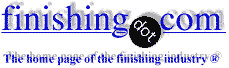
-----
How to formulate parkerizing solution?

Q. Dear Sir,
I'm from the Philippines & interested in the formulation of Parkerizing solution, generally used on firearms & most metal protective finishes. Currently, I'm into restoration of old motorcycles, especially Antique Harley Davidsons. Since most suppliers of "Parkerizing solutions" in U.S. cannot ship their products, I would just formulate my own and maybe introduce it to other gunsmiths & restorers as well. It's colors are usually grayish, greenish or black. They also call it Manganese phosphating. It would be a lot of help to have a do-it-yourself finishing solutions for us here.
Thank you very much & hope for your response.
Conrad Peralejo- Quezon City, Philippines
2001
A. INSTRUCTIONS FOR "HOME-BREW" PARKERIZING:
You need a number of things to do a "home-brew" "Parker-job", but only 4 ingredients.
1. Phosphoric Acid (the active ingredient in
naval jelly
⇦ on
eBay or
Amazon [affil link]
) usually procured at a chemical supply house.
2. Powdered Manganese Dioxide (a very dense and heavy dark gray to black powder) also available at any chemical supply house.
3. Distilled water (I've used tap water, but the distilled stuff gives more consistent results).
4. A biscuit of #0000 steel wool
⇦ on
eBay or
Amazon [affil link] (don't use soap pads or Brillo pads!)
I used to do this on the kitchen stove (I wasn't married in those days) in a one gallon Pyrex beaker (these little beasts are expensive, so be careful with them). Metal pots don't work as well (if at all) I understand, but then I never used anything else but Pyrex.
Proceed as follows:
1. Use one whiskey jigger (yeah, this is really scientific, right?) of phosphoric acid added to the water. Remember your high school chemistry, ALWAYS add the acid to the water, and it is best done by pouring it down a glass rod!
2. Use one whiskey jigger of the (powdered) Manganese Dioxide in the solution.
3. Bring the solution to an extremely slooowwww rolling boil .
4. Now add your biscuit of steel wool.
I used wooden sticks placed across the top of the beaker and suspended the parts in the solution using steel or iron "machinist's wire or some such. DON'T use painted coat hangers or any wire with grease on it! You can usually get this stuff from a machine shop or from Brownells [ Brownells home page (affil link) ] .
The parts should be totally immersed in the solution, being careful that anywhere the wire touches the part won't show on the finished part (usually easy to do -- like in the firing pin hole of a bolt). The part(s) to be Parkerized should be totally "de-greased" and sand or bead blasted prior to finishing (depending on the texture you desire on the finished part). Once you have bead blasted the part, you should handle the part with gloves (never greasy hands) and store them wrapped in clean paper towels awaiting the Parker Bath. Any grease on the parts or wire will cause what can only be politely called a variation in color (the parts come out streaked and spotted like a "paint horse").
I usually let the part remain in the solution for a total of 20 minutes (less MAY work, but I was told 20 minutes so that's what I used and it worked marvelously). When you withdraw the part, immediately rinse it in hot running water to get the solution off of it. Use extremely hot water, and the part will dry itself. Let it dry (and get cool enough to touch) on some clean paper towels, spray on some lubricant and voilà you are done!
Rumor control said that if you immersed the freshly rinsed and still hot part in Cosmoline, it would give the sometimes sought after "gray-green" tint to it. I have never tried it.
The original formula called for iron filings [affil link] vs. steel wool, but since I didn't have any floating around, and didn't want to file on the cast iron stove, I found that the steel wool worked just fine. What you get is a chemical reaction that causes an iron phosphate to form on the metal (steel phosphate I suppose, using steel wool). I have found that the resultant finish is just as durable as the Arsenal finishes and has exactly the same appearance! -- an attractive dark gray, almost black. Some say that adding more manganese dioxide causes a darker finish, but I've never tried it, as I was happy with what I got!
