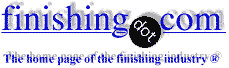
-----
Rusting of stainless turnstiles
Q. We have recently installed 8 full height security turnstiles at our industrial automotive facility. Each unit has (47) 304 stainless steel arms measuring about 1-3/8" diameter by 24" long and have a brushed finish. The units are located under a canopy outdoors in the Michigan weather. They are getting some salt mist in the winter. The units started badly rusting within two weeks. The manufacturer has given me several options. Swap them for 316SS at about $4 per arm plus labor. Or for a bigger charge, swap them for electro polished 304SS. Any suggestions, for cleaning/treating my existing arms on-site with polishes, etc. Or any comments on probable success and rust resistance of the 316 vs electro polished 304.
Are there companies that can do the electro polish locally in the Detroit area?
senior facility engineer - Detroit, Michigan
2004
A. Hi, David. It's reasonable to ask whether type 316 or electropolished 304 will be better. But you've purchased this turnstile from a manufacturer for semi-sheltered outdoor use, they've already let them off the hook once for giving you the wrong stuff. So I think they should be telling you what material is right for the installation conditions instead of you telling them, letting off the hook for a second time :-(
Our readers tend to favor 316 if there is going to be any salt about. Any stainless that is not electropolished, however, should be passivated. Yes, there are a number of companies who offer on-site electropolishing and passivation services, and hopefully you will see one advertising that service at the top of this page.
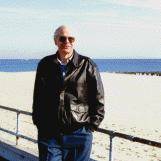
Ted Mooney, P.E.
Striving to live Aloha
(Ted can offer longterm or instant help)
finishing.com - Pine Beach, New Jersey
2003
A. I have some decorative outdoor stainless that was electropolished three years ago and still shows no sign of rusting. We are in North Georgia where there is NO salt, but they are exposed totally to the elements and still look like the day they were installed. You should get your contractor to get these parts properly passivated. It is obvious that they were not passivated if they failed in two weeks. I would even suspect they were put in contact with carbon steel in the final finish to fail as fast as they did. It is not uncommon for architects and contractors NOT to know about passivation of stainless architectural elements.
Dan Weaver- Toccoa, Georgia
2004
A. Ted is correct, of course. The supplier should have originally recommended the grade that works in this environment. If it is exposed to large amounts of salt spray you need 316. Even electropolished 304 will not hold up.
Were the parts passivated originally? If not, and if there is not a large amount of salt involved, you may be able to clean them up and passivate them properly so that they can last a reasonable time with maintenance. It may be worth trying a modified citric based material in situ that will remove the rust and repassivate the surface. If that does not hold up you can always replace them with 316SS.
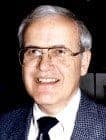

Lee Kremer
Stellar Solutions, Inc.

McHenry, Illinois
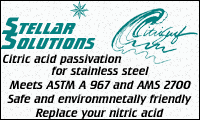
2004
A. Having dealt with this problem innumerable times in the past (before retirement) I can tell you that the above responses are correct; and improper or no cleaning/passivation was done by the fabricator, or, it was done and the units sat around in the fabrication shop environment too long after passivation and became recontaminated. Another possibility is that your local environment has iron contamination in the air. That is something that could be checked with a relatively simple test panel exposure program. Your immediate solution is, as previously mentioned, to re-clean and re-passivate. How long that lasts could, in effect, be your test panel program. It does not, however, solve the supplier liability problem. You really need objective evidence that it is not your local environment causing the problem.
Ray B Anderson- Kent, Ohio
2004
A. Not only is it common for fabricators to be unfamiliar with passivation, many will use steel fasteners. Check that there is no steel around your stainless. You might check if there is any one around who can passivate the pieces in situ.
Steve Clarkplating/polishing - Belfast, Maine
2004
A. About your 304 turnstiles. The city of Port Huron used an Electro Polished Railing along a riverfront walkway. It has held up for several years, and I would imagine that depending on the dimensions as long as the parts are uniformly polished, and they aren't damaged upon assembly you shouldn't see any corrosion.
As far as 316, I suppose it would work, but if you already have everything made of 304 you can still get it polished.
As far as the walkway in Port Huron, a friend of mine assembled it, and he said that it was all polished locally.
- Toronto, Ontario, Canada
2004
Q. A supplier sent in some parts that were 304 SS instead of 316. I am wondering if sending them out to be electropolished could make the performance equal to 316. The part has to be crimped so there will be some surface damage to the part after the process. Is this worthwhile or should the parts just be returned?
Les Subratteedesigner - Fort Lauderdale, Florida
February 16, 2009
A. Hi, Les. Electropolishing will remove iron from the surface of the stainless steel and make it less susceptible to rusting, but 304 is still 304, it's not 316. As Lee Kremer notes, if salt spray is present, 304 probably will not hold up.
Regards,
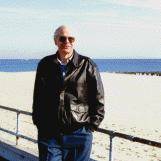
Ted Mooney, P.E.
Striving to live Aloha
(Ted can offer longterm or instant help)
finishing.com - Pine Beach, New Jersey
February 16, 2009
! Thank you all for your inputs on the subject. I suspected that 304 EP would would only temporarily mitigate and not perform up to 316. Looks like I will have to still run some test in salt fog to compare 316 vs 304 EP to appease the masses hellbent on shipping product.
Les Subrattee- Fort Lauderdale, Florida, USA
February 17, 2009
Q. I wanted to know the advantages of SS 316 over SS 304 bodies. We manufacture barriers and gates required for pedestrian and vehicle access.
Sam Pothapragada- Miami, Florida
January 28, 2012
Hi, Sam.
We appended your inquiry to a thread which hopefully will partially answer it. Type 316 stainless steel is more resistant to salt than type 304, and just generally somewhat more corrosion resistant. But in either case the stainless steel must be passivated. This is the process of treating it with nitric acid or citric acid to remove any traces of regular steel that it may have been contaminated with during manufacturing. Electropolishing is a more expensive process which not only passivates, but smooths the surface.
Regards,
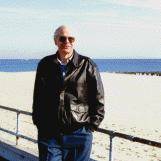
Ted Mooney, P.E.
Striving to live Aloha
(Ted can offer longterm or instant help)
finishing.com - Pine Beach, New Jersey
January , 2012
Q, A, or Comment on THIS thread -or- Start a NEW Thread