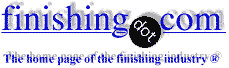
-----
Citric Acid vs. Nitric Acid Passivation

this text gets replaced with bannerText
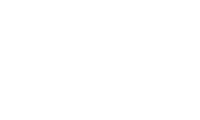
[editor appended this entry to this thread which already addresses it in lieu of spawning a duplicative thread]
Q. Our shop has done type II and Type IV Nitric/dichromate passivating for years. There is now interest in Citrate formulations. Any comments as to the pros and/or cons of Citrate chemistry?
- Clifton Springs, New York
September 26, 2023
A. No, sorry, no one has ever expressed an opinion on that subject on this site :-(
Seriously though, it was a constant subject here for years :-)
This thread and topic 39330 cover most of it, but searching the site for "passivation citric vs. nitric" will show even more.
Luck & Regards,
Ted Mooney, P.E. RET
Striving to live Aloha
(Ted can offer longterm or instant help)
finishing.com - Pine Beach, New Jersey
A. Gary,
Besides the removal of the hazardous chemicals and the ability, if done correctly, to run a single bath for all grades, one of the major distinctions of citric is the lack of removal of chromium and nickel from the surface. The pro is that unwanted etching is greatly reduced if not eliminated, and depth of iron removal is greater. The con is that any desired etching is eliminated as well, such as the "frosted" look that a handful of people have come to expect from nitric-passivated parts. I've also come to suspect that surface pores, such as are found on many castings, get opened up a little by nitric passivation, making them less of a corrosion hotspot.
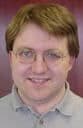
Ray Kremer
Stellar Solutions, Inc.

McHenry, Illinois
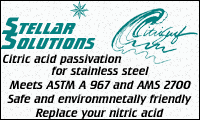
September 29, 2023
⇩ Related postings, oldest first ⇩
Q. We are a laser job shop that has in the past two years added an electropolishing and passivation line. We currently only offer citric acid passivation. From time to time we get people asking us to do nitric acid passivation. Everything that have I have read tends to suggest that citric acid passivation is equal to or better than nitric acid passivation. Can anyone shed some light on this for me? Since we are a job shop we work on all kinds of alloys. I am hoping that citric acid is the best overall passivation method.
Furthermore, nitric acid presents all kinds of hazards that I would like to stay away from.
electropolisher - Monroe, Connecticut
2004
A. According to ASTM specification you are allowed to use either nitric acid or citric acid based solutions. As a fact we have data that confirms the citric based solution will provide superior passivation promoting a higher ration of chromium oxide to iron oxide on the surface than nitric acid.
Also for 400 series stainless you need to use sodium dichromate with nitric to prevent attack on the stainless, and everyone is trying to eliminate chromates in processing.
Citric by itself will not function for 400 series or high sulfur stainless alloys such as 303, 420, 430, 440. Commercial citric preparations are available for these alloys.
Best regards,
- Lake Zurich, Illinois
Thank you. Can this possibly be the same Dayton Dailey from 40 years ago at Allied Kelite?
- Victor, NY
September 28, 2023
Ed. note: We forwarded your message to the last e-mail address we had for him, but that was from 2012. If it reaches him, no doubt he'll respond to you privately.
A. Citric acid removes iron from the surface - PERIOD ! Nitric Acid removes iron from the surface AND also control oxidizes the nickel in the surface to prevent it from uncontrolled tarnish. The Mil Spec has more clarification in this issue.
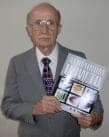
Robert H Probert
Robert H Probert Technical Services