We often used this technique when finishing .45s built on early Essex frames that needed a lot of fitting, thus often requiring the removal of offending metal. I used to checker the front straps (also violating the finish in a rather spectacular fashion) and the resultant finish worked great and showed little or no wear even with extensive use -- much like the official GI finish. I'm still using a wadcutter gun I performed the magic on back in the '70s and it still looks new.
A couple of cautions:
1. Always be careful of any sort of acid, even such an innocuous acid as phosphoric. I certainly would never deliberately inhale the fumes (although there is no great odor to the process that I could tell, but then I smoke cigars). I started doing this back in the early to mid '70s and still have no "twitch" that I can directly attribute to Parkerizing on the kitchen stove. Just use common sense, WEAR GLOVES AND EYE PROTECTION ANYTIME YOU ARE PLAYING AROUND WITH BOILING SOLUTIONS (with or without acids being involved).
2. Be very careful not to cause any splashes with the boiling solution (of course the same can be said of boiling corn).
3. Prepare your area and your parts before hand, don't try to do this on the spur of the moment.
4. Once you have allowed the solution to cool, you are DONE! Re-heating it don't cut it, It simply doesn't work (I've tried it on several occasions). Have everything that you want to Parkerize ready to go when you fire up the solution. You can keep Parkerizing as long as the solution is hot, but allowing it to get cold kills it -- you've gotta brew up a new solution and start from scratch.
Dave Ruggs- USA
2002
A. You are using a one gallon container to submerge the items in. Use slightly less than one gallon and it won't boil over when you add the items, slowly, to the roiling solution.
Vincent Tracey- Manhattan, Kansas
2007
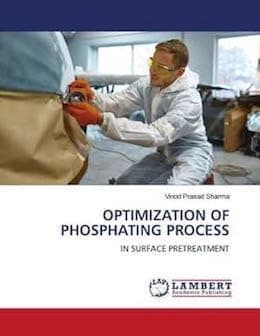
avail from AbeBooks, or Amazon
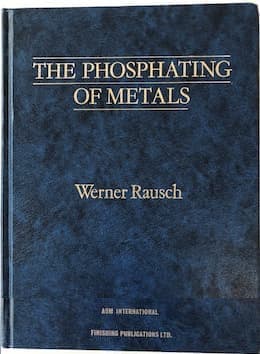
avail from eBay, AbeBooks, or Amazon
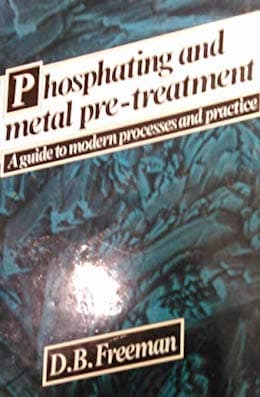
avail from eBay, AbeBooks, or Amazon
(as an Amazon Associate & eBay Partner, we earn from qualifying purchases)
Q. How much water to one jigger of acid? Thanks. Rick
Rick Yuke- Moose Jaw, Saskatchewan, Canada
2005
A. One doesn't have to use pyrex containers for parkerizing. Steel containers work just as well. I use a long mild steel tray for parkerizing barrels. Works fine.
DO NOT TRY STAINLESS containers, they will interfere with the parkerizing process, and leave small little "speckles" on your finish.
Q. When parkerizing rifle barrels, is it necessary to plug both ends of the barrel before parkerizing it? If so, how?
Mike
Mike Kelly- Wagener, South Carolina
April 12, 2009
Q. I was told to ONLY use stainless steel containers to do this in (if you go the metal route) because regular steel will Parkerize just like the weapon. Before I go out and purchase a very expensive stainless steel tray, can anyone confirm that stainless steel is/is not the way to go? Thanks.
Mark Quimby- Birmingham, Alabama
December 28, 2009
A. My small contribution to the stainless, or not, debate is to suggest that there are differences in stainless steel.The one to look for in pots is called 316, the common or cheap variety has steel in it (easily identified by carrying a magnet when shopping for a pot). The steel content would account for spotting. Strangely whilst looking for a pot I discovered that some cheap Chinese pots are 316. Hope this helps.
