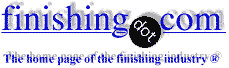
-----
Burning problem in Hard Anodizing of Aluminum

(to help readers new to the process more easily understand the Q&A's)
'Anodizing' of aluminum is an electrolytic process to deposit a finish of engineered aluminum oxide and related compounds on the surface of aluminum parts. 'Hard anodizing' or 'hardcoating' is one type of anodizing optimized for thick, wear-resistant coatings. Our FAQ "Introduction to Anodizing" explains how anodizing is done and the several different types of anodizing.
'Burning', when said in a plating or anodizing context, refers to a defect in the finish caused by trying to proceed at a faster rate than the overall electrochemical situation will support, and it usually results in a rough, bumpy, frosty look with possible discoloring. Because electricity takes the path of least resistance, burning sometimes occurs only on high current density areas of the part such as its corners.
A situation specific to aluminum anodizing is that aluminum is highly conductive, whereas the anodized finish is highly resistive. Because the raw aluminum has almost no resistance, we must start at low voltage or way too much current would flow, causing immediate burning. But we must gradually increase the voltage to keep building the anodized coating because if we maintained low voltage no current would flow through the insulative anodized coating and the process would stop. A consequence of this situation of starting at low voltage and gradually getting to higher voltage is that if a part on the anodizing fixture is making poor contact, it may have no current flowing to it early on, and consequently no anodizing building up on it; then, as the voltage is increased, a sudden breakthrough can occur whereby the part is now conducting but the voltage is already high and it has no resistive anodized coating on it yet, so excessive current flows and it burns.
Another thing that can happen is a part or portion of a part does not have much agitation/solution movement around it, so the plating current causes a heat buildup which indirectly causes burning (the heat doesn't directly cause the burning, but at higher temperature the solution resistance is much lower so too much current flows to that area, and it burns.
Q. I have taken over a metal finishing shop that has lost its employees, and as such, am working through a multitude of issues. When I arrived, Type III was shut down and I wanted a baseline, so I performed a series of titrations. The sulfuric concentration was low at 24 oz/gal or 180 g/l. I have since brought it up to 30 oz/gal or 225 g/l. The aluminum content is 0.5 oz/gal or 3.7 5g/l. There is strong aeration and the chiller is set at 34 deg F or 1.1 deg C. This shop had been producing quality parts just a few months ago, so the issues I've been having are puzzling. I get heavy erosion of the spine at the bottom and burning of the parts at the bottom of the rack. I would have thought insufficient aeration, but this setup (1100 gal SS tank, dedicated blower, 2000 Amp rectifier with ramping - current or voltage) has produced good parts for the previous 3 years. Do you have any ideas?
Steve Taylor- Seattle, Washington
October 14, 2022
Q. So, it appears my problems may have been caused by a number of issues, some of which included the pulse function of the rectifier being set to 2000 A with 100 ms on and 50 ms off. I have since disabled the pulse, and I'm having decent results using the 720 rule method. One of the negatives to my situation is that I have all the current in the world, but voltage is limited to only 40 V, so that limits the maximum current density. Does anyone have a recommendation for initial settings for the pulse? Is there any rule for this? As a percentage of the peak amperage or otherwise?
Steve Taylor [returning]- Seattle, Washington
October 20, 2022
A. Hi Steve. You did very good. Indeed, pulsing parameters are another tiger to tame, and one that you don't want to have loose until you've tamed the other parameters -- so shutting off the pulsing was the right thing to do.
Although not every anodizer and anodizing consultant is sold on pulse anodizing, some are, and the world expert on the subject is probably Dr. Anne Deacon Juhl who did her doctorate on pulse anodizing and has been conducting an anodizing school for several years now. I think you should write to Anne (anodizingschool.com) and see on what basis you can get her help with this question.
Please remind her where you learned about her ... and that she really should be here as an advertiser and a forum contributor :-)
Luck & Regards,
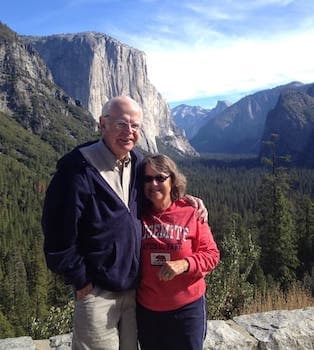
Ted Mooney, P.E. RET
Striving to live Aloha
finishing.com - Pine Beach, New Jersey
A. 1.Unless you are doing heat treated 2024 you will get much better hardcoat (smaller pore) with 180 g/L, 225 is too large pore and not Tabor abrasion passing hard coat.
