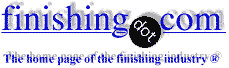
-----
Problems & solutions in heat treating electroless nickel plating

by G. G. Gawrilov
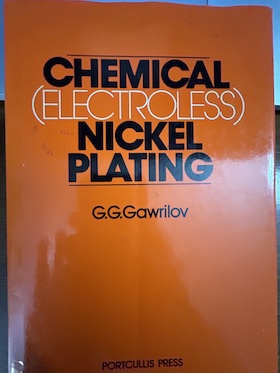
on AbeBooks
or eBay or
Amazon
(affil link)
Q. The electroless nickel coating turned yellow as I tried to heat treated the coating for hardness, 1 hour at 300 °C. Why did it turn yellow and how can I prevent it? Thanks for any advice.
Angus Chow- Hong Kong
2002
A. Try wrapping tightly in aluminum foil for an inexpensive method, or use an inert atmosphere oven.
Rick Richardson, MSFDayton, Ohio
2002
Electroless Ni plating peeling off after heat treatment
Q. Sir,
We are doing Electroless Nickel plating on a Mazak-5 component. It was given a copper strike before Electroless Nickel plating. After EN plating we heat treat for 2 hrs at 200 °C. But Plating peels off or bubbling occurs. What is the reason?
B.NirupamaPlating shop - Chennai, Tamilnadu, India
2004
![]() |
A. What is the substrate material? What process sequence are you using and where is the separation taking place, from the base metal or is it delaminating from the first copper layer? Guillermo MarrufoMonterrey, NL, Mexico 2004 ---- A. Too little copper can result in loss of adhesion after heating. Copper and zinc alloy together, copper diffuses into the zinc leaving the nickel with nothing to adhere to. Solution: increase the copper thickness to 6 microns. ![]() Don Baudrand Consultant - Poulsbo, Washington (Don is co-author of "Plating on Plastics" [on Amazon or AbeBooks affil links] and "Plating ABS Plastics" [on Amazon or eBay or AbeBooks affil links]) 2004 |
A. Mr Nirupama,
Please check the pretreatment cycle prior to Cyanide Copper strike. There should be no water breaks.
Please check the mazak is not porous and the bubbling is actually entrapped plating solution bleeding out on heating to 200 °C.
Check the peeled off Nickel. If the base of the peel off is Copper colored it signifies poor pre treatment. If it is Nickel colored it signifies poor adhesion between the Copper strike and nickel. This indicates the lack of good rinsing and a sulfuric acid 5 percent (room temp 30 sec activation dip).
Good Luck.
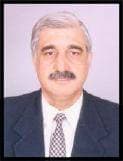
Asif Nurie [deceased]
- New Delhi, India
With deep regret we sadly advise that Asif passed away on Jan 24, 2016
2004
A. Mazak 5 is also known as Zamak 5 is a zinc die casting alloy containing 4 Al + 1 Cu. Don is correct that too little copper can cause adhesion problems. However, another possible cause is the zinc casting itself. This alloy will form an aluminum rich surface layer that freezes first during casting. This layer sometimes blisters from the rest of the casting after heat treatment. This can be confirmed by picking the blister off and examining its back side to see if it is zinc or copper or EN.
If the casting is blistering, it may be necessary to etch the surface layer off before plating with dilute sulfuric acid.
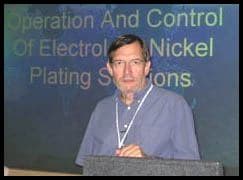
Ron Duncan [deceased]
- LaVergne, Tennessee
It is our sad duty to note Ron's passing on Dec. 15, 2006. A brief obituary opens Episode 13 of our Podcast.
Q. Sir we are facing the same problem. When we peel off the zinc comes out with copper layer what is the solution for this. Please advise.
Umesh Kumar Sharma- Aligarh, India
August 27, 2009
----
Ed. note: Asif Nurie says it's poor pretreatment. Are you electrocleaning, and with a proper formulation? Are you acid activating? Are you sure you have a waterbreak-free surface? Are you certain the diecastings are zinc, not aluminum-rich?
2006
Q. We are producing a machine that contains copper parts used for heat transfer. Our vendor puts electroless nickel on the copper parts for corrosion and abrasion resistance reasons. I would like to improve the abrasion resistance.
The plating I call out now is:
"ELECTROLESS NICKEL, LEAD FREE, 0.0005/0.0002 THICK PER ASTM B733 TYPE 1, SERVICE CONDITION SC1 TO SC2, CLASS 2 HARDENED 20 hours at 260 °C.
