatings.
claims that "Most suitable are coatings with a thickness of 0.6 to 0.8 µm".
But I don't see where either describes the thickness testing method though :-(
Regards,
Ted Mooney, P.E. RET
Striving to live Aloha
(Ted can offer longterm or instant help)
finishing.com - Pine Beach, New Jersey
Q. Can an Iron donor be used in a hot caustic bath to increase the thickness of black oxide coating? For a basic bath formulation of Sodium hydroxide and Sodium nitrate, what if I add Ferric Nitrate after the reaction stops, will sodium hydroxide reduce the ferric nitrate and add thickness to the existing magnetite layer or will I simply have iron oxide precipitate but no layer thickness increase?
Igor Petrusky
- Stuart, Florida
April 24, 2018
A. Hi Igor. According to Biestek & Weber again, you can get thicker coatings even more simply by just raising the temperature (which means raising the concentration) ... but the problem is that the thicker coatings are not useful because "they are poorly developed and covered with a loose deposit of hydrated ferric oxide".
Although I don't have the combination of time, interest, and chemistry knowledge to completely follow their presentation, again they claim 0.6 to 0.8 µm is the most useful thickness, and they seem to feel that the upper limit on useful coatings is inherent because of required interaction with the substrate. Good luck.
Regards,
Ted Mooney, P.E. RET
Striving to live Aloha
(Ted can offer longterm or instant help)
finishing.com - Pine Beach, New Jersey
Q. Ted,
What I understood from online readings is that increase in bath temperature produces deposits of Fe2O3 instead of magnetite. This loose red rust is the reason for thicker coating, however it is hardly comparable to magnetite layer for strength and usefulness. My goal is to try and deposit a thick, dense layer of Fe3O4 to produce a longer lasting and stronger protection layer than normal caustic bath creates.
Igor Petrusky [returning]
- Stuart Florida
April 24, 2018
A. Hi again, Igor. That's a fine goal and you may be able to achieve it :-)
All I am able to comment is that the one reference I have that attempts to investigate the chemical reactions driving the conversion chemistry seems to be saying (to my limited understanding) that it won't work: because once the substrate isn't exposed anymore, the proper reaction cannot continue :-)
Regards,
Ted Mooney, P.E. RET
Striving to live Aloha
(Ted can offer longterm or instant help)
finishing.com - Pine Beach, New Jersey
Q. Just want to ask here for professionals. We are in metal stamping industry, and we have a part produced (material is Carbon steel SK5M annealed) where process involved after stamping is heat treatment, tumbling and black oxide. The final process is black oxide. After receiving the part, we were surprised that some parts are out of specification for the material thickness.
Thickness is 0.30 mm +/- 0.04 mm: Some found thickness of 0.16 to 0.20 mm thickness out of specification. Reject percentage is around 10%. Could you help us digest what is the root cause for the thickness out of specification. Is it during black oxide?
Miguel Tom
- Kallang Pudding Rd Singapore
October 27, 2022
A. Hi Miguel. The black oxide process per se is certainly not the cause of the steel being too thin or getting too thin. Black oxide process tanks are usually made of mild steel and remain in service for decades -- indicating that the black oxide solution does not attack or dissolve steel at all, let alone by 0.10 to 0.14 mm from a short immersion.
However, if the steel is immersed in a strong acid tank with no inhibitors as part of a preparatory process before black oxide, it could dissolve to some extent. But unless I knew otherwise, I'd probably suspect that the steel was below the thickness spec before the process started :-)
Luck & Regards,
Ted Mooney, P.E. RET
Striving to live Aloha
(Ted can offer longterm or instant help)
finishing.com - Pine Beach, New Jersey
Q, A, or Comment on THIS thread -or- Start a NEW Thread