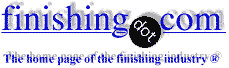
-----
How high quality plating on plastics is done, with problems and solutions
by Ted Mooney, P.E. RET
Quickstart:
Not everything that looks shiny is actually electroplating ... it may be vacuum metallized aluminum or "chrome look paint", for example. You may wish to see our FAQ "Introduction to Chrome Plating" to understand the general issues of chrome plating vs. some alternative technologies.
Almost anything can be electroplated, and there are at least a half dozen alternate procedures that can be used to make plastics conductive so that they can be electroplated. For an introduction to those various metallization methods, please see our FAQ "How to electroplate flowers, leaves, animal skulls, and other organic materials".
This particular thread addresses and discusses the issues involved in very high quality decorative plating on plastics, such as the nickel and chrome plating of automobile grills and exterior brightwork ...
Anything can be plated, but adhesion is usually a key issue!
Consider for a moment the situation of a nickel and chrome plated automotive grill. In this case you have a layer of metal (relatively low expansion with temperature change) deposited onto plastic (very high coefficient of expansion). The car may sit out in an Alaskan winter at temperatures way below zero, travel to Death Valley with temperatures of 130 °F, and sun so strong that you'll burn yourself if you touch the grill. In between, the car may go to car washes with scrubbing brushes, or suffer exposure to corrosive road salt, flying gravel, incidental contact with steam cleaning, etc. For the metal plating to adhere without bubbling, blistering, chipping, peeling, corroding, or wearing through in the face of decades of this abuse requires fantastic adhesion (courtesy of ABS plastic which can be etched to a sponge-like surface for terrific tooth), very robust and usually proprietary pretreatment and metallization cycles (consisting of steps like etching, activation, acceleration, and electroless nickel plating), and very high quality electroplating (a sequence of copper plating, semi-bright nickel plating, bright nickel plating, and chrome plating).
by American Society for Electroplated Plastics
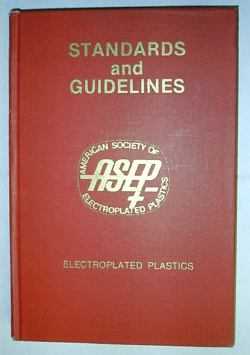
on eBay or Amazon
or AbeBooks
(affil link)
ABS Plastic (acrylonitrile butadiene styrene) is the preferred plastic for plating!
ABS is an engineering plastic with a number of outstanding properties (see wikipedia.org/wiki/Acrylonitrile_butadiene_styrene), but the property that makes it attractive for plating onto is that, because it is comprised of three different monomers, it is possible to expose it to an etching chemical (chromic-sulfuric acid) which will dissolve the butadiene portion, leaving a spongey, toothy surface which the electroplated metal can really lock into.
Pretreatment and metallization -- not conductive paint!
1). ABS is first etched in chromic-sulfuric acid to dissolve the butadiene.
2). After neutralizing, the plastic parts are "catalyzed", i.e., a catalyst, tiny seeds of palladium ions, is formed on (and in the sponginess) of the plastic via a series of steps. Generally the parts are sequentially dipped into a proprietary solution of palladium chloride and a proprietary solution of tin chloride, and the tin reduces the palladium ions to metal, and then the excess tin is washed away. The terms "activation" and "acceleration" are sometimes associated with these steps, but it must be continually emphasized that these pretreatment cycles are invariably proprietary: most cycles use an acid pre-dip before activation to prolong their life and stabilize them; some pretreatment cycles may not require 'acceleration' (or at least don't use that word), etc. So some people like to simply use the word 'catalyzation' to cover all the steps and process sequences involved in getting the palladium seeds in place and ready to go.
3). Next comes the autocatalytic Electroless nickel process. The parts are put into this solution, which is sort of "spring-loaded"; it contains reducing agents that are triggered both by the palladium seeds and by the deposited nickel, so that the palladium triggers the nickel to start depositing, and the deposited nickel triggers it to keep going, depositing a uniform layer of nickel. It keeps going until the parts are removed from the tank.
The central idea in this metallization approach is that metal ions permeate right down to the spongey plastic and electrochemically grow into metal from there. There is no layer of conductive paint which could limit the adhesion of the plating to the plastic. While a conductive paint layer between the plastic and the plating might prove perfectly acceptable for many applications, it's not adequate for exterior automotive brightwork.
Update: Direct metallization!
Copper, semi-bright nickel, bright nickel, and chrome electroplating!
Parts which are intended for exterior automotive use are then copper plated after the electroless nickel process, then duplex (double) nickel plated, maybe triplex nickel plated, and finally chrome plated.