2. The bottom of the rack is the highest current density, so (1) get 8" off the bottom (2) ramp from zero to the target ASF, 24 ASF) for 15 minutes before setting the current . Be sure the air agitation is not hitting the parts and displacing solution/current.
3. With 40 volts you should get up to 0.001 to 0.0015 inch thick, beyond that the resistance calls for higher voltage to maintain the amps, the amps fall off and the pore gets too large. If you want to do 0.002, you need 60 volts.
I have installed and serviced hundreds of hard coat lines, never found anyone who could prove to me any advantage of pulse, so you better stick with Ted Mooney on that subject.
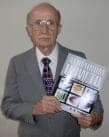
Robert H Probert
Robert H Probert Technical Services

Garner, North Carolina
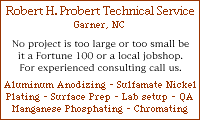
Q. I'm doing a bunch of Type III 2024 sheetmetal (8ga/.125") and have been having to reduce current density to avoid burning, even with strong agitation and good chemistry. Do you think adding glycolic acid would help my situation, and if so, at what concentration? It is an 1150 gallon stainless tank.
Steve Taylor [returning]- Seattle, Washington
December 27, 2022
⇩ Related postings, oldest first ⇩
Q. There is a burn issue with a part that the company I am working for is manufacturing. I am a student working as an intern and do not have expertise with anodizing. These parts are hardcoat anodized and stacked on a pallet, then wrapped with shrink-wrap. They are cylindrical in shape. They do make contact with one another in the current packaging setup. When they are transported to the next operation via forklift many of the parts at the points of contact have "burn" marks. They are blackened and the hardcoat is no longer there. We have used standard shrink-wrap as well as shrink wrap that should dissipate any static charge. It did not work successfully. Why would it be burning, I understand the hardcoat has dielectric properties and should be corrosion and wear resistant. Any suggestions would be greatly appreciated.
Will Potterstudent - York, Pennsylvania, USA
2004
A. I would be amazed if this damage was from static electricity in the packaging. I believe it is either fretting/galling damage (even that is hard to believe), or that the burns were there from the anodizing process.
Are you sure the burns were not there before the parts were stacked?
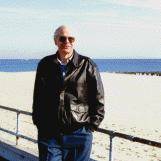
Ted Mooney, P.E.
Striving to live Aloha
finishing.com - Pine Beach, New Jersey
A. There are many places that claim to do hard coat. If it is a real hard coat not just type 2 with more thickness then I doubt it would be worn off.
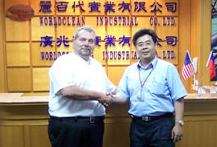
Drew Nosti, CEF
Anodize USA

Ladson, South Carolina
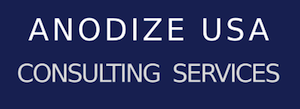
Multiple threads merged: please forgive chronology errors and repetition 🙂
Q. We have hard anodize process in a chemical shop.
Anodize bath contains sulfuric acid (190~210 g/l) and oxalic acid (max.10% of sulfuric acid).
We have been processing mainly "AL 7075-T7451/7175-T7351". But sometimes we get burning on the anodized part (even "melting away").
About 3 Amp-hour/sq.dm is applied at 3 - 5 °C. It is not much current density, I suppose.
My questions are the following:
(1) I was told that oxalic acid helps to make current flow stable in anodize bath. Is that right? What is proper range for oxalic acid?
(2) What should I do to avoid burning defects in hard anodize process?
Thanks in advance.
Fr. Sleepless in Korea.
Dong-cheol ParkAerospace - Busan, Kyungsang-namdo, South Korea
2004
A. Oxalic is old fashioned. Glycolic/Glycerine is the state of the art and protects from burning better than oxalic. Be sure to ramp up very slowly with 7075, be sure to rack so as to GET THE CURRENT ON THE PART.
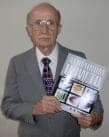
Robert H Probert
Robert H Probert Technical Services

Garner, North Carolina
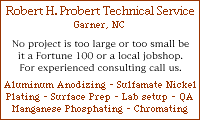
A. Hard coat temps in the 32 °F range, and very very good solution agitation are extremely important. We run at 30 ASF for hard coat.
When the agitation was not sufficient, the aluminum racks as well as some parts would burn.
