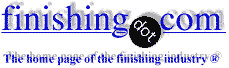
-----
Powdercoat Blistering after Zinc Chromate Undercoat
< Prev. page (You're on the last page of the thread)
Q. Hello,
I have some problems to get good adhesion of a powder coating on a zinc treated surface. This problem concerns especially the zinc with Cr6-free passivation.
What is the difference between the Cr6 and Cr6-free passivation concerning the adhesion of an organic layer?
How can I solve my problem?
Thanks in advance.
- Lyon, France
2005
A. Adhesion of powder coatings onto zinc plated or galvanized surfaces was always a perennial problem, and if you search our site you will see at least a dozen threads on the subject. But adhesion onto trivalent chromated surfaces adds yet another wrinkle because these conversion coatings often also involve a topcoat of one sort or another, which could be wax, lacquer, silicates, zirconium compounds, etc.
In our earth-wide hasty quest for Cr6-free coatings, we've judged the trivalent processes to be their equal if they can simply match the salt-spray test hours of hexavalent chromate ... which unfortunately has left us with a hodgepodge of secret proprietary trivalent chromates which offer the salt-spray resistance of hexavalent chromates, but which may not be their equal in ability of paints and powder coatings to adhere, or in chemical resistance, or in electrical conductivity, etc.
You haven't told us yet whether you are the specifier or the powder coater, and whether you also do the zinc plating and chromating and have control over it, etc. So the first requirement is a detailed process description. If you are the powder coater, and the parts are plated and chromated by someone else and they won't give you the exact process sequence, it may be virtually impossible for you to solve because, as one example, the problem may be separation of the chromate layer from the plating layer.
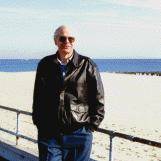
Ted Mooney, P.E.
Striving to live Aloha
(Ted can offer longterm or instant help)
finishing.com - Pine Beach, New Jersey
2005
2005
Q. My company sub-contracts this operation of zinc plated + powder coating. So we have 2 sub-contractors : one for the zinc, the other for the powder coating. The distance between them is around 600 kms.
The process steps for zinc deposition is :
- standard surface preparation
- nitric or sulfuric activation
- passivation CrIII
- drying
- packaging
The process steps for powder coating is :
- phosphate degreasing
- water drying
- Zirconium passivation
- air drying (170-180 °C for 5 minutes)
- painting (with Epoxy wax)
- oven (155 °C during 12 minutes)
If you need other information, I can send it to you.
Thanks in advance.
- Lyon, France
A. Hello DJ;
You may have a strong topcoat over the Trivalent Passivation that is preventing the phosphating over zinc plating effectively.
Your Powder Coater must ensure a good darkening of the zinc plating after his phosphating.
It would also be a good idea to skip the zirconium step before the powder coat.
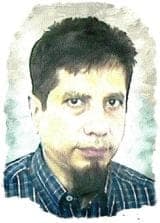
Khozem Vahaanwala
Saify Ind

Bengaluru, Karnataka, India
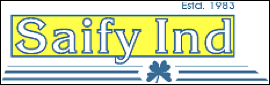
2005
Q. Hello KV !
Thanks for your answer.
Nevertheless, what do you mean by "must ensure a good darkening of the zinc plating after his phosphating". I do not understand darkening...
Moreover, my powder coater apply a phosphate degreasing and not a phosphating. Is it a problem for you. Perhaps a phosphate degreasing is not hard to prepare the surface?
Regards
- Lyon, France
2005
A. Hi. KV may not have seen your followup. I believe he was suggesting that the phosphate must react with the zinc for good adhesion, as evidenced by a gray color; and that if you are not seeing the gray color develop, it likely indicates the presence of an unacceptable zirconium topcoat on the zinc which is preventing the graying and preventing good adhesion.
Again, trying to get good adhesion of powder coating onto a secret proprietary Cr6-free chromate applied by others is shooting with a blindfold on. You must pass most of the problem back to the plating shop, who must pass it back to the vendor of the proprietary -- the powder coater probably can't solve it on his own. RoHS has created a nightmare for you :-(
Regards,
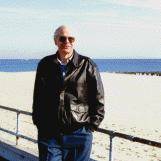
Ted Mooney, P.E.
Striving to live Aloha
(Ted can offer longterm or instant help)
finishing.com - Pine Beach, New Jersey
Zinc Plating before Powder Coating for Architectural Projects?
Q. I am an architect in Michigan. My firm designs many projects with decorative metal fabrications on the exterior.
I had recently specified the decorative railings on a project to be zinc-plated and powder coated.
