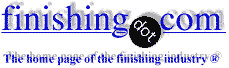
-----
Need alternative to manual buffing of stainless steel
Q. I am woking in an industry making sheet metal components for auto industries. We make all two wheeler fuel tank caps in stainless steel and our customer needs this in mirror finish. When we do buffing we get the required finish but this is tedious and non environmental.is there a better method of getting mirror finishing(buffed finish) which is easier in terms productivity and environment friendly.
Your reply will be highly appreciated. Regards,
M.RafiG.M. - Faridabad, Haryana, India
2004
A. Basically, you have 2 alternative choices. One is to use mass finishing equipment and burnish the parts or 2, electropolishing. Because I am more familiar with mechanical processes, I will only say that this will be about 90 or 95% the quality you get from a buffing operation. As for electropolishing, you surface profile will not improve that much, but you will get a reflective finish.

AF Kenton
retired business owner - Hatboro, Pennsylvania
2004
A. Try electropolishing
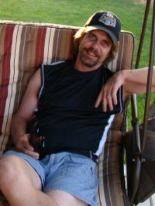
Marc Green
anodizer - Boise, Idaho
2004
A. AF is right. Mechanical polishing will remove the marks and flattening required surface. Chemical polishing is a reflective brightening process. My experience is that is you really want to get a good surface. First go for mechanical polishing, then chemical brightening to increase surfaces brightness.
Alfred Kung- Hong Kong
2004
A. I would recommend for mass finishing machines.
Niranjan S. Kulkarni- Thane, Maharashtra, India
2004
A. Mr Rafi
I will suggest:
- Vibratory Bowl polish to remove draw marks and burrs.
- Electropolish to a mirror finish.
This will replace Manual polishing and assure productivity as well.
Regards,
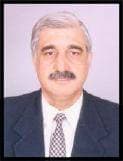
Asif Nurie [deceased]
- New Delhi, India
With deep regret we sadly advise that Asif passed away on Jan 24, 2016
2004
Automatic inline tube polisher to achieve mirror finish
November 9, 2009Q. I am a stainless steel tubing distributor. I purchased a used centerless polishing machine manufactured in someone's garage. After spending a few thousand dollars replacing a 10 HP motor, speed reducer controller and electronic motor starter I got the polisher to achieve a decent, but not great, 180 grit finish to my round tubing. Since it is a centerless polisher, I can only polish round tubing. The problem I am having is the tube ends up with a "trailing effect" or a "barber pole". As the tube goes through the machine you can see a line coming from the belt. I am wondering if the angle of the material hitting the contact wheel has something to do with this. I have tried several different angles. I have made many adjustments to make sure the material is level and going through the polisher straight. Oh and by the way, my tubing is always 20 ft long.
I use a 4" wide x 118" long abrasive belt. I recently purchased a 4" wide rubber-contact wheel on a quick-change hub. I have one 40 durometer wheel and a 50 durometer wheel. I find that when I change the belt often, these trailing lines are not as prominent. For example, 1.50" O.D. tubing, I have to change the belt after the fifth tube. The belts seem to have plenty of abrasive left. I feel that I am wasting belts. If I continue to use it the "trailing" becomes more prominent. I have used a rubber belt cleaner but it doesn't seem to help. It does seem to get rid of the dirt on the belt but it does not stop the trailing effect. I have used additional belt dressings but to no prevail.
Because of this, I spent over $10,000.00 to manufacture a new polisher with a few upgrades. I now know the machine is square and level. I know the tube is traveling perpendicular through the machine. I am still having the same issue.
Just in case you don't understand how my machine works I would like to briefly explain it. This polisher is similar to a centerless grinding machine. One side of the machine spins the round tubing with a rubber drive wheel with an adjustable speed control. As you push the drive wheel toward the tubing It pushes the material into the polishing wheel spinning at 3000 RPM. You can angle the drive wheel forward or backwards to advance the tubing through the polisher in either direction. I have the ability to use abrasive belts or various polishing wheels, sisal and airway buffs
⇦ on
eBay
or
Amazon [affil link]
.
I have used a few different types of polishing wheels. I have used a
12" x 5" x 2" wide Aluminum Oxide, medium grit (soft and hard). They have also yielded the same results. The belts achieve a better finish, though.
Please help. I am tired of throwing money at bad ideas.
President of Stainless Steel Distributor - Ontario, California, USA
A. For some reason while looking for hints on achieving a superfinish on aluminum parts I came across your question. I am a centerless grinder of some merit and would like to help you out. I moved to California from Michigan around 3 years ago as aerospace work is somehow more abundant than automotive work these days. Try these tips to eliminate your barber pole...
When using the polishing wheel: since I am assuming you have no dressing attachment on your machine, you should use a dressing tool such as a cluster diamond or even a silicon carbide stone to manually dress a VERY gradual taper or crown on the exit side of the wheel. By gradual I mean I would attempt to relieve the last inch to inch and a half of the wheel in the following manner... .001 over the first 3/4" and a fairly aggressive crown after that(up to .030")
When using the belts: You could try altering the supports to achieve the same effect as above, if you have a guide for the belt to hold it against the form on the supports.
Hope I am of some help.
Howard Stuckey- Rancho Cucamonga, California
February 17, 2010
Q, A, or Comment on THIS thread -or- Start a NEW Thread