Get a good rolling solution. I would bet that's where your problem is.
Todd Huehn- Blaine, Minnesota, USA
Thank you.
Agitation is wonderful thing.
I was able to get great hard coating by strong agitation.
Dong-cheol Park [returning]Aerospace - Busan, Kyungsang-namdo, South Korea
Multiple threads merged: please forgive chronology errors and repetition 🙂
Strange type of hardcoat "burn"
Q. Greetings - We have experienced a strange type of hardcoat "burning". The grade is 6061, T6. The "burn" appears as a lighter grey area with a rough surface area, right next to the normal hardcoat deposit. The area is anodized. Has anyone experienced anything similar and figured out what is causing the problem?
Vic Waldmananodizing job shop - Oxford, Connecticut, USA
2004
A. But is this burning in a HCD area, a spot that might be overheated, or a place where for any reason you would suspect burning to occur?
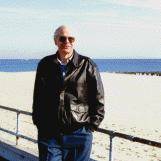
Ted Mooney, P.E.
Striving to live Aloha
finishing.com - Pine Beach, New Jersey
Q. Hi Ted -
Thanks for the response. The "burn" (for lack of a better term) is occurring on the exterior part of a gentle curve. Certainly not a typical HCD area. I don't think there is any overheating going on. What do you think of contamination of some sort?
Vic Waldman [returning]anodizing job shop - Oxford, Connecticut
Multiple threads merged: please forgive chronology errors and repetition 🙂
Q. Hi
Our hard anodize process get more burning on the anodized part about 1-2% .
Anodize bath contains sulfuric acid (140-160 g/l) .
We have been processing mainly "AL 3003 H14". About 37 Ampere/sq.ft is applied at -3 ~ 8'C , operation time is 20 min and hard coat of 1.2 mil that require.
We have 2 line air spargers in 7500 ltr anodize bath.
And then I would like to know how should I do to avoid burning defects in hard anodize process?
Thanks in advance.
Engineer - Thailand
December 7, 2010
A. Better agitation should work. Check your sparger design and placement relative to the parts in a good reference book. If it is OK, You may have to increase the air flow. Eductors work for pumped solution. I would buy one and test it in the lab with air.
James Watts- Navarre, Florida
A. 1. Lower the current density to 24 amps per square foot,
2. be sure the air is not hitting the parts
3. use a hard coat additive, either oxalic or preferably glycolic/glycerine(2%/2%/vol or proprietary)
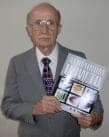
Robert H Probert
Robert H Probert Technical Services

Garner, North Carolina
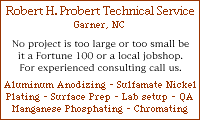
A. Noppachai
Your post suggests that you have not always had this problem. If your operation has not changed, and the problem is new, have you checked your dissolved aluminum content?
- Colorado Springs, Colorado
Thank you very much everybody for your help.
- Thailand
December 14, 2010
Q. For hard anodize bath, is it recommended to work with solution mixing or scrambling conditioning?
IRIS VAX- Tefen, Israel
January 8, 2014
Treatment &
Finishing of
Aluminium and
Its Alloys"
by Wernick, Pinner
& Sheasby
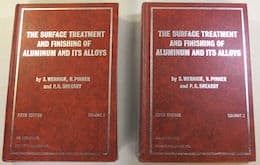
on eBay or Amazon
or AbeBooks
(affil link)
A. Hi Iris. Sorry, but I do not recognize the term "scrambling conditioning" ... maybe you are alluding to turbulent vs. laminar flow?
Hard anodizing requires very good air agitation or eductor agitation, and it is not sufficient to merely agitate the tank contents as a whole. You must provide agitation right at the individual parts because the hard anodizing process generates a lot of heat and the process will not function properly except at its intended operating temperature. Good luck.
Regards,
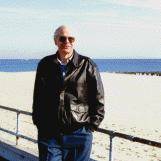
Ted Mooney, P.E.
Striving to live Aloha
finishing.com - Pine Beach, New Jersey
Q. I would like to know how to calculate the power of cooling unit for hard-anodizing.
Data are bathtub depth 1000 millimeters x width 1100 millimeters x length of 2000 millimeters.
The plan is 1500A and 80V
What is the minimum distance to leave between the cathode parts?
