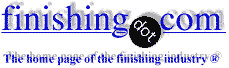
-----
Can't plate onto 316 stainless steel
I am Electrowinning Gallium from an Alkaline electrolyte, 316SS is used for anodes and cathodes, I am finding real difficulty in depositing on the SS. I can't use a strike plate, I have tried activating by reverse current, also using a 25% HCl dip but those methods don't help. I have tried the full range of CDs from 5 to 120 asf. For info if I use a Galvanized steel cathode, a nickel or copper cathode I have no problem. Whats up with the 316?
Jim CampbellMetal reclamation - Belleville, Ontario, Canada
2004
You will have to strike the 316 with Wood's nickel. 250 g/L nickel chloride 250 mL/L HCl rest water. This will activate 316 to receive any plate.
Guillermo MarrufoMonterrey, NL, Mexico
2004
First of two simultaneous responses --
316 stainless steel, like most stainlesses and many other metals, has a tenacious metal oxide on its surface that inhibits good adhesion of electrodeposits. The best way of eliminating this problem is to use a "strike" layer. I would suggest using either a Woods nickel or possibly a sulphamate nickel. Both formulations are easily available from a wide number of sources.
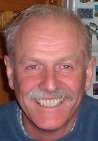
Trevor Crichton
R&D practical scientist
Chesham, Bucks, UK
2004
Second of two simultaneous responses --
I appreciate your response Guillermo, I have used Woods nickels many times in the past to promote good adhesion to stainless steel. Are you thinking about adhesion?. My problem is getting initiation of the deposit, It tends to start very slowly from High cd areas, so I would like to understand why.
Jim Campbell- Belleville, Ontario
2004
Jim,
Sounds like the problem is conductivity of the 316 and an inefficient solution. Try the following: Increase contact points on your cathode. Strike the cathode to get a more conductive surface. woods then copper if allowed should greatly help. lastly, try and improve the efficiency of your solution.
Stephen ParkhurstJob Shop - San Diego
2004
Try cleaning your cathode contact points with a good abrasive paper and then bolt the connectors to the stainless steel. Ensure the area you want to plate is thoroughly cleaned with a good stainless steel cleaning system; get some from a reputable supply house. This will probably involve both acid and alkaline cleaners and probably reversing the polarity. Do not let the stainless steel surface become dry as it will re-oxidise and you will have to repeat the cleaning process.
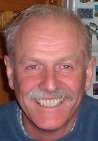
Trevor Crichton
R&D practical scientist
Chesham, Bucks, UK
2004
Q, A, or Comment on THIS thread -or- Start a NEW Thread