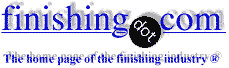
-----
Nickel Plating Repair

Q. Hello all,
I'm also looking to repair an EN plating on a steel part, however, the circumstances are different and likely difficult. I'm speaking on behalf of the small company I work for, whose main business is not metal finishing related.
The parts in question are components of a large machine assembly, made of ASTM A36 steel (I'm still trying to find composition information), specified with a flash electroless nickel plating not to exceed 0.01 mm (0.0004 in) thick. They comprise a plate and ring, each approximately 2.5 ft (750 mm) in inner diameter, weighing at least 725 lbs (330 kg), and located on the bottom of the assembly, so in-situ repair is the only practical option for the time being.
The nickel plating has served well in use for about 2 years, with more than incidental contact with water, but after an incident that exposed it to dust and possibly abrasion from the inadvertent "machining" of an adjacent anodized aluminum part, significant patches of red rust have begun to show through. The patches perhaps the size of a thumbnail, covering perhaps 50% of the affected area. For clarity, the dust generated likely contained both the anodize and raw aluminum, and may have mixed with small quantities of water.
So far, we've tried carefully sanding off the rust (with unknown effects on the adjacent coating) and treating with C-L-R cleaner
⇦ on
eBay
or
Amazon [affil link]
, followed by coating with Boeshield T-9 ⇨
In similar cases, we've tried using zinc-rich paint as a repair and encountered adhesion problems, so my manager is hesitant to let me try it.
The goals of the repair are:
1) Prevent further corrosion, or at least minimize generation of flaking or debris
2) Minimize final coating thickness to maximize clearance to a nearby rotating assembly. 150-200 micrometers (0.008 in) would be an upper limit for final coating thickness.
Mechanical Engineer - Vancouver, BC, Canada
⇩ Related postings, oldest first ⇩
2004
Q. We are a manufacturer of parts used in the Aerospace industry. My situation is as follows: We have components, (silicon iron substrate), sent out for electroless nickel plating. During final assembly these plated components have a tendency to get damaged or chipped plating because of handling issues. These chips are extremely small, but big enough to expose the substrate material, hence corrosion. I need to repair these chips with brush plating since they cannot be submerged in a bath. I have been experimenting for several weeks now with brush plating and various nickel solutions. I cannot get my experimental parts to pass a salt bath. I have been experimenting with voltage settings, activating solutions, surface preparations with alcohol, plating time etc. I cannot blast the chipped areas either because they are assemblies.
Does anyone have any information or suggestions on what I can try to get this process to work. I am at a loss. I have contacted the companies where I purchased the equipment and have tried what they suggested. Can small chips be repaired with brush plating?
Thanks a lot.
Manufacturing Engineer (Aerospace Engineering) - Wallingford, Connecticut, USA
February 9, 2022
A. I see two different problems. The silicon present in the substrate requires Hydrofluoric acid not found in brush activators that must be safe for hand use (HF is so dangerous that will penetrate skin and destroy bone). The other is the EN itself, which is also very difficult to activate for it tends to develop a dark smut during reverse etch and will never present a grainy microstructure to provide anchorage. My opinion would be to strip the whole plating and do it again, probably using a more ductile plate such as a sulfamate nickel. It will pass a salt test and will not chip. Brush plating companies also offer other chemistries not based on sulfamates.
Guillermo MarrufoMonterrey, NL, Mexico
2004
Q. Guillermo,
I really appreciate your response, thank you. I need to find a solution that would allow me to replate the tiny chipped area without stripping the existing EN plating. The brush plating companies are telling me that their products will work, even though I have informed them of the silicon iron substrate. I've even sent them some experimental parts to repair. Is it even possible to repair these parts with brush plating and have them pass a salt fog or salt bath test. Since I do not have much experience in plating yet, I'm not sure I follow exactly what you are saying.
Thanks
- Connecticut
2004
A. Gary,
To activate a EN deposit. First no pretreatment steps can be done with a anodic current. Then you use a acid with a anodic current will the EN deposit expose the phosphorus contents. To activate the EN is to use a cathodic current in 30-40 g/l Na Cn for 2 minutes. Rinse in 10 % chloride acid. Cathodic activation for 5-15 sec or to see if the gassing 3,5-4 volts in a clean 30 % sulfuric acid. Activate in a warm nickel activator. With brush nickel method is to use citric acid
⇦ on
eBay
or
Amazon [affil link] together with hydrofluoric acid. Remember never a anodic pretreatment.
Regards,
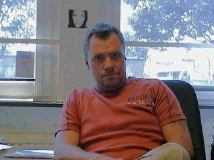
Anders Sundman
4th Generation Surface Engineering
Consultant - Arvika,
Sweden
2004
Q. I have the exact same issue except my base metal is free machining steel, 12L14. I have small dings from fixturing down to base metal, plating is silver over nickel. It is a full up unit that is non hermetic so I cannot submerge it or subject it to cleaners or activators. I can put voltage on it however. Is there a way to top got the ding with any material to protect it from corrosion? It does not need to look pretty. Lastly, is zirconium an option?
Roman burtykCrane aerospace - Chandler Arizona usa
January 26, 2016
A. Hi Roman. This can probably be brush plated, and there are specialty firms experienced in traveling to job sites and doing such repairs. I believe that zirconium is a non-plateable metal however.
Regards,
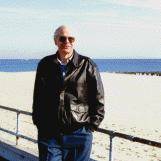
Ted Mooney, P.E.
Striving to live Aloha
(Ted can offer longterm or instant help)
finishing.com - Pine Beach, New Jersey
January 2016
A. I think the responses so far have missed two rather important points.
First, EN is not pure nickel. It is an alloy of nickel with (usually) phosphorus. "Repairing" it with "pure" nickel plating raises questions of corrosion sites, etc.
Secondly, and far more important, this appears to be for an aerospace application. Any remediation work must be signed off as acceptable by the client.
In my experience primes take a dim view of patched up work.
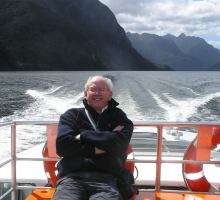
Geoff Smith
Hampshire, England
January 27, 2016
A. Geoff, Roman never mentioned that he was using EN. So brush plating Ni would be fine in this case.
Mark BakerProcess Engineering - Phoenix, Arizona USA
January 30, 2016
January 2016
I think we'll need to wait for Roman to clarify :-)
- "exact same issue" implies EN, but
- "silver over nickel" implies not EN
... and it's just not truly clear.
Regards,
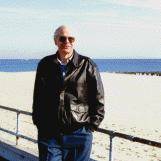
Ted Mooney, P.E.
Striving to live Aloha
(Ted can offer longterm or instant help)
finishing.com - Pine Beach, New Jersey
A. If I may, in my opinion you aren't addressing the root cause, which is mis-handling. If you sit down with ALL of the employees who handle these parts and brainstorm the reasons (even the smallest least possible) and document informally or ideally formally on say, an FMEA form. Then list all the ways for each issue that will prevent or eliminate the causes of the chips. You will not have to find a way to repair the Nickel plating, my friend.
Walt SecondineAerospace - Owasso, Oklahoma USA
June 15, 2019
Q, A, or Comment on THIS thread -or- Start a NEW Thread