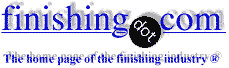
-----
Corrosion problem in CDR plant
2004
In this plant, we have CDR (CO2 dioxide recovery) plant for recovering CO2 from the flue gases which are coming from Primary reformer furnace of ammonia ⇦ on eBay or Amazon [affil link] plant. These gases are at a temperature of 165 °C and contains 12% CO2. CO2 is absorbed in an absorber using MEA (Mono Ethanol Amine) solution, CO2 Loaded MEA solution is then sent to Stripper for regenerating MEA for reuse whereas CO2 separated is sent to the user i.e. Urea plant.
This plant was commissioned in 1991 and since then, we are facing the problem of high corrosion in CDR plant. Iron in circulating MEA solution remains normally between 10-15 PPM. To maintain the iron level with in the limit, we are force to drain part of the MEA solution and fresh make up is charged. We had been using CuSO4 based corrosion inhibitor.
Can you suggest what can be the root cause for the corrosion problem in Amine based CO2 recovery process and remedial actions for the same or any better corrosion inhibitor. We are sending our observations for the same Corrosion Mechanisms in Amine Unit:
Formation of heat stable salts:>
In the presence of oxygen, MEA will decompose to form organic acids such as oxalic acid, acetic, glycolic and glycinic acid. All of these acids form salts with amines in solution, but these salts are not decomposed in the amine regenerator or stripper, thus the name ¡§heat stable salts¡¨. These salts build up in the amine solution and become corrosive as unit operating temperatures increase. The areas in Amine unit that are attacked most aggressively by corrosive amine solutions are hotter regions, the bottom of the stripper tower, the stripper reboiler tubes, and the transfer lines from the strippers bottoms to the reboiler or to the lean/ rich exchangers.
Corrosion is likely to occur wherever acid gases are boiling out of the rich amine solution. The areas of unit that experiences this kind of attack are the rich side of the lean/ rich amine exchangers, the amine stripper trays, and sometimes on the stripper reboiler tubes.
Erosion/ Corrosion
High rates of metal loss are sometimes experienced in amine units where there is high level of solids in the circulating amine solution. These solids are usually corrosion products and are typically present in units that do not have an effective amine filtration system in use. This type of corrosion occurs because the protective layer of corrosion product scale is removed by erosion in high velocity areas, which allows continued high rates of corrosion attack by the corrosive amine solution. The most common areas for this type of corrosion attack to occur are stripper reboiler tubes, flow control valves, amine pump impellers and amine line elbows and Tees.
Hope you will provide your valuable feed back.
Regards
Ajai Dwivedifertilisers / manufacturing urea - Jagdishpur, UP, India
Dear Ajai:
I had extensive experience with CO2 Removal when working in Ethylene Oxide. Basically a CO2 Removal Unit uses the Benfield process where CO2 is absorbed in a Potassium Carbonate solution which is regenerated using steam.
The corrosion/ erosion is successfully controlled with Vanadium Pentoxide.
Good luck
Vinh
Vinh Le- LaCrosse, Wisconsin
2004
2004
Dear Ajai,
Why don't you consider removing the cause of the corrosion i.e. the Heat Stable Salts. You could use ion exchange technology also called HSSX.
Besides preventing corrosion it could also prevent the MEA make-up.
Kind regards
Sjaak van Veelen- Vlaardingen, The Netherlands
We got a fouling and scaling in our lean / rich (plate) heat exchanger (scaling and fouling in rich side). The main of deposit components are 45.11%wt as Fe; 31.45%wt as Loss on ignition include CO2; Others (small quantity): Ca, Cr, SiO2, Ni, V, Sb, SO3.
Note:
Those problem occur when we use MDEA as amine solution (2 times of scaling problems in 2003 - 2006 period), but we didn't get the problem when we use MEA as amine solution in 1998 - 2002.
Could you give us the advice what happens in our CO2 removal system?
How to prevent the problem in the next operation?
- Gresik, East Java, Indonesia
2006
2006
The corrosive agents are the very acid gases (H2S & CO2 ) that are the reason for the existence of amine systems. Heat Stable Salts and amino acids enter with the gas or are produced within the amine system and contribute to corrosion. Many heat stable salt anions and amino acids are well known to make complexes with iron. The complexes are formed by the reaction:
Fe(H2O)6+2 + n(anion) <--> Fe(anion)n(2-n) +
(6-n)H2O
where n = 1 to 6
The reaction shifts toward complexation by increasing the anion concentration or by increasing the hexaquo iron ion in solution. Anions such as thiocyanate, formate, and acetate, common amine heat stable salt anions readily form iron complexes. The complexes then cause the dissolution of iron sulfide to shift to the right providing more iron ions for complexation.