- Tefen Israel
A. Hi Iris. The cooling unit must remove from the bath all of the heat that the rectifier adds. If the rectifier were running at 1500A and 80V all of the time, that would be 120,000 Watt-hours per hour or 120 KW-hours per hour or 410,000 BTU/hour, or 34 tons of refrigeration. You can scale this down based on what percentage of the hour the tank is empty, and what the actual amperage and voltage are as the voltage ramps up. If you figure the duty cycle is about 60%, then you need about 20 tons of refrigeration capacity.
The part to part spacing should not be critical for hard anodizing, as long as the parts don't touch each other and don't touch the cathodes, and don't shield each other from generous local agitation. Good luck.
Regards,
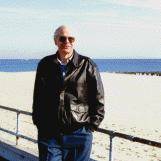
Ted Mooney, P.E.
Striving to live Aloha
finishing.com - Pine Beach, New Jersey
Q. Dear Friends,
I have an issue in hard anodizing, parts get burned. I am using good agitation too; I am using the following parameters:
Concentration of sulfuric acid -- 20% by weight
temperature -- 0 to -5 °C
time -- 45 minutes
current -- 250 amps per square meter
jigs -- Aluminium (by using titanium jigs, parts were getting more burned)
Kindly assist me with what could be the reason of burning the parts after all this arrangement?
In hard anodizing, if concentration of sulfuric acid is less than 10%, then it causes the burning of Aluminium parts which are 7075 T6?
Aijazullah Tajir- Abu Dhabi, UAE
January 26, 2014
A. Hi Aijazullah. Although the chemistry is very important, good chemistry won't help if the racks lose contact, or can't carry the amperage, or if agitation is insufficient to maintain the temperature of the parts.
Based on Robert Probert's earlier posting about rack capacity, and your observation that titanium racks fare worse, my guess is there is a racking issue. Sometimes an experienced anodizer can tell from a fairly quick look where the problem lies; so if such a person can visit, they may be able to offer expeditious help. Good luck.
Regards,
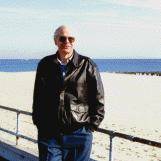
Ted Mooney, P.E.
Striving to live Aloha
finishing.com - Pine Beach, New Jersey
A. At first glance the parameters look OK. A few questions:
1. Are the parts a very thin sheet metal?
2. Where is the burning occurring. At the rack points? In the middle of the parts? On the outer edges?
3. Cathode material, and ratio of the cathodes to the work?
4. Distance from parts to the cathodes?
5. Ramp time?
A picture would help a little bit.
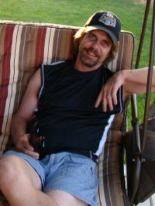
Marc Green
anodizer - Boise, Idaho
Q. Dear friends
Does low concentration (say, less than 10%) of sulfuric acid for hard anodizing cause the burning of parts (7075 T6)?I am using 250 amps/m2 for 45-min, temp 0 to -5 ° C.
- Abu Dhabi, UAE
January 28, 2014
A. 10% by weight would be only 2/3 normal strength and, YES, will surely "burn".
10% by volume of 66 degree Be sulfuric acid is about right and should not burn at your current density. Perhaps the air agitation is hitting the part and displacing solution long and often enough to cause burning, or your temperature is too cold for the alloy and current.
Send us some pictures of the racking and whatever you call "burning".
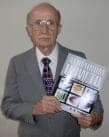
Robert H Probert
Robert H Probert Technical Services

Garner, North Carolina
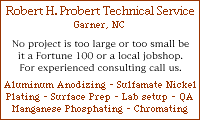
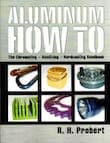
Aluminum How-To
"Chromating - Anodizing - Hardcoating"
by Robert Probert
Also available in Spanish
You'll love this book. Finishing.com has sold almost a thousand copies without a single return request :-)
A. Aijazullah
At 0 °C and 10% acid concentration, your voltage will be higher than at 0 °C and 15% acid concentration. Subsequently the wattage generated will be higher and the need for adequate agitation increased.
Most of the burning I have seen has been the result of inadequate agitation or an excess of dissolved aluminum.
- Colorado Springs, Colorado
A. Regarding Solution make up and air agitation, I would recommend Robert Probert's book, "Aluminum How To" ⇨
It really helped me a ton. For the air agitation in our acid solution we changed our air spargers to induce "micro-bubbles" instead of creating a rolling effect with air, and built new liquid manifolds with eductors. The combination of the two has eliminated almost all shadowing and our burning in minimal.
Best money I spent was on this book.