Peter Fleming- Hobart Tasmania Australia
September 26, 2010
A. The speckles from stainless steel is chromium or nickel dissolved in the acid that makes up a main part of the SS alloy. Pyrex is the way to go. All steels are going to leave behind some of their alloy content in the acids, even 400 series stainless. (300^400 series SS is magnetic, 400^300 is not)
For sealing the two ends...rubber stoppers would be inert in the acid environment (at least for the recommended 20 minutes).
- Pittsburgh, Pennsylvania
December 1, 2011
Thanks, Antonio. We've corrected your typo about the magnetic characteristics of stainless steel grades.
Decades ago I was involved in designing/building many huge zinc and manganese phosphating lines for General Motors and Caterpillar. 316L stainless steel is the ideal way to go if you can afford it.
Regards,
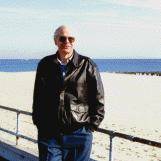
Ted Mooney, P.E.
Striving to live Aloha
(Ted can offer longterm or instant help)
finishing.com - Pine Beach, New Jersey
Q. I have recently been trying my hand at Manganese Phosphate and Zinc Phosphate treatments for gun parts.
The formula I'm using for this is:
Manganese Phosphate
4 oz Jasco Prep and Prime (75% Phosphoric Acid)
2 oz Manganese Dioxide
1 Gallon water
1/2 Biscuit De-oiled 000 Steel wool
190 °F
Immerse Lightly Sandblasted and cleaned parts for 8 minutes
Parts come out nice and Dark charcoal grey (almost black)
Zinc Phosphate
4 oz Jasco Prep and Prime (75% Phosphoric Acid)
8 Zinc pennies dissolved (It's all I had)
1 Gallon water
1/2 Biscuit De-oiled 000 Steel wool
190 °F
Immerse Lightly Sandblasted and cleaned parts for 8 min
Oddly, Parts come out nice and Dark charcoal grey (almost black).. Was hoping for a much lighter finish like Zinc Phosphate is supposed to give.
Questions:
1. Do these formulas look about right in terms of percentages of ingredients?
2. Should I be using the Steel wool in both solutions (is that why my zinc solution is making parts black)?
3. I have heard of using Nickel Acetate to improve the finish. I happen to have some around as I use it for sealer for anodizing. If it is applicable, how much should I use based on the batch sizes shown?
4. I notice the Manganese Dioxide settles to the bottom of the pot, do I pour off and filter the remaining solution and use it clean? Or should I just stir up the pot and keep it suspended while processing my parts?
Thanks a bunch for any information, tips or suggestions.
Rich
- Torrington, Connecticut
April 1, 2013
A.
Questions:
1. Do these formulas look about right?
- They look very close to some of the other formulas I've seen for parkerizing.
2. Black parts from Zn3(PO4)2 bath
- My best guess is that you're ending up with a black zinc and copper oxide layer. The extra stuff in the pennies is probably where your problem is coming from. Start with pure zinc. The steel wool might be causing a problem depending on the impurities in it. It's the only other unknown in the solution besides the pennies that I can see.
3. Nickel Acetate
- I have no idea, I suggest doing some small batch testing. Go up in increments of 3-5 g/ml and see what works best for you.
4. Manganese Dioxide
- If it's precipitated out I'd think that it's not doing much for the chemistry of the bath, filter it out and set aside. Test the bath and see if you have a better finish, if not replace and agitate.
Blacksmith - Boone, North Carolina, USA
April 8, 2013
Multiple threads merged: please forgive chronology errors and repetition 🙂
Q. In an industry where I am undergoing a 20 days training as a student, the total acid to the free acid ratio is maintained in the phosphate baths, but many times the coating is not uniform over the surface of the piston which is being manganese phosphate coated. Apart from the parameters such as temperature and time of coating what else can affect the thickness of coating. There are no measurements done on coating weights. how are coating weights measured? I need information regarding the chemistry behind manganese phosphate coating. As the process of coating occurs how does the acid ratio vary?
