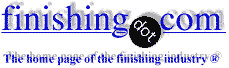
-----
Gold plating on Music Wire
Q. We are gold plating on the springs of Music Wire for one of our customers lately he's been complaining of corrosion on the gold plating .We plate nickel before plating gold and every thing seem good in testing.Any suggestions.
M. KhawarIslamabad, Pakistan
1999
A. Nitric acid porosity test?
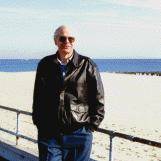
Ted Mooney, P.E.
Striving to live Aloha
(Ted can offer longterm or instant help)
finishing.com - Pine Beach, New Jersey
Q. IN RESPONSE TO MY QUESTION You HAVE WRITTEN NITRIC ACID POROSITY TEST. WOULD You PLEASE EXPLAIN HOW THE TEST IS DONE AND WHY SHOULD WE DO IT. THANKS AGAIN.
M. Khawar [returning]Islamabad, Pakistan
A. The gold needs to be thick enough to be non-porous. This is tested by exposing the parts to nitric acid fumes. Gold is resistant to nitric acid so if the gold is pore-free the fumes will have no effect; if the fumes do reach the nickel, nickel nitrate crystals will grow at the pores. See ASTM B735 for further info on the test.
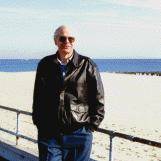
Ted Mooney, P.E.
Striving to live Aloha
(Ted can offer longterm or instant help)
finishing.com - Pine Beach, New Jersey
A. The cleaning and activation of the music wire has to be pretty stringent as the delayed reaction [ie corrosion at a later date are causing you problems. do not be fooled as it may not be the gold that is bad but rather the nickel to the substrate. If thats bad, then so is the gold.
I used to use nitric acid, rather than the fumes. I would plate, then subject the parts to a 50% Bv, nitric acid at room temp for up to 15 minutes. would rinse, dry then tape test and look under magnification. If they passed that test, especially the tape, then they should all be good. I used a percentage of parts in the lot plated against the total of parts in the lot. ours were small parts so I could take 1 part for each 50 thousand parts.....50 parts and do the test. If one failed, then I figured one in a thousand would fail. I got it down to zero defect as I had zero in my test results. that came from realizing the cleaning and number of turns on the EN bath was critical. Oh, and the gold adhesion to the nickel .... And the gold purity...
Todd Huehn- Coon Rapids, Minnesota
Q, A, or Comment on THIS thread -or- Start a NEW Thread