Garner, North Carolina
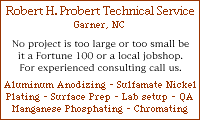
A. I hate to get this thread going again, but here we go. citric acid is a chelator only, as Bob Probert says. Chelating, or tying up the iron on the surface may pass as passivation in some circles. Nitric removes iron on the surface and into the metal some 10 angstroms and therefore is a better passivator (usually). If the operator allows the nitric solution to become saturated with iron, it becomes an iron immersion bath. Hence, the orange or brown parts described in past inquiries. Why would someone allow the solution to get that way? Check the price of nitric and then check the price of disposing of the spent solution.
Electro-Passivation is the next best of passivating by yielding a 15 or so angstrom penetration of iron removal. Electropolishing is the acknowledged best method with a 20 angstrom penetration. These numbers were established using auger electron spectroscopy and are subject to interpretation as is everything in our business, but are at least a starting point for the discussion.
- Toccoa, Georgia
Q. My company uses many stainless steel investment cast parts and we have usually specified QQ-P-35C (canceled) [link is to free spec at Defense Logistics Agency, dla.mil]C on our drawing as the specification to be adhered to for passivation. We have recently switched to ASTM A967 as the standard to be followed which raises many questions between vendors as it outlines many different concentrations of citric and nitric acids. I would like experienced feedback on which concentration of nitric or citric acid to be used to passivate CF8M(316) investment cast parts after they have been quenched either with water (non-preferred) or nitrogen.
Thank you for your attention and feedback!
Manufacturing - Minneapolis, Minnesota, USA
2004
A. I also hate to go over this again online. But the record must be set straight. I am not sure why some people keep ignoring the hundreds of tests that have been run by INDEPENDENT sources such as universities, etc., all of which show that properly formulated citric acid formulations yield much BETTER passivation, DEEPER penetration into the stainless steel, BETTER corrosion resistance in all test methods, SAFER, EASIER and MORE COST EFFECTIVE. Electropolishing followed by proper passivation yields even better performance.
Nitric acid DOES NOT add oxygen to the surface of stainless steel. It "chemically removes iron (along with nickel and chromium, etc.)and chemically oxidizes the surface (not adding oxygen until it comes in contact with the air or other oxygen donor). The same thing happens with properly formulated citric systems, only without removing the chromium and nickel. This is why many major corporations worldwide have switched to citric formulations that give BETTER passivation performance. Anyone interested in independent test data proving this can contact us.
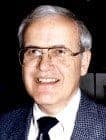

Lee Kremer
Stellar Solutions, Inc.

McHenry, Illinois
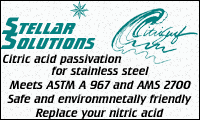
A. Passivation in nitric acid or citric acid cause acid penetration into deep hard to reach pores. Even with thorough rinsing you cannot remove all acid from such pores. These pores are the origin of local surface corrosion, while other area is passive. We suggest to rinse metal parts after passivation in diluted alkali solution. As an example of such solution: Na2HPO4 + NaNO3 with pH 8-9. There are other effective neutralizing rinsing solutions that can be selected for specific metal alloy and specific metal parts.
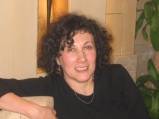
Anna Berkovich
Russamer Lab

