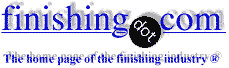
-----
Black and streaked deposits of EN coating
Q. I set up a new electroless nickel plating shop. After stripping the tank with nitric acid and cleaning with DI water, the EN coating of the 1st to 3rd runs is always black and streaked on part edge for more than 10 hours deposition. The EN coating performance after the 3rd run is always good.
I suspect there is nitric acid contaminant in the pipe and somewhere, but I'm not sure. In the 1st to 3rd run, the black and streaked deposits will not occur when the deposition time is less than 10 hours. What's wrong in my process? How can I clean the tank and prevent from the nitric acid contaminant?
Rivon Paiplating shop - Taichung, Taiwan, R.O.C
2004
A. It is very difficult to give you an answer since only the vendor of your chemistry knows what's in it. I can only say that nitric is a venom and kills the catalytic reaction in most acid formulations, so it is not likely to be the cause. It may be something else such as a slight imbalance of the make-up chemistry that improves over time with replenishment and work. Have you tried preparing a new bath without leaching the tank, or vice-versa to see what happens?
Guillermo MarrufoMonterrey, NL, Mexico
2004
A. Nitric acid indeed could be the cause of your problem. The addition of sulfamic acid will mitigate small amounts of nitric acid. But the best solution is to use sulfuric acid/hydrogen peroxide to strip the tanks thus eliminating nitrates altogether.
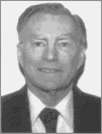
Don Baudrand
Consultant - Poulsbo, Washington
(Don is co-author of "Plating on Plastics" [on Amazon or AbeBooks affil links]
and "Plating ABS Plastics" [on Amazon or eBay or AbeBooks affil links])
2004
A. After stripping a tank with nitric acid (or with sulfuric/peroxide), drain as much of the acid as possible, then fill the tank with water, add enough ammonia ⇦ on eBay or Amazon [affil link] or potassium carbonate to raise the pH to at least seven, and recirculate the solution for at least 15 minutes. Then drain the neutralizer water solution, and thoroughly rinse the tank (preferably by filling it) with DI water. You can purchase nitrate test papers to check that the rinse water is free of nitrates.
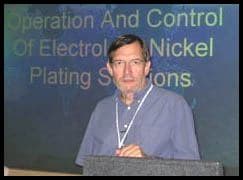
Ron Duncan [deceased]
- LaVergne, Tennessee
It is our sad duty to note Ron's passing on Dec. 15, 2006. A brief obituary opens Episode 13 of our Podcast.
2004
A. Rivon,
You do not say if the "1st to 3rd" runs after stripping out the tank are a new bath make-up -- a critical piece of information. If you put back into service a bath that was working fine before strip-out, it would make sense that you have a contamination problem, either from the Nitric or from your pumps or the holding tank.
If it is a new make-up, you have a problem with the EN formulation. Not that it is "bad", just that it does not fit your situation. What is your bath loading? In the 10 HR run time, How many metal turns do you use? Are you titrating and adding back to the solution frequently enough to NEVER add back more than 10% of the bath make-up ? If you are under-loading the bath I would NEVER exceed 5% addition. Are you maintaining the PH in the recommended range? Do you have a roughness or tank plate-out condition? Have you tried reducing your agitation on the first 3 runs?
I would suggest that you are using a bath that is high in stabilizer and or brightener for your bath loading. Mostly in the make-up Chemistry. Which could be why you are having success after 3 runs.
Awaiting more detail,
Plating Job Shop - San Diego
2004
2004
Q. Dear Steve:
Thanks for your reply.
No matter whether the bath is a new bath make-up or an used bath, the "1st to 3rd" runs after stripping out the tank get the black and streaked deposition. Usually, at the 1st and 2nd run almost all the work parts failed, and at the 3rd run half of work parts succeeded. At the 4th run the yield is almost 100%. I supply some information about my process according to your questions.
1.My bath loading is 1~1.5 dm^2/L.
2.Titrating and adding back to the solution frequently enough to NEVER add back more than 10% of the bath make-up.
3.I maintain the PH in the recommended range.
4.When the bath is about 5 to 6 turnovers, the bath has a roughness condition and sometimes has tank plate-out condition. When the bath is less than 4 turnover, there is not any roughness and tank plate-out.
5.I have tried reducing agitation on the first 3 runs. It still has the same results.
Waiting for your suggestion.
- Taichung, Taiwan
A. Rivon,
I was thinking more along the lines of a EN chemistry problem, and I still believe that, I have never seen a small amount of nitrates cause a major problem. If you have gross contamination it will shut the bath down. So now I have more questions. Could you better define what you mean by "run" as in the first to third "runs"? What TYPE of EN are you using? Phosphorous content? Is it one of the CAD and LEAD free formulations? What size is your bath? Are you using air agitation or solution sparging? If you are not having a tank plate-out condition until after 4 turns, why are you passivating with nitric before this? What material are you plating,and what is your required EN thickness? What is your tank material? Are your properly leaching your filters before use?
The bath loading may be a little low, have you tried increasing the load size?