The fabricator indicated that it is not possible to powder coat over zinc plating?
Is this true? Is there another substrate finish that we should specify for powder coating?
architect - Lansing, Michigan
2006
2006
A. The fabricator is incorrect, David. Zinc plating plus powder coating is a fine specification. The zinc plating will offer sacrificial protection to deter rust in any areas where the powder coating may get scraped in service.
It is true that, if not done correctly, there can be adhesion problems in powder coating over zinc plating; so if done by separate shops there may be buck-passing if adhesion problems do develop. So I would suggest that you try to find a shop that offers both zinc plating and powder coating so that one finisher can be responsible for the finish.
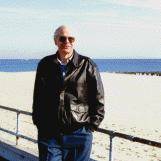
Ted Mooney, P.E.
Striving to live Aloha
(Ted can offer longterm or instant help)
finishing.com - Pine Beach, New Jersey
A. Dear sir,
If the Zinc Plating is done not properly, then you will face problem, We suggest best is zinc phosphating done at 65°C which will give very smooth crystalline coating of zinc, then powder coat.
- Karachi, Pakistan
2006
Hi. Zainuddin is steering you well that zinc phosphating is a more traditional, easier, and less expensive pretreatment for powdercoating than zinc plating -- but in a real-world corrosion test my guess is that the zinc plating will win handily because of its sacrificial capability, although I'm not aware of specific comparison testing.
Regards,
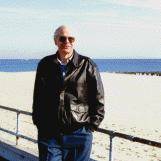
Ted Mooney, P.E.
Striving to live Aloha
(Ted can offer longterm or instant help)
finishing.com - Pine Beach, New Jersey
2006
A. A further point to Ted's reply, is that zinc plating is a quite thin zinc coating, and the corrosion protection is proportional to the coating thickness (in this case).
If the application is external, where corrosion is a consideration, then hot dip galvanizing should be considered. Typically about 6-10 times the Zn thickness, and powdercoating over HD Galv is no more difficult than over Zn plate. The same advice applies, ensure competent pretreatment and preferably by one shop that does both coatings so you don't end up refereeing in a fight over who did what wrong!
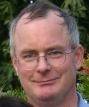
Geoff Crowley
Crithwood Ltd.
Westfield, Scotland, UK
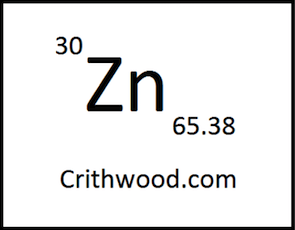
Q. Hi,
I am looking to get a couple parts zinc plated and was hoping to get some advise on pretreatment processes and what chromate to use for the zinc plating. Ideally I'd like to powdercoat the lids after they are plated to have them match the rest of the system. However, from looking around I have seen that there are a lot of common issues associated with doing this.
I was curious if it's beneficial to blast the steel after plating to help with the adhesion of the powdercoat or would this be counterproductive and take off the zinc as well? Additionally, does the thickness of plating impact how well the powder can bond with the surface? Are there any specific types of chromates and pretreatment techniques that typically do better when powdercoating on top of a zinc plated surface?
Please let me know what you think, any advise would be appreciated!
- Denver, Colorado, USA
January 9, 2020
A. Hi Josh. I don't think blasting is beneficial, and the thickness of the zinc plating is irrelevant.
However ... in the old days of hexavalent chromates, the trick was to keep the chromate layer as thin as possible so the chromate layer could not shear, as mentioned by Robert Probert several times on this site. But today, with proprietary trivalent chromating in "thick film", or "thin film" varieties plus proprietary topcoats, it is far trickier. Suppose you succeed the first time, then go back for more a few months later ... the powder coating shop may do exactly what they did last time, but the plating shop may have changed their chromating process and not tell you, or at very best take no responsibility for lack of adhesion of powder coating applied by others.
My own take is that these days you must get the whole process from one shop who takes responsibility for the finish.
Regards,
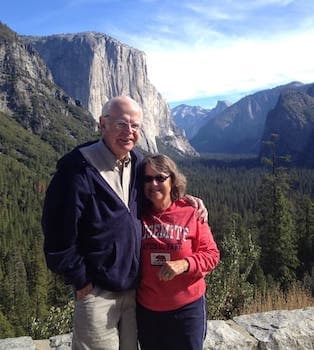
Ted Mooney, P.E. RET
Striving to live Aloha
(Ted can offer longterm or instant help)
finishing.com - Pine Beach, New Jersey
January 2020
Q, A, or Comment on THIS thread -or- Start a NEW Thread