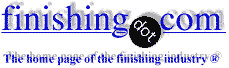
-----
Heat treatment of Electroless Nickel

Q. I HAVE A CUSTOMER ASKING ME TO PLATE .0002 ELECTROLESS NICKEL ON ALUMINUM THEN BAKE PER PROCESS 6061. When I look this up it tells me it depends on thickness and other factors. I cannot find anything that would tell me the length of time. any info would be appreciated.
BLAKE M. FRIGO- WORCESTER MASS.
September 23, 2022
A. Hi Blake. Sorry, I don't not what "per process 6061" means. Are you baking as an adhesion test, or are you baking to harden a high phosphorous electroless nickel deposit?
Luck & Regards,
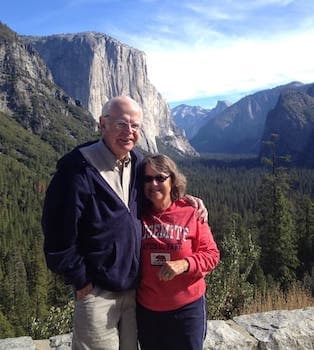
Ted Mooney, P.E. RET
Striving to live Aloha
(Ted is available for instant or longterm help)
finishing.com - Pine Beach, New Jersey
⇩ Related postings, oldest first ⇩
Q. We need to plate a part with Electroless Nickel, high phosphorus to a minimum thickness of 0.003" an as-plated hardness of 46 to 50 Rc, heat treat at 525-575 °F for 2 hours to obtain a final hardness equivalent to 60 -65 Rc. Parts have to pass ASTM B117, copper sulphate ⇦ on eBay or Amazon [affil link] Porosity Test and adhesion test. We've done a lot of EN, but never this thick, mainly for soldering purposes, not hardness.
My questions are:
1.- How much time can pass between the EN plate process and the Heat treatment. According to our lab, the ENi process will take about 6.5 hrs, based on plating rate. We have to send to an outside company for the heat treatment and they can do this the next day, is this satisfactory? Is there a time limit between the 2 stages of the process? What is the maximum time between the two?
2.-We need to test for microhardness, how is this performed?
3.- Our spec is in Rockwell hardness, how is this transferred to Vickers or Knoop? 60 Rc is how much in Vickers?
Thank you very much for your help.
Enrique Segoviaplating shop - Monterrey, Mexico
2004
A. 1. The time between plating and heat treatment for hardness is not important. The coating hardens because of a decomposition reaction of the nickel-phosphorus matrix to Ni3P plus Ni. This will happen whenever the coating is heated. The period can be one day or one week.
2. Microhardness testing is described by ASTM B578-21, which is for Knoop microhardness. However, the same procedures can be used for Vickers.
3. There is no direct conversion between Rockwell and Vickers hardness. ASTM E140 gives conversions for some bulk materials like stainless steel. Charts have also been developed based upon microhardness of standard Rockwell test blocks.
60 HRC is approximately equal to 750 HV. 65 HRC is approximately equal to 900 HV. Your two hour treatment at 550 °F will result in a hardness of about 750 HV. However, be careful not to harden the coating too much. Above a hardness of 800 or 850 HV, the coating will shrink and crack and you will not be able to pass salt fog or copper sulphate.
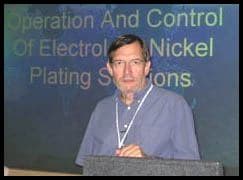
Ron Duncan [deceased]
- LaVergne, Tennessee
It is our sad duty to note Ron's passing on Dec. 15, 2006. A brief obituary opens Episode 13 of our Podcast.
2004
A. Hi, Enrique,
0.003" seems too much just for soldering purposes. Is there another reason for this unusual thickness? Regarding time elapsed between plating and baking, next day should be no problem.
? By the way, what is the substrate?