I am considering:
"ELECTROLESS NICKEL, LEAD FREE, 0.0015/0.001 THICK PER ASTM B733 TYPE III, SERVICE CONDITION SC3, CLASS 2 HARDENED HARDENED 20 hours at 260 °C"
Question #1 The parts develop a bluish scale when taken above approx. 280 °C. The spec says 360 to 390 °C heat treat for type III. Would 20 hours at 260 °C (as shown above) yield 64 to 74 Rockwell C, or is the 360 °C temp essential?
Question#2 If we go with 360 °C, is it common to heat treat in an atmosphere that does not "scale" the part? Nitrogen?
Question#3 Is there anything else I can do to increase abrasion resistance?
Question #4 Will chrome or other plating yield better corrosion resistance?
Thanks for your help! We'll need 5000 parts a month plated next year so I'd like to make this improvement quickly.
- Skokie, Illinois , USA
![]() |
If you need abrasion resistance, hardness alone will not tell you the full story. You should specify a Taber abrasion resistance test. Rockwell C scale is not suitable for thin coatings because the indenter perforates it giving you a false value from the substrate. You must specify Vickers or Knoop scale. Heating in an inert atmosphere or under vacuum stops the scale. The maximum hardness for EN comes at 400oC one hour, but the temperature to which you take your parts depends, among other things, on the tendency to distort them. Chrome is generally less corrosion resistant, more so in presence of certain environments such as those containing halides and because it often has cracks. It also does not coat uniformly as EN does. Guillermo MarrufoMonterrey, NL, Mexico 2006 Your type 1 EN does not have enough thickness to have a significant abrasion resistance because it is so thin on a relatively soft metal. It would do better if it was on hardened steel, but it still would not be great. Your type 3 should offer a major improvement. - Navarre, Florida |
Question 1. There is not much data on low phosphorous coatings hardened at lower temperatures for longer periods, but these alloys react generally at lower temperatures. So I would expect that 20 hours at 260C would produce full hardness in the coating, approx. 950 VHN. I also expect that it will be bluish in color if treated in air.
Question 2. Inert atmospheres are often used for higher temperatures to prevent the bluish color. Nitrogen often has enough oxygen and water present to react and form the bluish color. Vacuum treatment are much more successful in prevent discoloration.
Question 3. You probably do not need to harden the low phosphorous EN to obtain improved abrasion resistance. The Taber Wear Index of a Type III coating is about 10-11 mg/1000 cycles in the as-deposited condition, which is the same as a fully hardened Type I, IV, or V coating (1000-1100 VHN).
Further, hardening EN coatings causes them to shrink and can reduce their corrosion resistance significantly. For best corrosion resistance, as-deposited coatings are best.
Question 4. Chromium and other coatings generally have much poorer corrosion resistance than as-deposited Ni-P, and especially than high phos EN.
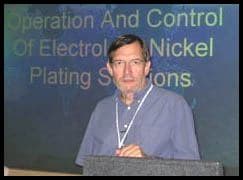
Ron Duncan [deceased]
- LaVergne, Tennessee
It is our sad duty to note Ron's passing on Dec. 15, 2006. A brief obituary opens Episode 13 of our Podcast.
Hardness varies within a batch for unknown reason
by Sha, Wu, & Keong
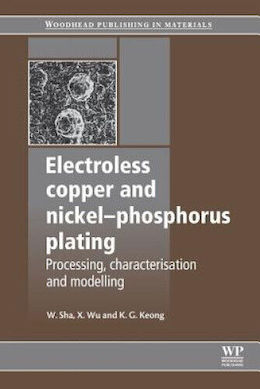
on eBay or Amazon
or AbeBooks
(affil link)
Q. We have been doing electroless nickel plating (mid phos) and always achieved hardness of 900 HV+ after baking at 400 °C for 2 hrs. Recently we have observed that some pieces in a particular batch achieve lower hardness after baking (around 700-750) whereas others are in the range of 950-1000. These low hardness pieces are also darker in colour (greenish-grey).
How does pH effect hardness?
What could be the possible cause for such low hardness/ variation in the same batch. The batch taken for baking consists of material up to 2 MTO.
Please suggest.
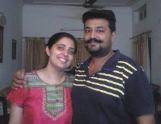
Vikram Dogra
Irusha India - Chandigarh, India
February 6, 2009
A. Hi
Is it a Hot air oven? Is the chamber comparatively bigger than required for your volume?
If so, one of the reasons could be the temp may not be uniform at all corners of the chamber.
If the components are wet, all of a sudden when exposed to elevated temp the color changes to gray/greenish gray (oxidation).
Regards,
- Chennai, India
February 12, 2009
Q, A, or Comment on THIS thread -or- Start a NEW Thread