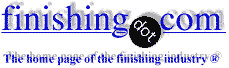
-----
How to set up the Zinc Phosphate Process?
Q. We have been manufacturing drill stem elements for drilling contractors for at least 5 years. On such elements there is a need to phosphate the thread connections. We would like to start doing this ourselves rather than subbing out the work, but we need information on the process. For example temperature, time in tank and any advice on the chemicals used to make up the zinc phosphate, I have learned that a titanium dioxide ⇦ on eBay or Amazon [affil link] is used as an opacifier. Can you help? I would be grateful of any information you could supply.
Regards
Mark Paton- Aberdeen, Grampian, Scotland
2004
A. Very few people use a home brew for phosphating. Step 1 is which of the three general types of phosphate do you want to do? Next is to contact two or more vendors with the type of metal and amount that you want to phosphate and ask for quotes for equipment and chemicals. Ask what tech service they provide on a routine and an emergency basis. Find out what you are going to need for in house lab testing to control the tanks. They will provide operations data sheets that has the ranges of all of the parameters.
After that, the secret of successful phosphate operations is bring the temp up fast, keeping metal in the tank as much as possible and dropping the tank temp as soon as done. I always saved the last water addition for evaporation until the last load was out. You can not overwork a phosphate line, but it will go sour rapidly if it is at temperature with no load or a series of loads that are too small for the tank volume. The Ti modifier in a rinse tank is necessary if you are going to acid etch the parts. Phosphate works best with freshly blasted parts.
James Watts- Navarre, Florida
Q. As per Mr. James Watts, advice that we should not overload phosphating line, is it applicable to entire line bath chemicals or only for phosphating bath? Because if it is true then we can have more phosphating bath and we can increase the capacity.
Pankaj Patilsurface finishing - Maharashtra
September 7, 2008
A. It is my feeling that it is difficult to overload a phosphate tank. BUT!
If you have a huge weight of parts, the tank temp will drop and you will not get a good phosphate, so you will need a larger tank OR huge heaters OR add parts a few at a time and remove the ones that are done and immediately add more IE, you sequence the parts rather than an entire load at one time.
Unless you have an unusual loading, chemical additions probably will not need to be done during a shift.
A tank at temp with no load in it is the worst thing that you can do for a phosphate tank. It really messes up the acid ratio which is a key for good work.
- Navarre, Florida
![]() |
A. Dear Mr. Paton Zinc phosphating process has pretty many parameters to be taken in consideration and it also costs more; so I can easily say it is not that easy to set up a bath by yourselves but I can suggest another kind of phosphating process: iron phosphating. First you should investigate if iron phosphating is suitable for your parts and, of course, for the later processes. The rest is quite easy compared to zinc phosphating. There are 5 important parameters to be taken in consideration. Temperature, Pressure (for spraying), Time, pH, Total Acid level. These should be settled in the charge of a process engineer or a chemist, otherwise getting the proper result will be harder. Best Regards, Levent Aliustaolu- Bursa, TURKEY 2004 |
A. For drill stem the object is usually make/break lubrication, in other words the phosphate coating is primarily sacrificial, intended to crush and provide lubricity so that the stem can be disassembled on removal. The common treatments for this are manganese phosphate and heavy zinc phosphate. The immersion time will vary from 2 to 10 minutes and the temperature of the bath will vary from 130 to 170 °F.
Use a ready-made chemical from a vendor that can help you set up the bath. The equipment is pretty basic, just a series of heated tanks and a hoist (programmed hoist for high volume). The phosphate tank will have to be stainless, like 304L or 316. Everything else can be mild steel or plastic.
I hope this helps,
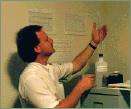
Jeff Watson
- Pearland, Texas
2004
A. Dear Mark,
A typical phosphating process is minimum seven step process. Additional steps may be required depending upon structure and job conditions. For selecting suitable bath size, component details and quantity is required. Further a suitable process has to be selected from low zinc phosphating, heavy zinc phosphating and manganese phosphating. Bath controls are very simple.
Prabhakar Gupta- Kanpur, U.P., India
Q. In our company we are doing phosphating of couplings. After the phosphating, how to identify the effectiveness of adhesion? Or in other words how to do a quality check. We have salt spray test... any other method?
SATHESH PANDIAN- Navimumbai, Maharastra, India
January 8, 2009
Q. Hello all,
I would like to ask a question about zinc phosphating process. What is the best conditions for each bath to take good result for coating ? And how can we understand that whether it is good coating or not? For example we measure T.A, S.A, Fe, Chloride, HAS, PO4 What is the optimum tolerance range for these parameters? And especially how can I improve rinsing bath? Thank you.
Best Regards
Duygu
- Bursa, TURKEY
December 26, 2012
Phosphating of downhole drilling parts
Q. We are currently looking into doing a phosphate coating on downhole drilling parts. The parts will have both threaded and non-threaded surfaces. Anti-seize will be used on the threaded surface though the customer calls for phosphate which I assume is both for lubricity and corrosion protection. I cannot determine on my own which phosphate to use out of Manganese and Zinc. The parts that I have seen in the past have a dark grey finish. I've been told that the type of phosphate can be determined through color (somewhat). Could I use the same or any phosphate on threaded connections that require a very high-strength thread lock ⇦ on eBay or Amazon [affil link] or will it keep the thread-lock from bonding to the substrate/base metal. Thanks.
Joseph Hamby- Cleveland, Texas, USA
December 21, 2015
Q, A, or Comment on THIS thread -or- Start a NEW Thread