The copper is not for corrosion resistance, but to offer a relatively a soft layer between the electroless nickel and the electrolytic nickel plating to help absorb the stresses caused by the different thermal expansion coefficients of metal and plastic. Then two (or more) separate layers of nickel plating offer maximum corrosion resistance as explained in the previously mentioned FAQ, "Introduction to Chrome Plating). And finally the chrome plating. Some automotive specifications may require some additional intermediate steps, but they always include the copper, semi-bright nickel, bright nickel, and chrome plating steps.
The design of the part and the condition of the substrate matters!
For example, a part which is designed with incorrect draft, or which has sections that are too thick or too thin, may be difficult or impossible to plate correctly. The part must allow contact areas with the plating rack, and must be free of cup areas which hold plating solutions or trap air or defy good rinsing. The plating goes where the current goes, and the current takes the path of least resistance, so there are limits to how deep the recesses may be. A part which is not molded of "plating grade" ABS may not etch or plate properly.
The editor has experience in plating on plastics, but doesn't claim to be a world-class expert. Rather, we offer this introduction to the dialogs just to help set the stage as the Q&A's bounce from one issue to another; so feel free to use the dialog to correct or challenge any misstatements you find here.
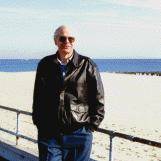
Ted Mooney, P.E.
Striving to live Aloha
(Ted is available for instant or longterm help)
finishing.com - Pine Beach, New Jersey
Q. Dear Sir,
We are doing Electroless Nickel plating and then Copper-Nickel-Chrome Plating on ABS Plastic. We are giving a minimum of 45 microns thickness of total plating. We don't know the detailed procedure of plating.
We are facing some problem with products (after finish metal plating):
1. pin holes (small holes in plating surface)
2. adhesion strength (after thermal cycle)
So, We would like to know what is causing these defects and how to prevent them (both resin and plating.
And, also I want to know the book or library addressing the mechanism of metal plating of ABS plastic.
Yours faithfully,
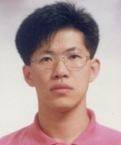
Kyungho Cho
- Uiwang, Kyung Ki, Korea
2004
A. Since you cannot provide any technical details of the process, I can only speculate on your problems. Pin pricks in electroless plating can be due to many causes. Firstly the ABS may be the wrong grade or be moulded under the wrong conditions. The holes could also be due to inadequate cleaning of the moldings prior to electroless plating. This could be due to the presence of mould release agent or other surface contamination. The pin pricks could also be due to the non-release of the hydrogen bubbles generated during the electroless nickel process - this could be due to the bath being out of specification or inadequate agitation. Failure during thermal cycling can be due to inadequate bonding between the ABS and electroless nickel, or bond failure between the numerous metal-metal interfaces, or quite simply the temperature range being too great. Remember that the expansion coefficients for ABS and metals are very different. One tip, - when I have done electroless PoP, I have tended to use slightly compressive nickel, as this seems to assist adhesion in thermal cycling. There are numerous books on the metallisation of plastics, some of which are listed in the "must have" bit of this website, so have a look and see what you can get.
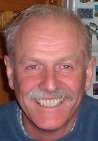
Trevor Crichton
R&D practical scientist
Chesham, Bucks, UK
A. "Trouble Shooting Decorative Electroplating Installations part 4: Plating on Non Conductors" by N.V. Mandich and D.W. Baudrand, Plating and Surface Finishing magazine September 2001 Journal of the American Electroplaters Society (AESF) covers the questions you are asking. This should be available from a Library.
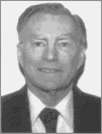
Don Baudrand
Consultant - Poulsbo, Washington
(Don is co-author of "Plating on Plastics" [on Amazon or AbeBooks affil links]
and "Plating ABS Plastics" [on Amazon or eBay or AbeBooks affil links])
A. We find the most common cause of "pinskip" to be airborne chrome from the chrome tanks if sufficient wetter is not present. There should be a thick foam blanket upon the chrome bath and exhaust system setup to draw in the air.
Jason Kcolhsa- USA
Q. Hi, I'm a student doing my final year project. I'm currently doing EN on ABS. I just want to ask about the pretreatment of the ABS before EN.
Thank you
Student - Johor, Malaysia
February 3, 2009
A. Hi Muhammad. We've now added an Introduction section to this page which should answer your questions.
Hunt through the university and town libraries and see if you can find a copy of "Standards & Guidelines for Electroplated Plastics". This will describe all of the typical methods for etching, sensitizing, and activating before electroless nickel plating, etc. Also, keep alert for current technical articles as the pretreatment of plastics is evolving to try to make it more economical, ecological, and applicable to additional types of plastics. Good luck.
