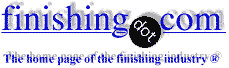
-----
Spalling on stem portion of Sursulf salt bath nitrided valve
Q. Ours is a Engine Valve manufacturing firm. Here on our customer requirement, we supply valves with Sursulf coating, which is done in-house. For the past few days, this coating results in Spalling on the stem portion of valves. This is very detrimental as far as our process specifications are concerned. So being a QA manager, I am very eager to know the reason & the possible steps to be adopted to avoid occurrence of the same problem in future.
P R KONDEENGINE VALVES - NASHIK, MAHARASHTRA, INDIA
2004
2004
A. Hi P R. Sursulf is a trade name, and probably a registered trademark, for one particular proprietary salt bath nitriding process for ferritic nitrocarburizing (carbonitriding). You may be able to get help by referring the problems to the supplier/licenser. For more general questions are about salt bath nitriding, other suppliers of salt bath nitriding processes, like Kolene probably can help help you as well.
Sorry, I'm not personally familiar with spalling in salt bath nitriding, so I would suspect the raw material as much as the nitriding process.
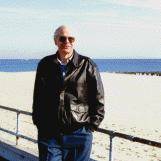
Ted Mooney, P.E.
Striving to live Aloha
(Ted can offer longterm or instant help)
finishing.com - Pine Beach, New Jersey
A. Please explain the SURSULF process then I shall help you out.
Regards,
J.V.Pawar- Pune, Maharashtra, India.
2004
A. Dear Pawar,
Sursulf is a patented process of salt bath nitriding. It's quite similar to Tufftride process. Standard procedure is as follows: Degreasing - Preheating to 400 °C - Sursulf treatment at 565 °C for 1 hour - Cooling in water - washing - Surface finishing after drying (optional).
Bath is composed of alkaline cyanates & carbonates as well as stabilized by Li-compounds plus a small amount of sulfur compounds(K2S)
- Pune, Maharashtra, India
2005
A. Spalling / chip off in the case of steel is caused mainly by the inherent metallurgical defect like embedded scale/inclusion in the metal itself, more likely in case of SS.
In this case, nitriding may have revealed the inherent defect, it is felt, assuming that the working parameters have been properly maintained for nitriding.
We, as manufacturer of cyanide-free nitriding salt working in the range of 565-570 °C, confirm that our customers have never experienced such defect in nitriding with our salt.
- KOLKATA, WEST BENGAL, INDIA
July 23, 2008
A. There can be two causes for this among others.
First it may be hot corrosion on the surface. This may be due to inferior maintenance of the bath parameters. Excess iron content in the bath leading to formation of complex ferro and ferri cyanide, excessive sludge in the bath (dirty bath conditions), high grinding removal in one grinding pass leaving excessive grinding stress on the stem surface, higher temperature of the bath leading to higher cyanide in the bath, localized over heating of the bath (some coils cut etc) giving higher cyanide, rusted or oxidized stems leading to iron oxide separation inside the bath all together or alone can lead to what you call spalling and what a re-grinder of crankshaft will call "mapping".
2) If it is chipping off, then it can be due to high cyanate content ~ > 38%/40%
Good Luck.
- Chennai, India / Houston, Texas
November 30, 2009
Q. Dear Sir,
Please help me out to solve this issue.
My main problem is that a thin film or layer is formed in the surface of the material after nitriding process, while inspecting the compound layer and the hardness it is found. I don't know the reason, but the hardness is good after removing the thin film layer which forms on the surface. My bath size is 450 * 750. How much re-generator should I add daily? The bath is running continuously since the size is small. What is the amount of weight I should load per batch?
It would be helpful if someone helps me.
- Coimbatore, Tamil Nadu, India
September 12, 2011
Q. Sir, in our engine valve manufacturing unit, we're using steel grade SUH11 (per JIS:G4311). After Salt Bath Nitriding we are getting seat runout which is resulting in high rework and scrap. Please suggest a solution?
Divya Tej Ganga- Hyderabad, Andhra Pradesh, India
December 30, 2013
Q, A, or Comment on THIS thread -or- Start a NEW Thread