- Spokane Valley Washington, USA
Tell me the right hard anodizing formulation with glycolic acid
Q. Dear Mr. Robert H Probert
We have an hard anodize process on cookware and various industrial parts. We have an issue of not getting proper black dark colour in hard anodize process. Can you help me to give me proper chemical composition of hard anodize bath what is missing?
We are using sulfuric acid and oxalic acid Anodize bath.
Please sir give me proper chemical composition of hard anodize bath
Can we mix Glycolic/Glycerine in our current bath of sulfuric acid and oxalic acid to protect from burning.
hard anodizing - Gujarat, INDIA
March 29, 2016
Hi Jigar. The previously mentioned "Surface Treatment & Finishing of Aluminum ..." text mentions a Reynolds formula of 15-24% sulfuric acid, 1-2% glycolic acid, and 1-2% glycerol. If Mr. Probert or anyone else can suggest a published work that answers your question, we'll be very happy to post the reference to that book or journal article. Or if you retain Mr. Probert as a consultant, he can of course teach you whatever the two of you agree upon as part of his professional services.
But in this field of hard anodizing additives, where various tweaks of oxalic acid, glycolic acid, glycerine, and miscellaneous substances are held as trade secrets going under a dozen or more different proprietary names, we can't publish such formulations. Thanks for your understanding that, considering the anonymity of the internet, we must guard against new employees accidentally blowing trade secrets, or disgruntled ones deliberately doing so :-)
Regards,
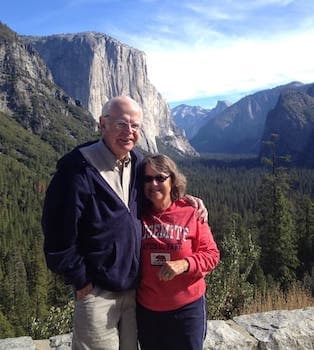
Ted Mooney, P.E. RET
Striving to live Aloha
finishing.com - Pine Beach, New Jersey
Q. Hi!
We are facing burning for hard anodizing; we used 35V / 8 °C / 20%w/v at 30 minutes; Aluminum concentration 2gm/L., we used titanium jig for hard anodizing and the total area of parts is 24 dm2 with Al 6061 alloys, Can anyone help us to solve this problem?
Anthony Aw
- Singapore
October 21, 2016
A. Hi Anthony. The most common hard anodizing temperature in my experience is 0 °C.
8 °C sounds much too warm for conventional practice. Where did that spec come from?
You don't mention ramp control or current limiting on your voltage, but you certainly can't start at 35 volts.
Regards,
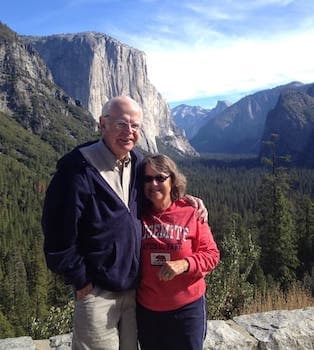
Ted Mooney, P.E. RET
Striving to live Aloha
finishing.com - Pine Beach, New Jersey
![]() |
Q. Hi! - Singapore A. Anthony - Green Mountain Falls. Colorado |
A. I WILLING TO BET MOST OF YOUR BURNING IS TAKING PLACE AT THE BOTTOM OF THE RACK. WE HAVE FOUND THAT REGARDLESS OF HOW GOOD THE AGITATION IS AT TIMES, THIS CAN STILL HAPPEN. YOU MAY WANT TO PLACE AN EMPTY RACK AS A ROBBER ON EACH END OF THE WORK BAR AND YOU MAY CHOOSE TO NOT RACK ON THE BOTTOM OF THE RACK. THIS HAS HELPED US GREATLY, ESPECIALLY WHEN RUNNING PARTS THAT ARE VERY THIN.
CHRIS SMIERCIAKABRAMS AIRBORNE MFG - TUCSON Arizona
Q. Hi readers,
Need some assistance. We do <25 micron anodising and lately having issues burning.
Black color or the silver color anodising is coming out with burns at same spots away from the anode. We have put glycolic acid, and run 20% sulfuric acid.
Checked concentration Al levels, Temperature all in specs.
Current = 1500 A , Load size = 8 sq. m.
Consistent burn marks on the jobs equal distance.
Changed Lead strip cathodes of the burning side.
Please suggest what we might be missing or doing wrong?
AEC - Wellington, New Zealand.