Sirisha Pamarthistudent - Mumbai, Maharashtra, India
2004
Q. Hi,
I would like to know the exact quantity and ingredients to make a homemade manganese re-Parkerized treatment for an old rifle. At the moment in Italy I can't find any prepared solution to do it. Any suggestion Is appreciated.
Thanks,
Daniele [last name deleted for privacy by Editor]parkerizing - Italy
2004
A. Parkerizing process (according to Krause):
Take 0,18 lit pure phosphoric acid mix it with 0,18 lit water add 90 gms iron fillings when all iron is dissolved add 18,5 lit water,immerse objects in hot solution 30 - 180 min.
Good luck!
Goran Budija- Zagreb , Croatia
A. Zinc phosphate based solution:
1,8 gm zinc fillings
5,7 gm phosphoric acid
Dissolve zinc in acid.Take 6,5 parts of this solution and mix it with
1000 parts water.Cold
immersion(30-180 minutes).Dry without rinsing, then oil, wax or lacquer .
Good luck!
Goran Budija- Zagreb , Croatia
Q. Do you have a formula for Manganese Phosphate solution ? for Parkerising. Brownells [ Brownells home page (affil link) ] have one in the USA but it is not available in Australia, and they won't send it due to probs sending Chems by post or Courier..
Luke Speer- Safety Beach, NSW, AUSTRALIA
2004
A. You can use 30-40 gm manganese phosphate /1 lit water solution! Good luck!
according to W. Machu: Nichtmetallische Ueberzuge, Wien 1952.
Goran Budija- Zagreb ,Croatia
Q. Read Goran's suggestion of Manganese Phosphate in water....
Isn't manganese phosphate insoluble in water ?
- Malta Europe
March 26, 2009
Q. Where is a source of Manganese phosphate, I have googled it to death with no luck. All refer to using it but where do you get it?
Jan Sorokamaterial scientist - Dallas, Texas, US
July 2, 2009
A. Hi, Jan. Although some of the readers on this page are talking about very simple home-brew, "Manganese phosphate" (in the sense that we are usually using it on this site), is not a simple chemical compound, but a multi-step chemical process including cleaning, activation, grain refinement, the phosphatizing step per se, and a final passivation treatment which you buy from a manufacturer or distributor specializing in metal finishing processes. You can start in our Chemicals & Consumables directory and look for "phosphate", or yellow pages, or Metal Finishing Guidebook or Products Finishing Directory. Good luck.
Regards,
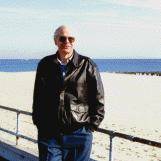
Ted Mooney, P.E.
Striving to live Aloha
(Ted can offer longterm or instant help)
finishing.com - Pine Beach, New Jersey
July 5, 2009
A. In Canada I buy it at The Pottery Supply Warehouse. No idea what they use it for, but maybe you can try a similar business there.
Craig Nelson- Hamilton, Ontario
August 14, 2022
Manganese phosphate chemistry
Q. This is a learning project for me. I am trying to do manganese phosphating home-brew coating. After some reading I decided to go with a nitrate accelerated bath with the following concentrations:
H3PO4 - 8.5 g/L
NaNO3 - 23.6 g/L
MnO2 - 2.5 g/L
My goal is to create 8L final bath.
I started by combining 80 g of 85% H3PO4 in RO water.I added 12 grams of MnO2 to the mixture and topped the container off to 800ml with RO water. Brought the temperature up to 90*C and provided stirring, goal was to create manganese phosphate before adding iron. Left the 800 ml beaker [beakers on
eBay
or
Amazon [affil link] sit overnight to cool off. Added 6g of iron in the form of 0000 steel wool. Added a nickel nickel (Canadian 5C) as a source of nickel ions for grain control. As intended very little of it if any at all dissolved. Just wanted some Ni+ ions in the mixture....Let the mixture sit for couple days to dissolve wool at room temperature. At this point I have somewhat clear liquid with grey precipitate at the bottom. Iron phosphate?
Poured off 400 ml of the liquid into a cooking vessel and diluted to 4L of total volume by more RO water.Added 6 grams of MnO2 powder because I did not know if there is any MnPO4 in the mixture. I did not see any active reactions in phosphoric acid when I added MnO2 to it initially.