Pittsburgh, Pennsylvania
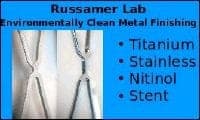
A. My company provides passivation services to a variety of customers. We have a large body of data showing that citric acid-based solutions provide surface chemistries that are at least equal, and in most instances somewhat superior, to surfaces passivated with nitric acid (as measured by elemental surface analysis using ESCA, Auger, etc.).
A paper and powerpoint presentation was recently presented at a trade conference by an engineer from one of the aerospace giants. He did a series of functional experiments to see actual corrosion resistance after treatment by citric versus nitric acids. He passivated surfaces after purposely contaminating them with tramp iron, and then subjected the passivated surfaces to corrosion tests such as the salt spray test. His data confirmed what surface analysis shows - that the citric acid -based passivation was slightly superior to the nitric acid passivation.
cleaning and passivation - Downey, California
What a great site. Thank you to all the contributors for your information. I have found it very helpful indeed.
January 10, 2008
Ground Water Treatment - Perth, Western Australia, Australia
Ed. note: Thank you for the kind words, David. The readers of this site are indeed both exceptionally knowledgeable and very generous in sharing that knowledge with us.
Q. Presently, I send my SST parts out for a full passivation using a nitric acid. I need to pull this process inside. I read about the citric acid process, and at first glance it looks it may work. My customer just requires "passivation" not to any specific spec.
Does anyone know how I could set this up in my plant?
Manufacturer - Vadnias Heights, Minnesota
May 17, 2010
A. Hi, Bob. As you can see, this subject of citric vs. nitric acid has come up before (in fact, on many threads, not just this one). We appended your inquiry here instead of starting another thread because it makes little sense to have everybody just repeat their opinions :-)
After you have decided which process to use, if you elect to go with citric acid or another proprietary, the vendors will get you started. If you want to go with nitric acid, since that is generic you would probably be best to retain a consultant to spec out the line for you. Good luck.
Regards,
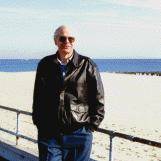
Ted Mooney, P.E.
Striving to live Aloha
(Ted can offer longterm or instant help)
finishing.com - Pine Beach, New Jersey
A. Hi,
It has been proven many times around the world that ASTM A380
and ASTM A967 are founding references on the subject of CLEANING, PICKLING & PASSIVATION.
The whole process is actually 16 stages.
Not too many people can understand this. They interpret the standards as single facts. The fact is you NEED to read both standards together to get a rough understanding.
We have Australia's (and I'm told, the southern hemisphere's) largest Nitric/HF Acid tanks at 13 meters long.
We use Nitric. There are many reasons why. Most of which cannot be published to the public. The main reason, is that Nitric/HF is brilliant for PICKLING ... NOT for passivation. We use a separate Avesta product called 630 for passivation; it isn't even an acid....that should put a few foxes amongst the pigeons.
Have a great day and may your day be filled with knowledge.
corrosion services - Perth, Western Australia
Q. Has anyone ever experienced an example where a thread has been formed in a stainless steel component and has been found to be ok prior to passivation then found to be tight after it has been passivated.
If so, can you give me information as to why this can happen when passivate does not add any coating to the surface of the material?
- UK
August 17, 2012
A. Hi Ian. Remember that stainless steel is very prone to galling. Are you sure that the thread actually grew, and it's not just the fact that oils were removed and a fresh surface, highly prone to galling, was created. What is the opposing threaded article made of?
Regards,
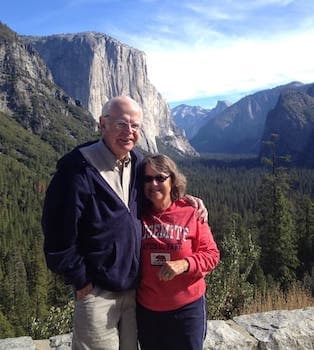
Ted Mooney, P.E. RET
Striving to live Aloha
(Ted can offer longterm or instant help)
finishing.com - Pine Beach, New Jersey
A. Simply put, in AMS2700 if the "Cognizant Design Authority" Approves the use of citric acid Per AMS2700 Method 2 as acceptable you are good to go in those steels listed as recommended in Table 4 of AMS2700. A lot of big companies won't change because someone is afraid of writing an acceptance letter from their Engineering department approving the use of AMS2700 Method 2, citric acid. The world would be a much cleaner and safer place without Nitric Acid!
David LukjanovsETI Tech Inc - Englewood, Ohio USA
March 27, 2017
Ed. note: Can we say "the world would be a cleaner and safer place with reduced use of nitric acid" instead?
Q. Hi all,
In our case, the customer wants to do citric acid passivation as per AMS2700, and 48 hours salt spray test should pass. Is this achievable in citric acid passivation? If yes or no please, describe what can be done for achieving 48 hours salt spray .
Raw material 303 or X5CrNi-18-10
Looking your feedback on this requirement.
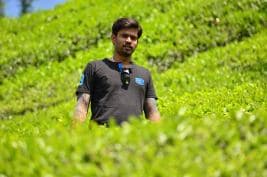
m. karthikeyan
- banagalore, Karnataka, India
January 9, 2018
Ed. note: I love this pic, Karthi! (Stream of consciousness double-take: have you read JD Salinger's classic?)
A. Either of those stainless steels will, when properly passivated, easily pass 48 hours of standard salt spray testing (ASTM B117 is what I normally think of as standard: I don't recall offhand the equivalent ISO specification).

Lee Gearhart
metallurgist - E. Aurora, New York
A. Mr. Karthikeyan,
48 hours salt spray should be trivial for that, as long as you use an alkaline (pH at least 10) preclean to rid the surface of sulfur, and the standard is followed for everything else.
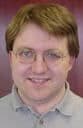
Ray Kremer
Stellar Solutions, Inc.