October 27, 2017
A. Hi Anil. If I am understanding you, all parameters are in accordance with specifications which formerly were generating good work. If that is the case, it's hard for me to think of anything besides make-&-break contact or bad agitation nozzles which would cause parts to start burning. Good luck.
Regards,
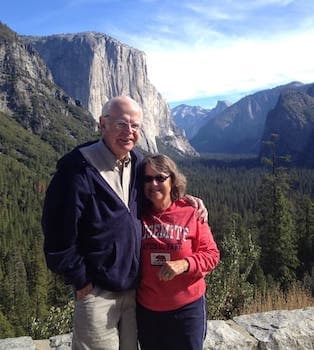
Ted Mooney, P.E. RET
Striving to live Aloha
finishing.com - Pine Beach, New Jersey
Q. Thanks Ted for your time.
I am sharing more details so as to understand the problem a bit better...
We have now welded a polypropylene 5 mm thick sheet to the affected area in the anodiser tank and burns disappear for 2 days and came back again on the same spots but less dense now.
Al conc: 10.9 g/L (12-15 g/L)
sulfuric acid 183 g/L (180-200 g/L)
Temperature: 21 °C (20-22 °C)
We are having hard time getting work through and most pieces are getting burn marks but not as much used to a week and half ago.
Suggestions from the readers welcome.
Thanks in advance.
- Wellington, New Zealand.
November 5, 2017
A. Anil
Your aluminum and sulfuric acid concentration are ok.
Your temperature is ok if you are running regular anodize. 20 °C too high if you are running hard anodize.
Your current density is a little high if you are running regular anodize, and a little low if you are running hard anodize.
If you are running hard anodize you will want to make sure you have adequate agitation. If the burning is occurring in an area where agitation is impaired, you may need to add supplemental agitation.
- Green Mountain Falls, Colorado
A. Sounds a lot like chlorides in the anodizing tank.
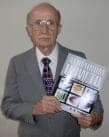
Robert H Probert
Robert H Probert Technical Services

Garner, North Carolina
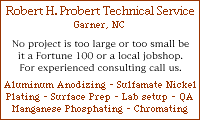
Thanks very much for the great response gentlemen. The root cause for burning (which turned out to be color variation in the end) came out to be something we never would have thought of.
While following the load during anodising I spotted some agitation pipe leakage in the Seal tank. That tiny bubble began at the bottom and took the shape of giant triangles by the time it appeared on the surface, thus causing the vulnerable color layer to come off in the same shape. Repaired the valve and now the issue disappeared. Such a great learning curve.
Thanks again to all.
- Wellington, New Zealand.
Q. Hiya. I work in a metal treatments shop providing conversion coatings along with chromic and sulfuric anodising. We have recently installed a hard anodise line but we're having a problem with a burning issue which we are trying to get to the bottom of.
Test panels that are jigged on Aluminium jigs anodise fine when they are on their own towards the top. But any panels that are jigged towards the bottom seem to always burn. The jig is masked off par contact areas.
The tank is running at 17.3% sulfuric acid concentration, Aluminium content is around 5 g/l along with an Oxidite A-42 additive and the temperature is -1 °C with good agitation provided by eductors. We Hard anodise @ 33amps/ft2.
Could this be down to poor agitation at the bottom of the tank? Or maybe provide a more direct connection on both ends of the jigs help solve this issue? I do see a very slow ramp up helps but not 100% perfect
Any advice would be great.
- Yeovil Somerset
October 13, 2020
A. Hi Danny. Although thin parts can be a problem, if they anodize properly near the top I don't think their thinness or the contact arrangement is the problem.
Slow ramp-up of voltage is of course imperative because the thing that is preventing excessive current is the resistance of the anodized film, so burning will occur if slow ramp-up is not achieved. This is why parts with poor contact burn: they don't slowly build up a film but instead, when the voltage is high enough to 'break through' whatever is deficient in the contacts, highly conductive aluminum is exposed to high voltage and conducts too much current.
In your case I'd be pretty confident that the problem is in fact agitation. Hard anodizing, with its high voltages & high currents produces a lot of heat, and the solution in the immediate vicinity of the part will ruinously heat up very quickly unless there is excellent agitation right on the part. Agitation which is adequate for Type I and Type II anodizing will not be adequate for Type III and its much higher heat generation and cooling requirement. But Chris S's answer on this thread is interesting.
