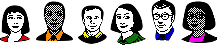
Metal finishing Q&As since 1989
-----
Galvanizing startup
Q. We are starting to manufacture anchor bolts and imbeds and are exploring doing the hot dipped galvanizing in house. We would like to get information on what equipment, materials, permits, etc. would be needed.
Gene Burrus- Beaumont, Texas
1999
A. Hi Gene , If you are considering galvanizing anchor bolts "etc" then there is really only one process worth considering, in my opinion, and it is definitely not "Hot Dip Galvanising". I would suggest that you investigate Mechanical Plating & Galvanizing call Macdermid in Waterbury Connecticut. The process is a lot easier to manage than "Hot Dip" and just as effective for corrosion protection . But I must stress Call the Head office in Waterbury. Regards

John Tenison - Woods
- Victoria Australia
1999
A. For our experience there are two possibilities to galvanize threaded parts.
1. Hot-dip galvanizing at higher temperatures. This means temperatures above 970°F (520°C) which is only possible in a special furnace. This furnace has a ceramic kettle. This design/process is more common in Europe. After dipping you have to spin the parts. You need pretreatment of the parts with degreasing, rinsing, pickling. This liquids need a waste water treatment. In most countries you need a special permission to run these type of plants.
2. A process called amazinc which is a new technology. The advantages are less investment costs, no need of pretreatment of the parts like washing, pickling etc. (and no need of waste water treatment), more uniform coating than hot-dip. It is not needed to heat up the plant all the time. This process is very well suitable for threaded parts.
Best regards,
Peter Kordt- Hagen, Germany
1999
----
Ed. note: Please try to discuss alternate technologies in generic terms rather than with brand names, folks. For one thing, once a brand name is thrown into the mix, readers are shy that they'll hear from lawyers if they pooh-pooh it; so the result is you hear only glowing positives and none of the negatives, which means you also have to throw away the positives you've heard, and be left with nothing :-)
A. John is right, who would want to put in a hot galvanizing process with the great technology of mechanical galvanizing available? You can customize your process size to your production volume by varying the size and number of the tumblers (they look like small cement mixers).
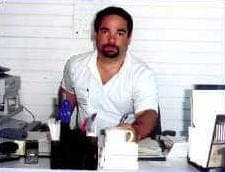
Jim Conner
Anoplex Software

Mabank, Texas USA
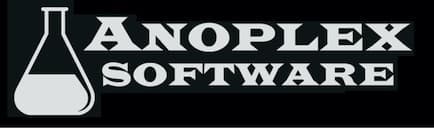
1999
A. There are several galvanizers in the state of Texas that can already provide you with a hot dip galvanizing services.
Take a look at The American Galvanizers Association web page at www.galvanizeit.com to read up on the different types of galvanizing to see what your potential customers would like.
MNS
Mike Stroia- Canton, Ohio
1999
Q. What is the amazinc mentioned by Peter Kordt?
Terry Edgecombe- Auckland, New Zealand
2001
A. Mr. John Tenison-Woods commented on - that mechanical galvanizing (should really be called mechanical plating because only applying zinc in molten form to steel is actually galvanizing) is "just as effective for corrosion protection." This is not really an explanation of the differences between zinc hot-dip galvanizing and mechanical plating of zinc.
Hot-dip galvanizing of fasteners, threaded rods, etc. applies zinc uniformly to all surfaces -- even the hard-to-reach corners and joints. This means 100% corrosion protection. Mechanical plating peens zinc onto steel and is limited by the size of the glass shot doing the peening. Hard-to-reach places do not get any zinc cover and that is exactly where corrosion begins. Additionally, there is very little control over the mechanical process to insure that all surfaces are coated with the same thickness of zinc.
Because the galvanizing process is a metallurgical reaction between the steel and zinc in the molten bath, the bond strength of the zinc coating is approximately 3600 psi, an order of magnitude greater than the mechanical bond in plating. Thus, galvanizing provides a tenacious coating that resists abrasion. Additionally, in the metallurgical reaction between zinc and steel in the molten zinc bath, zinc-iron alloy layers (delta, gamma & zeta) are formed prior to the formation of the bright, shiny pure zinc outer layer known as the eta layer. The three alloy layers are actually harder than the base steel itself. In the mechanical plating of zinc, only pure zinc is peened into the steel and the pure zinc is significantly softer than the steel itself -- meaning abrasion on the mechanically plated parts are damaged rather easily.
Philip G. RahrigAmerican Galvanizers Association - Centennial, Colorado, USA
2001
2003
A. Electroplating, hot dip galvanizing, and mechanical plating all have their advantages and disadvantages. A proponent of any one of the technologies will usually stress the advantages of that process while not mentioning the disadvantages. So before choosing one, it is best to find an advocate of the other processes and read what they have to say.
But for a first-cut analysis, electroplating is the least expensive and most practical for thin coatings, hot dip galvanizing for thick coatings, and mechanical plating for mid thicknesses. And in fact, you'll see that that's mostly the way things play out in practice. Electroplaters generally do 0.00015" to 0.0004" zinc, and almost never over a thousandth of an inch; nobody ever hot dip galvanizes that thin; and the range in between is usually done by mechanical plating or zinc flake dip-spin coating. Yes, they all have advantages and disadvantages, but required thickness is probably the main driver.
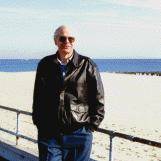
Ted Mooney, P.E.
Striving to live Aloha
finishing.com - Pine Beach, New Jersey
Q, A, or Comment on THIS thread -or- Start a NEW Thread