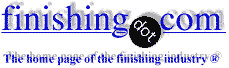
-----
Salt spray test parameters
Q. We are in a process of buying a salt spray tester. Before that I would like to know the parameters to be recorded during ACTUAL testing. Is there any format for recording chemical concentration? If we use distilled water for solution is there any need to adjust the pH of the concentration.
How the results are normally evaluated? I mean how the report is made? Do we need to mention % of corrosion observed with regular intervals by checking the component? Or only end result is recorded after the test is over?
Q.A.Engineer - Aurangadab, Maharashtra, India
2004
A. astmb633.htmlb117.html" --> should have all of the information you need with regards to maintaining the salt fog conditions. When evaluating the results of corrosion tests, there are a number of standards to use. The following is a partial list:
ASTM D610 Standard Test Method for Evaluating Degree of Rusting on Painted Steel Surfaces
ASTM D714 Standard Test Method for Evaluating Degree of Blistering of Paints
ISO 4628-1PAINTS AND VARNISHES - EVALUATION OF DEGRADATION OF COATINGS - DESIGNATION OF QUANTITY AND SIZE OF DEFECTS, AND OF INTENSITY OF UNIFORM CHANGES IN APPEARANCE - PART 1: GENERAL INTRODUCTION AND DESIGNATION SYSTEM
ISO 4628-2PART 2: ASSESSMENT OF DEGREE OF BLISTERING
ISO 4628-3PART 3: ASSESSMENT OF DEGREE OF RUSTING
ISO 4628-4PART 4: ASSESSMENT OF DEGREE OF CRACKING
ISO 4628-5PART 5: ASSESSMENT OF DEGREE OF FLAKING
ISO 4628-6PART 6: RATING OF DEGREE OF CHALKING BY TAPE METHOD
ISO 4628-7PART 7: ASSESSMENT OF DEGREE OF CHALKING BY VELVET METHOD
ISO 4628-10PART 10: ASSESSMENT OF DEGREE OF FILIFORM CORROSION
Automotive module supplier - Michigan
A. ASTM B117 includes a section on records and reports. That information applies to the test conditions only. The test requires water which meets ASTM D1193 Type IV. Using this water will not guarantee the correct pH since that is very much dependent upon the proper mixture of salt and water, as well as the salt itself. Checking the pH of the collected solution is required by B117. The results and evaluations of the samples are usually outlined in the material specification. For example, an automotive company may indicate that 5% red rust is allowable, while another may require less than 5%. Usually results are recorded at the end of the test, but that can vary with the material specification.
As Toby already indicated, there are a number of standards which describe a rating scale.
- Sylvania, Ohio, USA
2004
Q. Thanks for your reply. But I would like to know if we use distilled water for salt concentration, do we need to check & adjust the pH during salt spray testing? What is the normal requirement, how many hours of salt spray should withstand for a zinc phosphated shaft?
Prasanna- Aurangabad, Maharashtra, India
2004
A. You absolutely have to check both the makeup tank and the collected spray. They will not be the same pH as the collected solution will take up some carbon dioxide from the air and change the collected pH. The tank pH has to be maintained at a pH that will allow for the correct "collected" sample pH. A final note, don't look for an easy way out. If you take that approach, you are not in compliance with the specification and thus can not certify to it!
James Watts- Navarre, Florida
2004
A. B117 requires that you check the pH of the collected solution. Since it usually changes during atomization, the only way you will know the pH at which to start your make-up solution is to check that, too. Using distilled or deionized water doesn't guarantee that the pH will be correct.
Cynthia L. Meade- Sylvania, Ohio, USA
2004
Q. We would like to know the standards IEC-68-2-11 supply conditions, etc.
chidambar nadigerbuyer - jamnagar Gujrat India
August 2, 2008
A. Hi, Chidambar. I believe that spec is also known as
IEC 60068-2-11 Ka. We've linked to a place you can get it. Good luck.
Regards,
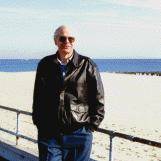
Ted Mooney, P.E.
Striving to live Aloha
(Ted can offer longterm or instant help)
finishing.com - Pine Beach, New Jersey
August 5, 2008
Q. We are currently doing 40 hr salt spray test on our zinc chromate plated parts. Can't find a standard of the permissible red rust. Most of the standards are for setting up the chamber such as ASTM B117.
Any suggestion? We were suggested to use no more than 5% surface are.
Quality Engineer - MIRAMAR, Florida, USA
July 15, 2013
A. MIL-STD-1312-1, "Fastener Test Methods. Method 1, Salt Spray"
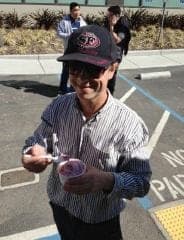
Blake Kneedler
Feather Hollow Eng. - Stockton, California
First of three simultaneous responses -- July 16, 2013
A. Hi Steven,
I would hope that after 40 hours you wouldn't see any red rust, it would indicate either an inadequate thickness of zinc or poor quality plating!
At the end of the day you have to make the call about what is acceptable to you. Your acceptance standard will depend on how and where you are using the coating.
In aerospace we tend to want a much higher standard of corrosion resistance than say the automotive industry, so where automotive may look for 48 hours resistance to red rust aerospace would be looking for 96 hours to white and probably 168 hours to red rust.
Aerospace - Yeovil, Somerset, UK
Second of three simultaneous responses -- July 17, 2013
A. Hello Steven,
If you see the posts above, you will see one written by Toby Padfield. He listed some of the standards to assess corrosion test results. 5% maximum corrosion is not a bad criterion, you should talk with your client to clarify how much is OK or not OK.
Hope this helps you! Good luck!
- Cañuelas, Buenos Aires, Argentina
Third of three simultaneous responses -- July 17, 2013
Q, A, or Comment on THIS thread -or- Start a NEW Thread