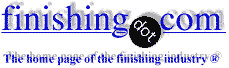
-----
Topcoat ideas
We have a zinc-nickel-bronze plating line that includes a chromate conversion coating. This is an "in-house" plating facility. We plate mainly power steering components on this line. We have been tossing around ideas on inexpensive ways to increase the corrosion resistance of our products. We would like them to perform better in our customer's complex corrosion testing and in service.
We have been investigating the possibility of adding some sort of topcoat at the end of our plating line. We are looking for a simple dip process so that no extra investment in new equipment is required. We have a list of technical requirements that also need to be met (fluid compatibility, thermal resistance, dimensional constraints...) We are hoping for 15 to 20% improvement in corrosion resistance at a reasonable cost. The one option we have started looking at is a lacquer that seals the chromate. I would welcome any suggestions that you have to make. Thanks!
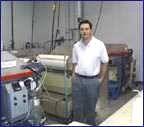
Tim Neveau
Rochester Hills, Michigan
1999
Timothy, It is not difficult for alkaline Zn-Ni plating with yellow/iridescent or black chromating to pass 500 hrs on white rust and 1000 hrs on red rust, to my experience. I believe this performance can meet the requirements for most applications. I would like to suggest you to switch to alkaline Zn-Ni plating if you are using acid chloride Zn-Ni plating and turn to iridescent or black chromating from bronze chromating. This switch will not require additional equipment but improve performance substantially. Thin topcoats do not help very much in enhancing corrosion resistance but make production hard to control consistent quality.
Good luck! Ling
- Grand Rapids, Michigan
1999
1999
Hi Timothy ,
In part I agree with Ling , that by using a properly formulated Yellow Chromate on top of your Zinc - Nickel alloy plating you will achieve good corrosion resistance , forget Black chromates , a lot poorer corrosion protection than the newly formulated yellow ( iridescent ) chromates . and usually much more expensive to run .
However , the application of waterborne and correctly applied acrylic & Vinyl coatings can substantially improve the life of a Zinc ( Zinc alloy ) chromated finish .
The product I am most familiar with is called TINTAC "C" it is a waterborne acrylic finish from the Kenvert range now sold by Macdermid , but I am sure other vendors will have similar products. As a judgment , I have always found that the waterborne Acrylics out-perform the waterborne Vinyls .
As a word of warning there is a body of thought out there that says beware of believing accelerated corrosion testing results, in that they bear no resemblance to what actually happens in practice especially when comparing zinc & Zinc alloy finishes !
Best regards

John Tenison - Woods
- Victoria Australia
Q, A, or Comment on THIS thread -or- Start a NEW Thread