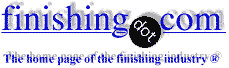
-----
Student's Nickel electroplating problem
Q. I am currently doing an investigation on Nickel electroplating in school. I am having problems, as every time I try to electroplate onto a Copper sheet I always get a layer of Nickel (II) Oxide and no Nickel metal. I have tried using different current densities and concentration of solution(Nickel Chloride). However, I have found out that when I use Ammonium Nickel Sulphate I get a nice shiny coating. Can someone please explain why this is the case?
Thank you very much,
Waseem A. [last name deleted for privacy by Editor]Chemistry investigation - Glasgow, Scotland, UK
2004
A. Interesting ... The only thing I can think of is that nickel is usually electroplated at a pH of about 3.5 to 5 (in round terms). I do not know the pH you used with nickel chloride, but I suspect it will be at least 5 and perhaps higher. This will result in the nickel oxide being put down. When you used ammonium nickel sulphate you had the solution buffered at a suitable pH (i.e., between 3.5 and 5). However, I am surprised you got a bright deposit, unless it was very thin and on to a bright brass plate.
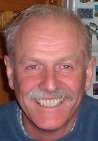
Trevor Crichton
R&D practical scientist
Chesham, Bucks, UK
2004
Q. Thank you very much for your help. Could you please suggest what I could investigate as a result. My teacher says I should try varying the concentrations of ammonia ⇦ on eBay or Amazon [affil link] and Sulphate but after reading your very generous suggestions, I feel this may be a waste of time and I do not have a lot of time to waste. I was thinking I could maybe try finding an optimum pH at which the nickel electroplating occurs. I was using copper sheets which polished before I used them and I had a very thin layer of nickel plated onto it.
Thank you very much.
Waseem A. [returning]- Glasgow, Scotland
2004
A. I would suggest a bath comprising 300 g/l nickel sulphate, 30 g/l nickel chloride, 40 g/l boric acid. Operate at pH = 3.8-4.2 at about 50 °C. Cathodic current density about 40 ASF, anodic cd about 50 ASF. This is known as a Watts nickel bath.
Add about 0.5 g/l sodium saccharin to harden and brighten it. If you want to be really clever, add about 10 g/l cobalt sulphate and this will also brighten and harden it.
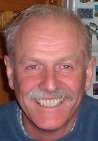
Trevor Crichton
R&D practical scientist
Chesham, Bucks, UK
2004
A. Hi,
The best method to electroplate nickel is definitely the way Mr. Trevor has suggested. It is a conventional watts bath. A few more things ... the pH of the bath has to be in the range of 4.8 to 5.4 and the current density 10 to 15 Amperes/Square feet. Also the surface cleaning and activation prior to the plating is most essential.
Mukund Shindechemical co. - Mumbai, Maharashtra, India
2004
Q. I am doing a semi-similar investigation for my advanced higher investigation, and have found that I also get the best results using a Watts Nickel Bath. My recipe for this is 52.5 g nickel (II) sulphate, 7.5 g Ammonium chloride and 7.5 g boric acid in 500 cm3 water. This works best around 35 °C and you need a nickel anode obviously.
What I am investigating is the difference produced when varying pH, temp, and current density [current per unit area of cathode immersed] this worked well for me. Good luck
- Dumfries, Scotland
September 3, 2008
Q. Dear All,
I have a chloride nickel plating bath that includes 150 gr nickel chloride and 75 ml acid Hydrochloric acid per liter.
What kind of additive can I add to my bath to get the best plating result?
Many Thanks.
- Isfahan, Iran
October 1, 2015
by William Safranek
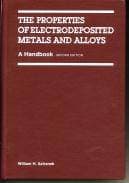
on eBay or Amazon
or AbeBooks
(affil link)
A. Hi Jalal. It kind of depends on what you mean by "the best plating result" though, since adhesion, stress, wear resistance, corrosion resistance, appearance, maximum sound plating thickness, and suitability for follow-up layers of other plating like gold or chrome may depend upon process parameters and deposition conditions. Readers may be interested in Safranek's "The Properties of Electrodeposited Metals and Alloys".
as it attempts to tabulate a lot of data on this for different deposition conditions.
Another thing that production platers, as opposed to investigators, must strive for is an equilibrium process, i.e., a process that stays the way you want it without constant need to adjust it. For example, if you try to plate from a low concentration solution, but the concentration keeps rising as you use it so that you are forced to drain off part of the solution and add water to dilute it, this will be an environmental issue as well as an expense and a possible interruption to production.
It's not clear to me whether you are a student researching nickel plating (in which case you should read Trevor's suggestions about a Watts Nickel plating bath, which will be far more successful for general plating) or you are a production shop doing a variation of Wood's Nickel Strike (which would not use any additives), or if this is some specially selected bath for an engineering purpose. Please clarify. Thanks!
Regards,
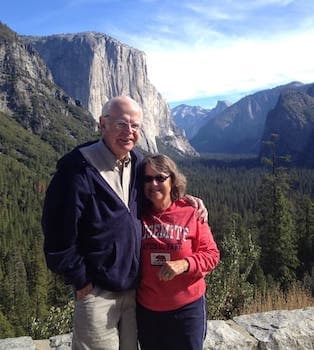
Ted Mooney, P.E. RET
Striving to live Aloha
(Ted can offer longterm or instant help)
finishing.com - Pine Beach, New Jersey
Q, A, or Comment on THIS thread -or- Start a NEW Thread