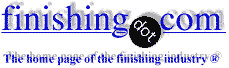
-----
Saline-resistant coating for stainless steel shaft to reduce seal damage
2004
Q. My company is experiencing a problem using 316 stainless steel. A 3.6mm dia. rod passes through 2 retained nitrile 'o' rings. In operation, the rod moves up and down through the seals at about 2mm/sec. i.e. very slowly. As the rod moves up and down, it also rotates at a low rate in a spiral manner. The rod is moved up and down by a screw thread. The rod is very polished spec 316 stainless steel. The rod is immersed in saline solution ( 0.9% ) as it moves up and down, i.e. it is always immersed.
The problem is this: Over a period of between 3 and 6 months the rod surface becomes corroded but I suspect that eroded would be a better word. The sharp edges produced by 'erosion' chew up the 'o' rings and then saline passes through the seals and contaminates everything underneath.
There are no detectable stray volts about so electrochemical action seems a no no. There is another 316 stainless item in the saline bath but not in contact with the rod. In my mind the problem appears to be that the rod surface is not hard enough and can easily pit, leading to corrosion.
My request is this. Is there a hard corrosion resisting metal that can be applied to the 316 but still enable us to maintain a tolerance on the rod diameter. Electroless nickel perhaps?
Thanking you,
Colin Bryantoptical equipment manufacturer - Worcester, Worcestershire, UK
First of three simultaneous responses --
A. Stainless steel can be plated by a variety of metals, including nickel (both electroless and electroplating processes) and chromium. Another option would be a diffusion hardening process like Kolsterising from Bodycote. However, I am not sure that erosion (lack of hardness and wear resistance) is the problem. Type 316 is not impervious to corrosion in chloride environments, so depending on the actual concentration, you may need something with better resistance to pitting and crevice corrosion. Austenitic stainless steels like Type 317 and 904L have better resistance, as doe duplex alloys like 2205 and 2507. You can find more information on these alloys from producers like Sandvik, Carpenter, and Outokumpu.
Toby PadfieldAutomotive module supplier - Michigan
2004
Second of three simultaneous responses --
A. Yes. High phosphorous only, no-bake.
Guillermo MarrufoMonterrey, NL, Mexico
2004
Third of three simultaneous responses --
A. Try softer seals, either O-rings or lip seals.
Tom Gallant- Long Beach, California, USA
2004
A. Hello,
You should try Thermal Plasma Spray of Chrome Oxide, 0.005" thick and then grind it and lap it to lowest Ra value. May be 2 or 3 Ra.
Ken Katakia- Georgetown, Ontario, Canada
2004
A. You should go to a 6 moly stainless. If your temperature is less than 180F it will not pit.
Bruce Bishkin- Elmhurst, Illinois, USA
2005
Q, A, or Comment on THIS thread -or- Start a NEW Thread