I used large 8" nails as the test specimen. I sand paper cleaned the nail, then etched it in a mixture of sulfuric and phosphoric acids, then etched it in citric aid and did a water rinse. I know I am skipping the activation step, however my goal for now is to produce a manganese phosphate deposit and I am going to worry about its adhesion next. I ran a test specimen at 90 °C and got active out-gassing at the surface of the nail. A dark grey, almost black, deposit formed.
I then added 90 grams of NaNO3 (22.5g/L) and ran another test specimen at 90 °CC. No active out-gassing at the surface occurred, a dark grey, but lighter shade of grey deposit formed. This was a much slower reaction. I monitored the PH of the solution at after adding NaNO3 it was at 2.9. I added 85% H3PO4 1 ml at a time until PH dropped down to 2.5 before doing the 2nd test specimen.
When solution cooled I had a mixture of white and black precipitates at the bottom. I am guessing a mixture of sodium phosphate and unreacted MnO2?
My goal is to understand the chemistry of what has happened and what each of the final components are, in order to be able to better optimize the bath later.
Is the grey precipitate in my original 800 ml mixture waste or is it iron phosphate that should be added to the actual plating bath?
Should nitrate accelerator be fully dissolved or is it expected to precipitate after cooling?
Should I see vigorous reaction between MnO2 and H3PO4 or should MnO2 just hang out in the bath as solids occasionally donating Mn here and there?
Is there any DIY test I can do to determine how good / bad the phosphate coating is?
Thanks for teaching.
- Florida, USA
May 18, 2018
A. Hello Igor, I think what is happening (first) is that you didn't "age" the bath with steel wool, so you won't get a good phosphate coating when you immerse the first part.
Second, I would check total and free acid to know if the formulation is correct and how it is after the steel wool. pH is not a parameter here.
Third, you are getting brown sludge, it could indicate some imbalance in your formula. Because of this, you should check the second point.
Best of luck!
TEL - N FERRARIS - Cañuelas, Buenos Aires, Argentina
Room temperature parkerizing / manganese phosphate treatment
Q. Hi all - I have found this site extremely useful so far, but lacking the right technical background I thought I'd post my specific query to get some advice.
I build custom steel bicycle frames; normally they get painted or powdercoated but I am planning to give the next one a protective treatment that leaves a consistent blackened finish with good corrosion resistance and durability.
After doing some research I have decided that some sort of manganese phosphate / parkerizing immersion treatment would be a good option. There is a lot of good information out there but I am keen to find a solution that works at room temperature due to the difficulties heating a bike-sized tank to the boiling temperatures normally used. I have a good workshop here but it is very much on the hobbyist scale.
Chinese patent CN1259451C has been useful and sounds like good results are possible at room temp, but the total bill of materials would be very expensive for a home workshop, considering the volume needed (approximately 140l), so I would like some feedback regarding which of the chemicals are necessary, and which could be done without in exchange for longer treatment time, for example.
The proportions given in the patent result in this BoM for ~140l:
Phosphoric acid 2-4% 4.50 kg
zinc oxide
⇦ on
eBay or
Amazon [affil link]
0.4-0.6% 0.75 kg
Zinc nitrate 0.5-1.5% 1.50 kg
Nickel nitrate 3-5% 6.00 kg
Manganese nitrate 2-4% 4.50 kg
Sodium borofluoride 0.2-1% 0.90 kg
Sodium chlorate 2-3% 3.75 kg
citric acid
⇦ on
eBay
or
Amazon [affil link] 0.5-2% 1.88 kg
Water Balance 126.23 kg
As I understand it, the nitrates are accelerators to make the low temperatures work. Are they all necessary in the amounts given? They are some of the most expensive bits and used in quite large amounts.
Sodium borofluoride is household borax
⇦ on
eBay
or
Amazon [affil link]
, as I understand it. Along with the phosphoric acid, sodium chlorate, zinc oxide
⇦ on
eBay or
Amazon [affil link]
and citric acid it is relatively inexpensive. I assume the citric acid is to control the acidity.
