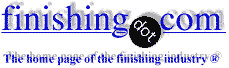
-----
How to Hard Chrome Plate on Aluminum
I am looking for the preferred method for application of Hard Chrome on aluminum (356-T6) casting. Area to be plated 1 1/2 inch inside diameter up to 2 inch depth. Plating thickness (.010-.012). Good adhesion needed for grinding after plate.
Henry Livings- South El Monte, Ca.
1999
Dear Henry Livings I have tried to plate hard chromium on Al (Al-Si) as well. I saw that good adhesion with ZnO plating for about 10 sec. then chrome plating. You may try this. best wishes
Mustafa Demirciplating company - Istanbul/Turkey
1999
For my nickel, the best may not be the optimum. A high quality zincate is a must. Literature that I have read, says that a ternary zincate works best. This has just enough cyanide to cause waste treatment problems, so consider a double zincate where you get professional help and training in the startup and training of your operators. A lot of the QC is visual.
An electroless nickel strike is excellent. A problem is, it is difficult to get all of the chrome off of the rack coating and just enough will come out in the EN to prematurely kill it.
I would look at EN after the strike and eliminate the grinding.
If you chose to chrome, internal anodes are suggested to get a more uniform coating than you can get from tank anodes. Rack design becomes very important since nickel passivates quite rapidly, especially if it becomes dry.
The proper grit and resin wheel is extremely important. The max recommended cut is 0.0002 per pass. On aluminum, it is even more important since there is a great difference in the coefficient of thermal expansion between aluminum and chrome.
- Navarre, Florida
1999
Hi Henry,
All that Jim Watt says is correct, but I would question your choice of coating, a much better choice would be electroless nickel, you could plate it up and negate the need for grinding which is where your problems will begin if you go the Hard Chrome route, if the coating is for both frictional & Corrosion reasons then choose EN with PTFE occluded in the deposit .
Best regards

John Tenison - Woods
- Victoria Australia
1999
Q, A, or Comment on THIS thread -or- Start a NEW Thread