Iron carbonate and iron sulfide are more soluble on the lean side. HSS and/or degradation products will cause iron carbonate and iron sulfide to become soluble in the lean side of the system. When the amine is circulated back to the contactor and picks up CO2 and H2S, the iron carbonate and iron sulfide will precipitate out leaving the HSS and/or degradation product free. This free complex former is circulated back to the lean side where it picks up more iron. This cycle can repeat itself over and over and may cause severe corrosion on the lean side of the amine treating system. Furthermore, the precipitated iron carbonate and iron sulfide can plug trays in the contactor impacting operation or they end up in the (plate and frame) heat exchanger.
HSS and amino acids can result in:
- corrosion
- Solids / deposits
- Reduced amine capacity
- Higher chemical cost / losses
- Operational gap for the plant (lost profit)
HSS cause(s)
Heat Stable Salts (HSS) are any ionic substances that are NOT substantially removed from the alkanolamine solution by heat (in the regenerator or "stripper" of an amine system). This definition is not restricted to salts that arise from reactions with contaminants absorbed in the contactors. It includes as well salts arising from addition of "neutralizers" and other special additives, salts that enter the amine from cooling water leaks, etc.
The HSS are generally identified by the name of the anion of the ion pair, because the cation is generally protonated amine. The variety in mechanisms is in the formation of the HSS anions.
Modes of HSS Accumulation in Alkanolamine System:
1.Reaction of HCN (hydrogen cyanide) and/or organic nitriles Examples: formate, acetate, thiocyanate
2.Oxidation of H2S Examples: sulphate, thiosulphate
3.Absorption or addition of strong acid anions.
Examples: chloride, sulphate, phosphate.
4.Oxidation and cleavage of the alcohol of the amine
Examples: formate, oxalate, acetate
5.Hydrolysis of CO (carbon monoxide), catalysed by metals
Example: formate
Very low concentrations of the primary reactants in the process gas lead to gradual buildup of HSS.
- Vlaardingen, Netherlands
2006
Does this explain what happen in Wim D Verduijn paper
"Corrosion of a CO2 Absorber tower wall" excellent paper printed July 1983 in Plant/Operations Progress Vol 2 No 3 In it he discusses Corrosion of a pot carb process and its extreme corrosion rates ?
If not what is the process for the corrosion?
what is the modern thinking?
- Brisbane, Queensland
2006
Piperazine in MDEA solution. Our CO2 removal unit is using (activated) MDEA solution, the main components are MDEA; piperazine (as activator), water and some impurities.
Would you like to give us the analysis methods to measure the piperazine content in MDEA solution?
Would you like to explain the philosophy of analysis procedure?
best regard,
- GRESIK, Indonesia
My Question in CO2 removal unit by benfield solution we added meta vanedate for corrosion protection,Each addition we observe that V+4 increased with increasing V+5 while Fe concentration constant.
Thank you
fertilizers - Alexandria, Egypt
February 27, 2009
What is best corrosion inhibitor can be use or in use for MEA system
salman BhattiStudent - panama city, Florida, USA
July 15, 2009
March 2, 2011
My dears,
At the downstream of one of our NGL plants there is an amine sweetening unit for sweetening of our sour natural gas. The acidic compounds which are absorbed from the sour gas are mainly hydrogen sulfides and carbon dioxides. Other sulfuric compounds such as mercaptans, carbon disulfide and CoS are also present in the sour gas. The amine employed in the unit is Di-Ethanol-Amine. Recently we have observed some black and sticky sediments which were first shoe polish like compounds, but then turned into hard compounds as were permitted to contact with air. They seem to be polymeric compounds. They dissolve plastic bags and make with them a uniform and homogeneous matter. The black sediments are highly corrosive.
Would you please let me know if anybody has observed such sediments in his unit or not. If you have encountered with this problem earlier, would you please let me know what are they composed from and how we could prevent them from their formations? Thank you, Dr. B. Hashemi Shahraki
Prof. In Chemical Engineering - Ahwaz, Khoozestan, Iran
Q. Is it possible to use Magnetic filter for Benfield solution filtration? What will be advantages and disadvantages of installing magnetic filter along with carbon filter?
- Pakistan
December 22, 2011
Q, A, or Comment on THIS thread -or- Start a NEW Thread