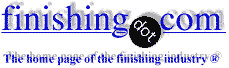
-----
Anodize Performance with NO CAUSTIC ETCH
I am a project engineer working in the military hydraulic flight controls industry. My question is as follows: To minimize localized pitting corrosion for aluminum housings that are anodized I would like to eliminate the NaOH etch process. For a part that is sent to the plating shop clean (as-machined surface from a hand forging of 7075-T73) what is the downside of eliminating the etch in terms of anodizing performance (e.g. salt spray resistance)? What if the deoxidation (e.g. HNO3 acid dip) is also eliminated that is normally performed to remove the smut for the etch process? If I just allow mild alkaline cleaning what will be the downside for anodizing performance. Comments or a response will be greatly appreciated.
Terence SavasMaterials Engineering - Irvine, California
2004
What you are describing is a "non etch" preprocessing. Uses a non caustic alkaline cleaner, phosphoric acid based etch and a iron/EDTA desmut. Works fine on fully machined wrought alloy. 7075 is not an easy alloy to work with and some anodizers have problems doing a great job. I would have a few test parts done and then use them as a performance standard, if they are acceptable. Both the shop and your QC need several pieces for references.
James Watts- Navarre, Florida
2004
James, thank you for the response. You mention "phosphoric acid based etch and iron/EDTA" can you descibe these further. Does the phosphoric acid "etch" as you say. What exactly is iron/EDTA? Are you concerned without a "deoxidation" process of some sort, i.e. strictly non-etching cleaning, that anodize or Alodine will not properly coat.
Thanks again,
- Irvine, California
2004
2004
You can go to virtually any large plating chemical vendor and find a non etch system. This does cost a bit more than raw chemicals, but after years of being cheap, it dawned on me that I was literally penny wise and pound foolish. Just the operations sheet and analsys methods is worth the minor extra cost. The ability to call tech services when you are in a bind is invaluable. Now for the chemistry. After a non caustic alkaline cleaner, it goes to a tank that is mainly water, phosphoric acid, wetting agents and proprietary "stuff". This activates the surface but will leave a small amount of smut/oxides. The next tank looks like Georgia clay mud water. This is from the iron in it. It also contains EDTA which is a powerful complexing material. The total process removes very little material, so it does nothing for hiding scratches. It works great on 2024 and 6061. Do not remember doing any 7075, but it should work. This process might not work on castings. It did great on wrought and good on decent extrusions. To show my age, we bought it from Allied Kelite which was bought out years ago.
James Watts- Navarre, Florida
Your pitting problem has nothing to do with the NaOH etch. The parts are not being properly deoxidized in the HNO3, and the use of iron containing deoxidizer will only make the matters worse as you will leave traces of iron on the parts. You need to increase the activity of your HNO3 bath.
Jonathan Flicher- Chicago, Illinois
2004
Terence
Etching these parts may not be the right thing to do. Etching removes aluminum and leaves everything else in place (mostly). Therefore your first idea of eliminating the etch is a good one. Eliminating the dioxide is not. This step not only removes the smut but it neutralizes and prepares the aluminum for anodizing. It is essential for the removal of oxide of aluminum that will cause uneven anodizing and can contribute to salt spray familiar.Remember the difference between a deox and a desmutter=a de-smutter will only de-smut a deox will de-smut and de-oxidize. Please refrain from going into the anodizing tank directly from the cleaner or its rinse. It is bad policy and can kill your anodizing tank prematurely. You can also try a cycle of cleaner-deox-cleaner deox rinse than anodize. To me the only reason for an etch is to cover visible surface imperfections.
Hope this helps!
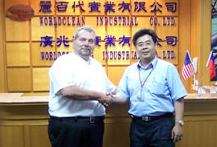
Drew Nosti, CEF
Anodize USA

Ladson, South Carolina
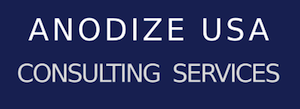
2004
Q, A, or Comment on THIS thread -or- Start a NEW Thread