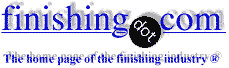
-----
uneven weight loss in etching
Hi, We are an anodising and powder coating company based in S.India.We usually process 6063 alloys for architectural applications.We are running a long life etch with the usual caustic/Sodium gluconate/sodium thiosulphate ⇦ on eBay or Amazon [affil link] /wetting agent at 60-65 °C. We have noticed that some sections get etched beautifully within ten minutes while others (mostly hollow )sections take no less than 20 minutes for the same quality of etch. this results in more weight loss which some customers object to. Can any of you help me by giving some leads on why this happens and how to overcome this? Thanks
Jothi Ramalingam- madras, India
1999
From your comments, I would guess that it is temperature related. Heavy pieces come up to temp a lot slower than lighter ones as well as hollow ones would have nearly double the surface area to absorb heat from the solution. It is also possible that a large load is dropping the temperature of the entire tank with the probability of assymetrical heating, IE: the side nearest the heaters gets the heat first and gets the most. I would take a piece that is a problem child and put it into a hot water rinse tank and then go into the etch tank. You will probably come up with near the same time as the hollow parts, possibly shorter. I would not use the seal tank as it is too hot. If this comes out great, then your problem is temperature dependent and there are several ways to attack the problem. If not, hopefully someone else will have the answer.
James Watts- Navarre, Florida
1999
Q, A, or Comment on THIS thread -or- Start a NEW Thread