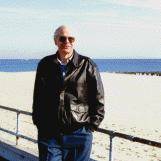
Ted Mooney, P.E.
Striving to live Aloha
(Ted is available for instant or longterm help)
finishing.com - Pine Beach, New Jersey
Q. Hi
I have a few parts made of ABS. I'm planning to start my own plating on plastic project. I have looked for some material from internet, but I'm not yet sure what exactly has to be done (e.g which element, in what concentrations, temperature and time lapse between progressive tanks and many other questions).
Is there a guideline online or some text book, which I can study to start up my experiments?
Or can anyone help me with all the standard procedures?
techmen - lahore, Punjab, Pakistan
December 17, 2012
A. Hi Saad. I think the best reference is the book I just mentioned. People take months or years writing a book, with the expectation of being compensated for all that effort, so it is always more comprehensive, more authoritative, and more tutorial than any web page or forum article.
But if you want to try to piece it all together, you can start with this page as a framework of what the overall process is about, then hunt for additional detail on each of the steps. Best of luck!
Regards,
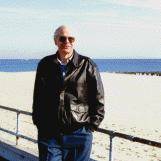
Ted Mooney, P.E.
Striving to live Aloha
(Ted is available for instant or longterm help)
finishing.com - Pine Beach, New Jersey
Q. Sir,
I want to know how thick the electroless nickel layer should be for copper plating.
- SHIMLA, India
December 29, 2012
Q. Hi.
I would like to make an auto motive parts like an emblem which is put on fuel tank motorbike. It is made in ABS plastic and finished by gold plating I need complete process to create this article can you help me ?
- Karachi Sind Pakistan
January 21, 2013
A. Hi Noman. The complete process is etch > activate > accelerate > electroless nickel plate > acid copper plate > semi-bright nickel plate > bright nickel plate > gold plate, with rinsing between each step.
But each of these steps makes a good chapter in a plating text, and almost all plating shops use proprietary plating solutions rather than generic home-brew. So your quest for "complete process" details is probably beyond what you can receive. You can probably do it, but it will be a development effort of months under the guidance of a plating consultant rather than a few minutes of reading the forum. If possible, contact a major supplier of plating processes as they will have all of the processes for you, although they will retain the fine details as trade secrets. Good luck.
Regards,
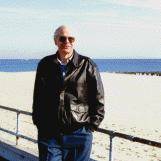
Ted Mooney, P.E.
Striving to live Aloha
(Ted is available for instant or longterm help)
finishing.com - Pine Beach, New Jersey
Why is copper plating of ABS more difficult than nickel plating?
by N. Kanani
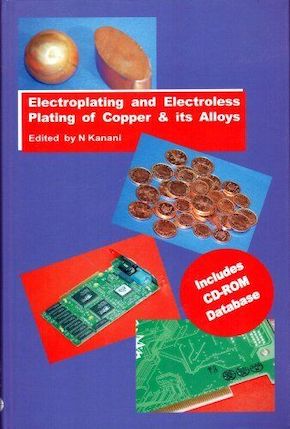
on eBay or Amazon
or AbeBooks
(affil link)
Q. Hi. My work involves copper plating on ABS plastic. I have heard that nickel plating on ABS is relatively easier to achieve than copper plating. What is the reason for this?
Rameez Malik- Odisha, India
December 9, 2015
A. Good day Rameez.
There have been to date no replies, and I thought I would throw something at you. The only reason I can think of is if the copper is applied electrolytically, and the ASF is too high initially, you can "burn" through the metallization on the surface. As thickness builds, you can ramp up the ASF to the desired range. This may be why electroless nickel would be easier, in my opinion.
Hope this helps.
Regards,
Eric Bogner, Lab. Tech
Aerotek Mfg. Ltd. - Whitby, Ontario, Canada
A. Eric, my guess is that Rameez is referring to electroless copper vs. electroless nickel.
Hi Rameez. "The grass is always greener on the other side of the fence."
But, yes, in the early days of electroless plating, electroless copper was sometimes used in decorative plating; these days to my knowledge it is only used on circuit boards where the conductivity of copper is required. It is apparently more difficult to control.