Manganese nitrate is used in place of the more common MnO2, is there is reason for this?
I'm not 100% committed to this particular solution, so if there is a different option that would yield a consistent, corrosion resistant (when oiled afterwards) and durable finish that is achievable in a unheated tank at a price acceptable for low-scale use, I would be glad to hear it.
Cheers
Ben
Bicycle framebuilder - Birmingham, England
March 13, 2019
A. Hi Ben, several points:
- There are many reasons for taking out a patent ...
There is no reason to expect the published patent formula to constitute a viable production process and often not work at all.
- Borofluoride is absolutely NOT household borax!
- Have you costed in the essential effluent treatment facility. Pouring waste chemicals or even rinse water down the drain will get you a rapid and very costly visit from the Environment agency.
- What would it cost to write off a bicycle frame when your home brew does not work?
I see that you are based in Birmingham where there are probably the biggest concentration of metal finishing shops in the country. You will save yourself sleepless nights and a lot of money by letting the professionals do the job.
If you can't find one yourself ask the Institute of Materials Finishing who are also based in Birmingham
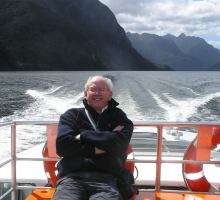
Geoff Smith
Hampshire, England
A. Try next solution: 20 gms tannic acid ⇦ on eBay or Amazon [affil link] , 15 ml phosphoric acid, 1 lit water. Hope it helps and good luck!
Goran Budija- Zagreb,Croatia
Q. Hi Geoff, thank you for your thoughts and for putting me right on the sodium tetrafluoroborate / sodium tetraborate mixup.
My first thought was to look into local professionals. In the event that any finishers or the IMF ever respond to my enquiries perhaps I will report back for the benefit of other hobby or small scale manufacturers who will be familiar with the disinterested or rude replies one can often expect, if any.
Goran, the tannic acid
⇦ on
eBay
or
Amazon [affil link] suggestion is a good thought, I know that it is used for museum / conservation work and its simplicity is attractive. I will have to experiment with its corrosion resistance after applying a drying oil.
Cheers
Ben
- Birmingham, UK
![]() |
A. Hi Ben. Regarding "the disinterested or rude replies one can often expect, if any", I'm in the middle here, being neither a shop nor a potential customer; but there are usually two sides to such problems :-) I'm not here to take sides but, having fielded more than a hundred thousand inquiries here over the last 25 years, I will say that a big part of the problem is that most potential customers pose abstract questions rather than clearly stating their own needs. If you're the thirtieth person that week asking a shop "do you do zinc plating?", they may well have limited patience because the answer "yes" achieves nothing at all. They may do zinc plating, but only offer barrel plating whereas the customer needs rack plating or vice versa. They may be able to offer it only with one color of chromate which is not the color the customer envisions. They may only be able to process a minimum of 75 pounds of screws because of their barrel size, not the 5 small screws the customer has. They may be able to handle low carbon steel, but not the hardened steel suspension parts the customer has because it requires a careful baking regimen. They may be able to plate the zinc but not deal with the existing toxic cadmium plating waste that may be stripped from old parts, etc. Although there will always be some rude people out there, rudeness is often the result of frustration & exhaustion. My experience is that if the inquirer writes:
"I have 23 old bolts from my 1954 Indian motorcycle where the plating has worn off; they range from 1/4"-20 x 1" long to 1/2-13 x 2" long per attached picture. I'm guessing they are zinc plated, and they are silvery colored as you can see in the photo. Would you be able to re-plate these for me and, if so, can you offer an estimated cost and a delivery time if I brought them in next week? If this is not enough info, what else would you need to know? Thanks!"
The answer might still be "no", but you will almost surely get one and it will almost never be discourteous. Regards, ![]() Ted Mooney, P.E. RET Striving to live Aloha (Ted can offer longterm or instant help) finishing.com - Pine Beach, New Jersey |
Q, A, or Comment on THIS thread -or- Start a NEW Thread