Monterrey, NL, Mexico
by Sha, Wu, & Keong
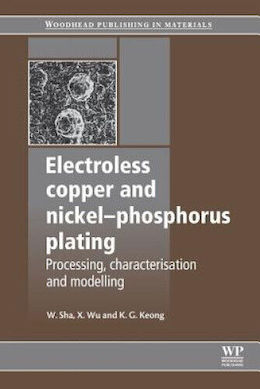
on eBay or Amazon
or AbeBooks
(affil link)
Q. Thanks to Ron and Guillermo,
Guillermo, the process spec is not in this case for soldering, it's mainly for corrosion protection. The parts are made of Cast Stainless Steel type 316. The finish has to be abrasion and wear resistant, the part is a pump component for corrosive liquids. We are required to provide a final hardness of 60 to 65 Rc, according to our client spec with a bake of 2 hours at 525-575 °F We feel the thickness is excessive, even more so because the base metal is SS T316.
Ron, Since the client spec calls for 60-65 Rc (approx. 750-900HV) what do you recommend so that we don't have the shrinkage and crack effect you refer to? Since the part is made of SS I don't think we'll have problems with the porosity test with copper sulphate and the corrosion in Salt Spray (time required 168 Hrs)
We just received back the first samples from the bake operation and we only have hardness in Vickers of 613-634 with a Knoop 10 grams, Hk 10 grms.
Could this be because the temperature is not high enough? I've read that to have a difference in Electroless Nickel hardness we need at least 400 °C for one hour?
Our client specified only 300 °C for 2 hours.
Any help or insight are highly appreciated.
Thanks for your help,
Enrique
Enrique Segovia [returning]Plating Job shop - Monterrey. Mexico
2004
A. There seems to be some confusion or lack of information about your specification. The specified plate thickness seems adequate for the purpose, but if its high or mid phosphorous, heat treating it to obtain the mentioned hardness will make it lose much of its corrosion resistance, which doesn't make sense in your application.
On the other hand, the development of a very low Phosphorous EN has received some attention for its high as-plated hardness of 800-850HV and its very good resistance to chemical attack (supposedly better that high and mid phosphorous when exposed to alkalies). In my opinion, in such case a low temp bake would promote a better adhesion to substrate. Hardness would be OK and corrosion resistance will not suffer much.
Guillermo MarrufoMonterrey, NL, Mexico
by G. G. Gawrilov
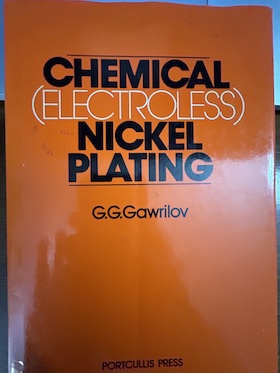
on AbeBooks
or eBay or
Amazon
(affil link)
Q. Guillermo,
Thanks for your response. You know how some clients transfer their requirements for finishing, sometimes without much knowledge about it, or at least less knowledge than us, the finisher. The Client Corporate Spec requires a high phosphorus Electroless Nickel, to a minimum thickness of 0.003" an as-plated hardness of 46 to 50 Rc, heat treat at 525-575° F for 2 hours to obtain a final hardness equivalent to 60 -65 Rc. We have backed other parts to 750° F, never at 525° F.
On the other hand they recently told us that the SS test is only for 168 hours. We don't understand why they specify high corrosion environment and require only 168 hr to SS test. Also, they don't want to change to low phos because their spec doesn't allow for it. Any comments?
Thanks for your help.
Enrique Segovia [returning]Plating job shop - Monterrey, Mexico
2004
A. We have used 600° for 3 hours to get 55-60 Rc scale many times.
Skip Head- Hampton, Virginia
March 21, 2012
Multiple threads merged: please forgive chronology errors and repetition 🙂
Electroless Nickel, Rockwell C, Temperature and Bake times
I'm a quality engineer for a plating company in Dayton Ohio. Currently we are able to vary temperature & time when baking our product after applying an e-nickel coating. I wanted to know if there is a standard available to use for a more consistent process.
EX. - Bake Temp & Time to achieve desired hardness.
Rockwell C Bake Temp Bake Time
45-52 What temp How long
55-60
60-65
62-67
I prepared to perform the test myself, but thought I would ask if there is a standard available for this process.
