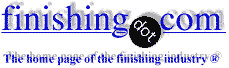
-----
Anodizing 356 T6
Q. I am working on an automotive project that involves anodizing a bore to improve its wear resistance. I started with 383 diecast alloy and every thing worked out fine, but I encountered problems when I used the same parameters to anodize cast alloy 356 T6. Specifically, when I used a low current density (A/in2), it seemed that the bore was anodized very little (approx. 1 micron) or not at all. However, when I ramped up the current to approx. 5 amps and then decreased it to a value of 2 amps, the bore began to anodize as anticipated. I was wondering whether my thoughts are correct. Is there some sort of voltage threshold that must be exceeded in order to start the anodizing process on 356 T6.
Bill LiavasAutomotive - Concord, Ontario, Canada
2004
A. 356 requires 19 volts to get 12 Amps per square foot in 165.3 gm/L Sulfuric Acid (Alcoa 1956 !)
Now you said "bore", so I guess this is inside a cylinder. Depending on the depth of the bore you may need an inside cathode. If the bore is dead end on one end then you will have to pump in fresh solution, preferable thru an aluminum or lead tube cathode.
Come back with some more information.
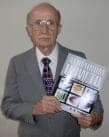
Robert H Probert
Robert H Probert Technical Services

Garner, North Carolina
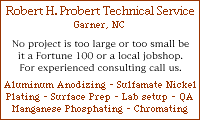
2004
Q. Thank you Mr. Probert for your reply to my question. The bore that I am trying to anodize consists of a cylindrically shaped through hole. Currently, I am using an inside cathode and pumping fresh fluid throughout the bore. I was wondering what voltage and current setting would produce the maximum hardness result. Also, I am not clear about the 165 gm/L sulfuric acid value seen in your response. Do you mean
165 g/L or 165 mg/L. Does this refer to the sulfuric acid concentration? If so, the acid concentration that I am using ranges from 25 to 30 %wt. Finally, what does "Alcoa 1956" refer to?
Any help would be much appreciated.
Thank you,
- Concord, Ontario, Canada
2004
A. My opening statement above was derived from Alcoa's Aluminite Book published in 1956. So many job shop anodizers do not understand that different alloys require different voltages to drive 12 amps per square foot.The 19 volts that I listed is the right voltage in 165.3 GRAMS PER LITER (15%/weight) (12 fluid ounces per gallon) (9.3
%/volume of 66 degree baumé Electronic Grade Sulfuric Acid).
Now if you are as high as 30%/wt the voltage requirement will be much lower and I do not think such a range has been published. Why so high? The coating will be very soft, with very large pores. Dissolution is worse at higher acid concentrations and that may be your problem. If I was there I would cut the solution to 15%/wt and try 19 volts.
Keep coming back - we'll get it yet.
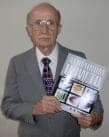
Robert H Probert
Robert H Probert Technical Services

Garner, North Carolina
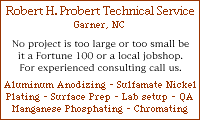
2004
A. Here's a thought, bore it out and put a brass sleeve in it.
William Moore- San Diego, California, USA
2004
Q. Thank you once again Mr. Robert Probert. I have tried using lower voltages with the 30 % wt sulfuric acid solution. However, it seems that using lower voltages does not start the anodizing process within the bore. Currently, I am using a carbonized cylindrical cathode with a hole drilled through the center, in addition, to cross drill holes
(i.e. holes perpendicular to the center hole) enabling the solution to be pumped directly through the cathode and into the bore. Using high voltages ranging from 18 V to 20 V, corresponding to a current range of about 2-3 amps, seems to start the anodizing process. However, maintaining these parameters constant does not result in consistent results in terms of the thickness of the anodized layer developed. Also, the solution I am using was obtained from a vendor and I am only aware of the 30%wt sulfuric acid concentration. Do the components of the other 70% play a factor in the quality and thickness of the anodized layer developed?
Could that be a source of error in not obtained consistent results? Or, could it be the material? Any help would be much appreciated.
Thanks,
- Concord, Ontario, Canada
2004
A. The solution is too concentrated, too conductive. Please cut the solution down to 15%/wt which is 12 fluid ounces per gallon of 66 degree baumé Electronic Grade Sulfuric Acid. With the lower designated concentration the anodizing will "start" at 16 volts, 72 F, causing 12 amps per square foot. 30% is unheard of in conventional functional anodizing! 30% if it anodizes at all, makes a softer coating.
Keep coming, we will get it yet.
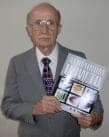
Robert H Probert
Robert H Probert Technical Services

Garner, North Carolina
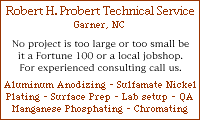
2004
Q, A, or Comment on THIS thread -or- Start a NEW Thread