McHenry, Illinois
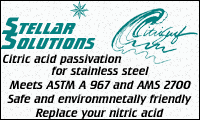
Q. Hi All,
Does Anyone know if Nitric acid bath can be "doped" with ferrous ion making it unusable?
One of my staff accidentally drop steel part in the bath, it takes over 15 minutes before we take the parts out and the bath turn some orange yellowish.
What is the impact on the 30%W/W Nitric acid solution performance.
Many thanks and best regards
- Quebec, Canada
January 23, 2018
A. Jonathan,
There is some concern about the build up of iron in the nitric passivation bath, yes. If it is saturated with iron, then for all additional iron it removes from the surface of parts, some iron will plate back out onto the surface.
As an aside, this does not happen with citric acid passivation due to the chelation that occurs.
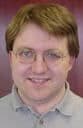
Ray Kremer
Stellar Solutions, Inc.

McHenry, Illinois
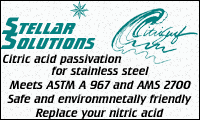
A. Hi Jonathan!
Nitric acid used in passivation of stainless steel ALREADY HAS iron in solution, so the answer is no, nitric acid with some iron in solution is OK for passivating stainless steel. You could see if there are some problem after the nitric dip (rinses) or before (pickling).
If you can't solve this issue, please tell us more about your process to help you :)
Best of luck!
TEL - N FERRARIS - Cañuelas, Buenos Aires, Argentina
Q. Dear Fellow experts/peers if you have any information/ study results for the following issue, kindly provide.
In a chemical process I am exposing the surface of stainless steel to citric acid (up to 10% and pH 4.8, Temperature: max 50 °C). There is no provision for influx of air (Oxygen).
While carrying out Electrochemical studies, the critical passivization current density is found to be a significantly high value indicating poor passivization.
Which polar organic compound (I cannot add inorganic salts as there is limitation on maximum value of conductivity) can help in passivization of stainless steel in such environment?
Freelance consultant (Materials & Corrosion : Oil and Gas, Chemical Industries) - Bangalore, Karnataka, India
January 24, 2018
A. Subrahmanya,
I think you need to consider what is actually happening during this process, and what your electrochemical test is actually measuring.
"Passivation" is a bit of a misnomer in this process. The acid bath actually is removing iron from the surface and exposing new zero valence chromium. The true passivation occurs when that chromium reacts with oxygen to form chromium oxide.
Your electrochemical measurements are probably indicating the presence of the zero valence chromium on the surface, because it is very much ready and willing to be oxidized. However, in real world conditions this would be the oxidation we want (forming chromium oxide) rather than oxidation we don't want (formation of iron oxide).
I don't know about polar organic compounds that will help you here. Short of rinsing and drying the parts then letting them sit out in the air for a while (as per correct procedure for the stainless passivation treatment) before starting your electrochemical test, the best thing you can do is soak them in a peroxide solution.
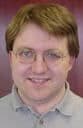
Ray Kremer
Stellar Solutions, Inc.

McHenry, Illinois
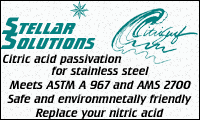
A. Just some information on Free Iron in Nitric passivation baths; some customers will have their own requirements for maximum recommended or allowed buildup in the bath. I believe GE recommends keeping it under 8 ppm, for example.
It's a good idea to perform testing on your bath as a worst-condition, pre-dump sample, and if you find how much you are building up iron under normal usage, think about scheduling bath changes to maintain total free iron at a level your customers will accept.
If you drop a tool or a bolt or something in the bath, you can always dry and weigh it against an identical object and calculate the lost weight x %iron in the alloy / bath volume to get a rough estimate of how much went into the solution and decide if you need to do an emergency dump.
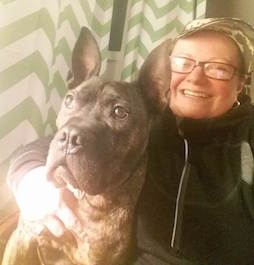
Rachel Mackintosh
lab rat - Greenfield, Vermont
Q, A, or Comment on THIS thread -or- Start a NEW Thread