Luck & Regards,
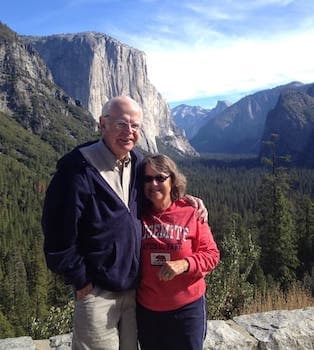
Ted Mooney, P.E. RET
Striving to live Aloha
finishing.com - Pine Beach, New Jersey
A. Sometimes the best way to answer a question is with a question. So let's start this way: How far do your cathodes go down into the tank? They should go to the bottom of your parts on the rack but really no lower. Also if it is agitation. I would try turning the air off using non-production parts to see if burning gets worse. If it does then increase the air until burning is reduced. It's a start
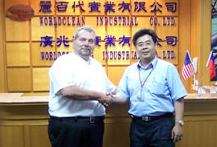
Drew Nosti, CEF
Anodize USA

Ladson, South Carolina
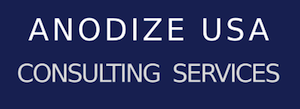
Q. Which is the best way to calculate air agitation for hard anodizing? Flow volume per liter or flow volume per tank size
dangfang bryan- singapore
February 16, 2021
A. Hi, Danfang. Those values are more or less the same thing since tank size can be expressed in terms of volume. But I think the question is an excellent one because, while air agitation serves several different purposes in plating and anodizing, in hardcoat anodizing its foremost mission is probably heat removal from the parts and the solution touching them because so much power/heat is produced and the acid is more aggressive at higher temperatures.
Wernick, Pinner & Sheasby says the thinner the components, the more agitation is needed, but also quotes a number from Turner of up to 0.45 m3 of air per m2 of tank surface. That sounds good to me.
Luck & Regards,
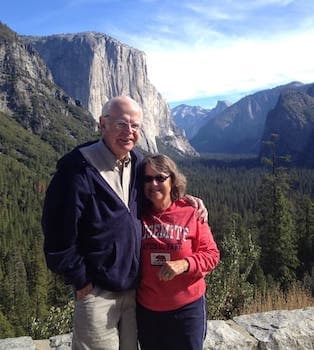
Ted Mooney, P.E. RET
Striving to live Aloha
finishing.com - Pine Beach, New Jersey
Q. Hi, we are currently having problems with our hard sulfuric anodize, currently parameters are:
total acid 123 g/L
aluminum concentration 12.6 g/L
temperature 35±5 °F
And the problem is that every time now when we run any type of aluminum alloy after 20 or 30 min in the bath and when the operator stars to increase the volts at around 35 volts the bath starts to eat the racks and the parts.
Even when we do the ramping procedure, so we have not been able to figure this out, may be its because the acid concentration is low or i don't know to be honest, so if anyone here can give me some tips or explain the why or give me an answer i will appreciated.
Best regards.
- Anaheim California
July 22, 2021
A. Hi Hassan. There are a number of possibilities, perhaps including Cl- in your bath or other solution imbalance, but if you consistently have a problem only at higher power input, my guess is that you have inadequate agitation and cooling.
Luck & Regards,
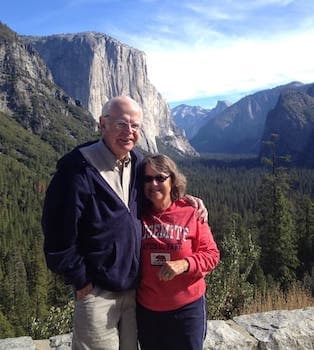
Ted Mooney, P.E. RET
Striving to live Aloha
finishing.com - Pine Beach, New Jersey
A. Obviously the acid is way too low, it is a certain burning recipe, get the acid up to 180 g/L, and call us back.
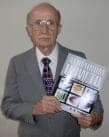
Robert H Probert
Robert H Probert Technical Services

Garner, North Carolina
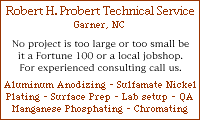
A. Hassan
If your total acid is 123 g/l and dissolved aluminum 12.6 g/l, your free acid is likely ~ 50 - 60 g/l.
I believe Robert is suggesting you raise your free acid content to ~180 g/l. At your current concentration, the best you can hope for is a thin film.
- Green Mountain Falls, Colorado
Q. Working with 6061 pieces that appear to have burned at the rack leaving a distinctly shiny spot. This shiny spot is surrounded by a dull black finish of a type III coating that's fairly uniform over the rest of the part. Looks like a coating is applied. I'm trying to identify the problem with the shiny spot. It's cosmetically flawed, and I'd like to hear suggestions how to correct it.
