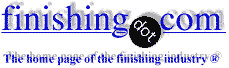
-----
Nickel-phosphorous electrolytic plating
Q. I work as Quality Engineer in a leadframe manufacturing company. Recently, we are switching an electroless nickel plating (EN plating) to electrolytic nickel phosphorous plating (by using different plating machine of course). We are plating NiP/Ni/Cu where copper is our base material. Our customer is requesting a phosphorous content in NiP layer of 6-9 wt % but when we try to plate, we could not get the wanted P content, although we are using the optimal plating condition recommended by our sole chemistry vendor. Thus, I have several questions which hope can get help from plating expert on the problems I faced.
1) Is NiP/Ni/Cu electrolytic plating process is an common plating configuration in electrolytic industry? To what I am told by my plating engineering guy, this is quite a new plating process.
2) How to determine the phosphorous content in NiP layer? We used EDX analysis to check on the P content. Is there any other alternative analysis method for p content? such as AAS
⇦ on
eBay
or
Amazon [affil link] , UV spectrophotometer or ICP?
3) What are the important parameters that need to be controlled during the electrolytic plating process? pH, current density and ...?
Thanks in advance for your valuable help.
CQE Engineer - Bayan Lepas, Penang, Malaysia
2004
Electrolytic Ni-P is not commonly used in the USA. I know of two facilities that use it for high build coatings for diamond turning for optical applications. Also, one proprietary supplier has tried to commercialize it for electronic applications like yours. Their installations I believe have primarily been in Europe.
If electrolytic Ni-P is like electroless Ni-P, if you use EDX to analyze for phosphorus, you will get a high result, because phosphorus is concentrated at the surface. UV or ICP methods give better results. The UV method is described in ISO spec 4527. The ICP method is described in ASTM spec 733.
Darell Engelhaupt of NASA in Huntsville has written several papers on this bath and its coating.
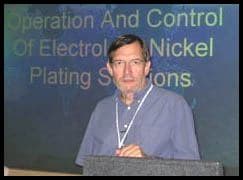
Ron Duncan [deceased]
- LaVergne, Tennessee
It is our sad duty to note Ron's passing on Dec. 15, 2006. A brief obituary opens Episode 13 of our Podcast.
A. I also know of an application in the USA in the biomedical industry which I'm not at liberty to speak too much about it, but electrolytic nickel-phosphorous has some unique properties. I mention this to note that sometimes when you think nobody is using a certain plating process, it's not as uncommon as you think.
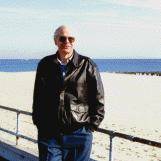
Ted Mooney, P.E.
Striving to live Aloha
(Ted can offer longterm or instant help)
finishing.com - Pine Beach, New Jersey
2004
A. I believe the copper included in the process tends to lower the P content in the deposit. try lowering the amount of copper, after you have a reliable analytical method. I have used gravimetric methods successfully.
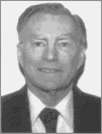
Don Baudrand
Consultant - Poulsbo, Washington
(Don is co-author of "Plating on Plastics" [on Amazon or AbeBooks affil links]
and "Plating ABS Plastics" [on Amazon or eBay or AbeBooks affil links])
2004
A. Dear Mr. Ho;
for the P% content change, one easy way is to change the ASD.
- Sinagpore
August 10, 2013
Q. Does NiP require a Au flash on the surface for corrosion resistance. I know some use PdNi without Au flash and work just as well.
TJ Tan, Engineering Manager- Singapore
September 26, 2012
Hi TJ.
Nickel phosphorous is quite corrosion resistant and is used alone in lots of applications, although gold is even more corrosion resistant, of course. I could be mistaken, but I think the usual reason for gold plating of nickel phosphorous is for low contact resistance for very low voltage, very low power, digital circuits where even a little tarnish is a problem.
Regards,
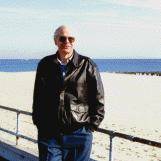
Ted Mooney, P.E.
Striving to live Aloha
(Ted can offer longterm or instant help)
finishing.com - Pine Beach, New Jersey
September 27, 2012
Ni-Co-P electrodeposition
October 11, 2017Q. Hi
I tried to make nickel-cobalt-phosphorous coating by electrodeposition but the coatings didn't have enough quality (weak adhesion and cracks high stress). Electroplating bath was 240 g/l H2SO4 + 30 g/l NiCl2 + 40 g/l CoSO4 + 30 g/l H3BO3 + 20 g/l NaH2PO2 and saccharin + SDS as additives. The condition was as following:
pH= 2
i= 5 A/dm2
T= 65 °C
agitation = 250 rpm by 4 cm magnet in 250 CC beaker [beakers on
eBay
or
Amazon [affil link] .
The thickness of coatings= 100 µm
I cannot use another bath (such as sulfamate or chloride bath). Is pulse or reverse pulse electroplating helpful? Please give me some advice. How can I have good coatings?
Student - Tehran, Iran
Q, A, or Comment on THIS thread -or- Start a NEW Thread