Thank you.
plating - Dayton, Ohio
2005
![]() |
A. The hardness that results from heat treatment with vary with the amount of phosphorus in the deposit, but Figures 13 and 14 in the Electroless Nickel Chapter in the Metals Handbook Vol. 5 give hardnesses for mid and high phos coatings as a function of time and temperature. ![]() Ron Duncan [deceased] - LaVergne, Tennessee It is our sad duty to note Ron's passing on Dec. 15, 2006. A brief obituary opens Episode 13 of our Podcast. A. You cannot use Rockwell on electroless nickel over steel. You get the influence of the underlying steel. ![]() Robert H Probert Robert H Probert Technical Services ![]() Garner, North Carolina ![]() |
Multiple threads merged: please forgive chronology errors and repetition 🙂
Is Vacuum Necessary for Baking of Electroless Nickel?
We plate Electroless nickel (10% P) on carbon steel substrates. To improve adhesion and hydrogen release bake them at 200 °CC for 4 hours. Our customer demanded heat treatment under vacuum. Is there any advantage in going for vacuum? There is no tarnishing of coating even in normal furnace. Is it really necessary to go for Vacuum? Our customer says this coating (30 microns) is for corrosion resistance. For what type of applications baking under vacuum is needed?
Ram Prasadjob plater - Bangalore, Karnataka, India
September 17, 2008
Conventional furnace may leave surface contamination which in turn may lead to premature corrosion. Also remember that "The one who pays, rules".
Guillermo MarrufoMonterrey, NL, Mexico
Maximum achievable hardness?
Q. In High Phosphorous Electroless Nickel plating, what is the maximum hardness that can be achieved for 0.010-0.012 mm plating thickness after heat treatment? The material is 42 CrMo4v.
Our customer requires HV900-1100. Is it achievable?
Please advise.
- Bangalore, India
August 16, 2013
Q. Our customer requires that we heat treat high phosphorous electroless nickel to 63 HRC minimum. Is there a way to achieve the hardness without discoloration? I understand that inert atmosphere works, but we would like to do it in-house. Any help in this matter would be greatly appreciated.
Dave Vogl- Benton harbor, Michigan
February 5, 2015
A. There is no way that you can check EN hardness with Rockwell C. That testing will be highly affected by the hardness of the substrate. You need a microhardness test such as Vickers.
James Watts- Navarre, Florida
A. Hi Dave,
James is right, you will not be able to directly check Rockwell C on the part, but will need to manufacture a test piece and test that. 63 HRC works out to be about 775 HV. To get high hardness on electroless nickel you will need to heat treat at 400 °C for 1 hour,. if you do not want any discoloration you must either use a vacuum or an inert gas atmosphere.
Aerospace - Yeovil, Somerset, UK
Q. I was trying to heat treat a part which completed its Ni Plate to a thickness .00008" to 0.001", my final hardness should be 400/500 Vickers Hardness (HV100).
Is anyone able to provide me some advice please?
Engineer - Singapore
June 5, 2022
A. Hi Siong. According to this thread, that is not a very high hardness and should not be difficult to achieve. However, the achievable hardness is extremely dependent on the phosphorous content which has not been mentioned yet. What is the substrate, what hardness do you get before heat treatment, have you attempted any heat treatment yet and what were your results when you tried it please? Thanks!
Luck & Regards,
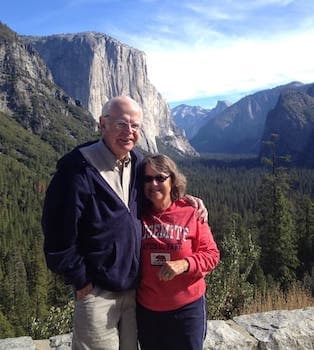
Ted Mooney, P.E. RET
Striving to live Aloha
(Ted is available for instant or longterm help)
finishing.com - Pine Beach, New Jersey
Q, A, or Comment on THIS thread -or- Start a NEW Thread