#4 above concerns me, It says to me that the problem may be low stabilizer in the add back chemistry, and high stabilizer in the make-up chemistry, my first analysis, but if this was the main problem, when you passivated the tank and returned the used chemistry, it should have worked like before you passivated the tank!
As I await your response, here may be some quick solutions.
Avoid nitric all together by using Liners in your tank, use them for a few turns and dispose of them. Or, pump out your tank more frequently and manually clean the tank walls- if you do this often enough you may never need the nitric.(If this is truly the bad guy)
Re-plumb your tank, install clean outs in the lowest points of your plumbing so you KNOW you will properly rinse after passivation.
You will find the answer, Steve.
Job Shop - San Diego
A. Hi Pivon,
Try to use ammonia with water to pump at last step in your EN tank and the filtered, before you fill the tank with EN solution. Often black deposit can come from water rinses with sulfuric contamination, but this happens after EN plating and rinses.
Regards,
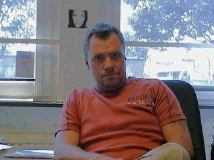
Anders Sundman
4th Generation Surface Engineering
Consultant - Arvika,
Sweden
2004
2004
Q. Hi, Steve:
At first, reply your questions.
1."Run" means a process to get 180 µm thickness.
2. The EN solution is the type of nickel sulphate and sodium hypophosphite. The pH is controlled by NaOH, not by ammonium.
3.The P content is about 11 wt%.
4.CAD or LEAD is not in this EN system.
5.My EN bath is only 4L, but the solution is from and back to a regulated bath with 50 L volume.
6.I am using both air agitation and mechanical vibration.
7.My tank material is SUS 316 and it is passivating during the process. It's not easy to have tank plate-out for this design. But the PP pipe of filtration pump (in the regulation tank) is very easy to plate-out.
8.Why I passivate the tank before 4 turns? I want to know if the black is induced by the new set-up solution or by the tank passivation.
9.I leach my filters before use.
10.It's very difficult to increase the load. The work part is deposited only a little area and is masked most of the area.
I agree with your opinion, it should be a EN chemistry problem. Recently, I tested the 4th again, it got the only 50% yield. The agent of EN solution reveal that the pH additive is NaOH with some chemistry to inhibit the Nickel hydroxide. I tried diluting pH additive by some NaOH solution to decrease the inhibitor content.The black and streaked deposit is solved but the little bulges appear on some work part.
Best Regards,
- Taichung, Taiwan
Q. I have a few internal camera parts that are brass, finished with electroless nickel (don't know the type). After ultrasonic cleaning and an ultrasonic rinse in DI water, they showed a black discoloration. Our DI ion exchange tanks had gotten saturated and were passing less than excellent DI water.
Is there a reasonably innocuous method to remove the black and "re-brighten" the nickel finish? I'm looking at a few websites that recommend a fairly strong mix of hydrochloric and sulfuric acids. I'm also considering a commercial gun bluing remover.
The DI water service man is on the way with new tanks as I type.
Thanks for your help,
manufacturing engineer - Trenton, New Jersey, USA
December 6, 2013
A. Hello Norm,
I have touched up parts that had blemishes in EN before with success. I used a wet scotch brite pad and "blended" the finish around the defect, cleaned, re-activated and went back into the EN. The parts in your photos however look all black. This could be the photo color quality though. I am not sure if my method would help you, and would depend on the severity of the defect. The finish may have to be stripped. There are Ni strippers available on the market if you can't scrap the parts. If you do a lot of EN, it's a good idea to have a strip tank in place. Let the supplier of the stripper know the type of EN and that brass is the base metal. Be careful with internet home brew products and having to mix strong acids. A Ni strip supplier can furnish the product to you ready to use. Good Luck to you.
Process Engineer - Malone, New York, USA
December 19, 2013
A. Blue Magic polish will work ⇨BR You can get at any auto store.
Casey Weizel, PresidentForesight Finishing LLC

- Tempe, Arizona
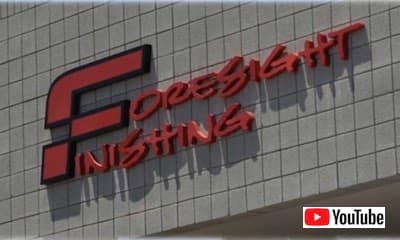
December 20, 2013
The black discoloration was pretty much on 100% of the surface. I had it in my head to remove it the way it went on, by immersion in chemistry. I tried several different brands of C-L-R and they seem to be all the same chemistry. They may work for some things, but not this. I finally removed the black with a very fine ScotchBrite pad, working under water. The parts are now usable and cosmetically pretty.
Blue metal polish would have been my next step. Thanks.
BTW, I had to have my DI water ion exchange resin tanks changed twice more, a week apart. Typically, they've been good for two or three months. The service tech tells me that it may be due to road salt runoff. We'll see how long this set of tanks last.
Thanks to all,
Norm
manufacturing engineer - Trenton, New Jersey, USA
December 23, 2013
Q, A, or Comment on THIS thread -or- Start a NEW Thread