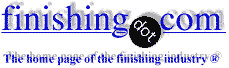
-----
Shelf roughness in nickel-chrome plating
We are manufacturing faucets and I am working at plating the parts. (Typical bright nickel / Chromium plating) We use brass diecasting as a substrate. These days we are having trouble with roughness on the shelf because required plating quality level became very critical. Insides of product are having very complex structure. So we have difficulty in precleaning process. After stripping plating layer, insides of product become clean and we get better plating. Major dirt in the product are casting sand on the corner of inside, metal chip of machinery process, and buff compound of polishing process.
Our precleaning process are as follow : Vapor degreasing -> Dipping in alkaline cleaner -> rinse (3 times) -> ultrasonic cleaning -> rinse (3 times) -> electrocleaning (cathodic, anodic) -> rinse (3 times) -> surface activation -> rinse -> Nickel plating.
Is there any solution which could solve our problem?
Thank you.
ST LimPlating shop - Gum gok dong, Incheon city, South Korea
2004
Buffed parts are generally not vapor degreased as this is known to strip away any grease from the buffing compound and leave the abrasive grit hardened on. The process might run better if you simply skip that step.
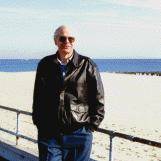
Ted Mooney, P.E.
Striving to live Aloha
(Ted can offer longterm or instant help)
finishing.com - Pine Beach, New Jersey
2004
2004
Mr S T Lim,
The Pretreatment is the key. Follow this sequence.
1) Soak Clean for 6-8 minutes in a Liquid Wax Remover cleaner which is used to remove Polishing compounds and wax. Its called" CHOO LA SHOEI" in China but I am sure you can find the equivalent from a Korean source. This step can be run in an Ultrasonic cleaner tank for added effectiveness.
2) Alternatively the second stage can be the same cleaner with Ultrasonic agitation for 5 minutes.
3) Third step can be a rinse and
4) cathodic Cleaner as per present set up.
5) Anodic Cleaner as per present set up.
6) Rinse twice
7) Continue as before.
Shelf roughness in Nickel is also caused by lack of sufficient air agitation but I am reasonably sure you have checked that by now. Dust and dirt sucked in from the blower is a factor at times. Eliminate the solvent cleaner from your sequence.
Good Luck,
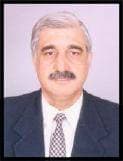
Asif Nurie [deceased]
- New Delhi, India
With deep regret we sadly advise that Asif passed away on Jan 24, 2016
Q, A, or Comment on THIS thread -or- Start a NEW Thread