Regards,
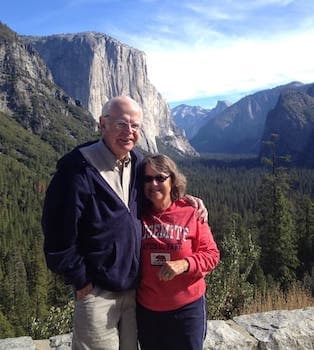
Ted Mooney, P.E. RET
Striving to live Aloha
(Ted is available for instant or longterm help)
finishing.com - Pine Beach, New Jersey
Copper Plating doesn't adhere to the metallization at high current density
Q. I was electroplating a plastic piece with copper (after making it conductive). On increasing the current density the copper plating started turning black. Even if the density was reduced to reduce the black colour formation, the adhesion strength of the coating was very weak. It could be peeled off by just scraping with your hand. But on lowering the current density considerably the coating adhesion increased. How is current density affecting the coating adhesion?
Rameez Malik [returning]- Odisha, India
June 8, 2016
by John McDermott
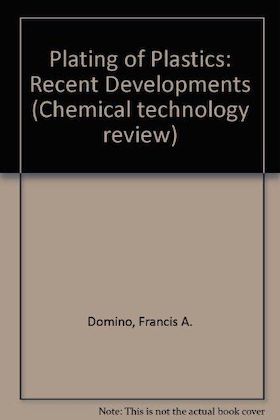
on eBay or Amazon
or AbeBooks
(affil link)
A. Hi Rameez. How did you "make it conductive"? Are you sure that the 'burning' you created did not affect the metallization layer you had applied? Burning causes tramp contaminants to co-deposit which would not have been deposited at lower current density; it causes the evolution of excess hydrogen gas at the surface which might affect the topography of the joint. But with no disrespect, I think you may be poorly framing the question because electroplating is in large measure an empirical science; so when things are done wrongly or poorly, and it consequently doesn't work, the question of "why" may be unanswerable, and the only meaningful answer may be "do it right instead" :-)
But if you want to continue the discussion anyway, we'll need a lot of data on the plastic, the metallization, the copper plating solution, etc.
Regards,
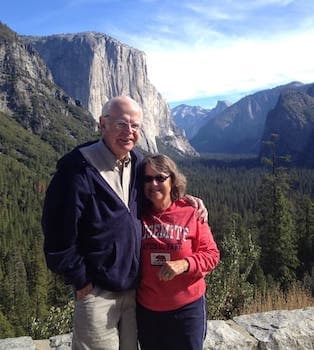
Ted Mooney, P.E. RET
Striving to live Aloha
(Ted is available for instant or longterm help)
finishing.com - Pine Beach, New Jersey
Q. The plastic was ABS Plastic and the solution was supersaturated copper sulphate ⇦ on eBay or Amazon [affil link] solution. I am a novice and wanted to experiment so tried electroplating different pieces of the plastic at different current densities and found that on increasing the current density, the adhesion strength of the plating decreased as well as the plating turned black. I could not find a valid reason for this. Hence, I want to know is there a general relation between the plating current density and plating adhesion achieved.
Rameez Malik [returning]- Odisha, India
A. Hi. I'm still not hearing what method you used to make the ABS conductive :-(
At low current density there is probably no relationship between current density and adhesion. But as you get too high, copper ions cannot move from the solution, through the boundary layer, quickly enough to satisfy all the electrons accumulating on the cathode. They can't migrate fast enough. So those electrons start getting satisfied by electrolyzing the water of the solution into H2 and 2OH, which causes 'burning' (blackening, rough surfaces, and poor quality of deposited metal).
Unfortunately, as previously noted, there is a lot of empirical knowledge involved in the science of electroplating. So usually we cannot say from first principles what the satisfactory upper limit for current density is; rather we only know what works and what doesn't. Plating at greater than about 30 ASF usually starts getting problematical unless you can apply extreme agitation to thin the boundary layer. But I personally feel that you are burning and destroying the underlying metallization layer which you are not describing -- it is quite possible that the metallization you applied is not capable of carrying the current you are using and is being destroyed. Try plating at very low current density for 5 minutes until you have some significant copper on that metallization to sustain higher currents. Good luck.
Regards,
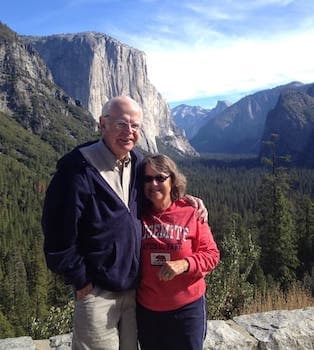
Ted Mooney, P.E. RET
Striving to live Aloha
(Ted is available for instant or longterm help)
finishing.com - Pine Beach, New Jersey
Q, A, or Comment on THIS thread -or- Start a NEW Thread