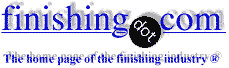
-----
Gold plating thickness on high abrasion parts
I need to know what would be the specification, ASTM, MIL, etc., and most desirable thickness and of gold plating on two pieces of metal that slide, under pressure, against each other at least twice a day. One piece is a brass rivet and the other is a beryllium copper spring. A nickel underplate would be applied before the gold plating.
Dick SpearManager, Manufacturing Engineering - Boulder, Colorado, USA
2004
A. Someone just said in another thread that 15 millionths of an inch is a typical thickness of gold on a PCB edge connector, so I certainly don't think it should be less than that.
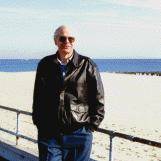
Ted Mooney, P.E.
Striving to live Aloha
(Ted can offer longterm or instant help)
finishing.com - Pine Beach, New Jersey
A. The plating specifications are MIL-G-45204C GOLD PLATING, ELECTRODEPOSITED (canceled, but still available: http://assist1.daps.dla.mil/quicksearch/), AMS2422 E Plating, Gold (www.sae.org), and ASTM B488 Electrodeposited Coatings of Gold for Engineering Uses (www.astm.org).
For abrasion resistance, select a 99.0% gold, alloyed with Co or Ni to give a Knoop Hardness > 200. This is Type III, Grade D per MIL-G-45204C or Type 3, Code D per ASTM B488. Sorry, don't have the AMS spec.
- Goleta, California

Rest in peace, Ken. Thank you for your hard work which the finishing world, and we at finishing.com, continue to benefit from.
A. Surface finish, gram force and expected life (cycles) are critical factors in determining the amount of hard gold or gold substitute to be used when engineering a contact finish.
Rick McCarthy- Chicago, Illinois, USA
Q, A, or Comment on THIS thread -or- Start a NEW Thread