- Chicago, Illinois
May 25, 2022
A. Hello namesake. Pardon my lack of imagination, but I don't understand the pic. Is this a single louvered component or a stack of parts? And what is with all the scratches and gouges, and the sharp but ragged edges -- it looks like the parts haven't been mechanically finished whatsoever.
It doesn't seem to be a case of poor contact because that would probably evidence itself across the entire part, not a section of it.
The temperature of the bath is 32 °F or lower and you have excellent agitation? Are you certain that the part(s) was waterbreak-free clean before the other process steps? Is this a new problem in a long established process or are you just starting up?
Luck & Regards,
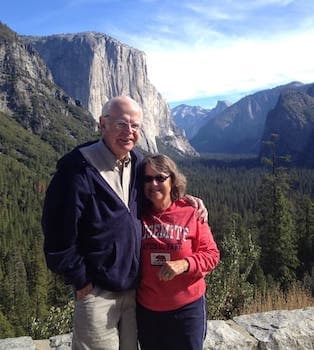
Ted Mooney, P.E. RET
Striving to live Aloha
finishing.com - Pine Beach, New Jersey
A. Until you send us more data, my first guess is that "weathered" oxide was not removed by your deox. It looks like the parts had been stacked for some long time, the exposed edges then covered with natural oxide so thick that the deox could not remove. The plain dark spots would have been the NON-exposed edges during the formation of the weathered oxide.
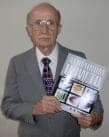
Robert H Probert
Robert H Probert Technical Services

Garner, North Carolina
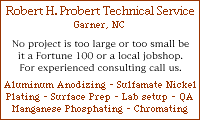
(to provide context, hopefully helping readers more quickly understand the Q&A's)
Although stripping and re-anodizing is usually a viable process, it is important for readers who are new to anodizing to recognize one very important distinction between stripping & re-anodizing compared to the stripping & replating they may be familiar with ...
The anodized layer is produced by a reaction between the raw aluminum on the surface and the oxygen produced by the process -- so, aluminum is consumed in anodizing, and when a component has been anodized and stripped, it will be thinner/smaller than the original part was. As a rule-of-thumb 50% of the anodizing thickness came from the aluminum. Example: if you've hardcoat anodized to 0.002" thickness, when you strip that anodizing you will have lost about 0.001" of aluminum.
Q. No doubt we have some common ancestors, Ted.
These are stacked parts. The saw marks are rather deep, so we didn't take the part surface down to remove these. The parts are deburred, degreased, and burnished. There's some dust on the pieces shown.
On further inspection this is not a burn. This is black marker ink spot over silver rack marks. The shop was a bit heavy handed with the marker. The rack marks are slightly smaller than the ink spots. Because the sharpie ink comes off with a paper towel, it's not ideal for us.
What is our best cost effective solution? Strip and rerun the parts with a better rack setup? Or brush anodizing over the rack spots? What is possible/cost effective? Thanks in advance.
- Chicago, Illinois
May 26, 2022
Electrochemical Metallizing by Marv Rubinstein
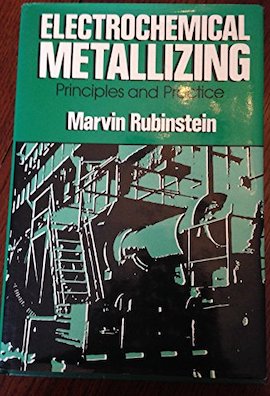
on eBay or Amazon
or AbeBooks
(affil link)
A. Hi again. Although brush anodizing is possible it is usually prohibitively difficult and expensive, and insufficiently aesthetic, for this sort of repair. The best repair is usually to strip and re-do the anodizing.
Luck & Regards,
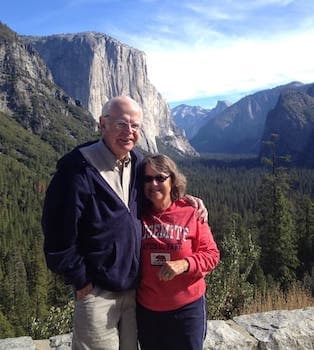
Ted Mooney, P.E. RET
Striving to live Aloha
finishing.com - Pine Beach, New Jersey
Q, A, or Comment on THIS thread -or- Start a NEW Thread