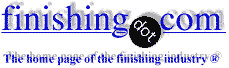
-----
Hard Times In Hard Chrome Plating
The following problem has just surfaced on a cylindrical item, utilizing hard chrome plate on an internal surface: Lower coating thickness than expected,with differences of thickness on the circumference section and void areas the length of the component about 15 degrees.
We found that one phase was missing(2 fuses 3000a and 2 scr were replaced, routine troubleshooting).The coating was still low and not same thickness all around but the void area disappeared.The manufacturer of the rectifier delivered the unit with an AC ripple of less than 5% (between 1 and 9 V), but we have now measured about 16%. Samples were sent to the lab of the solution and proved to be satisfactory. All electrical conductors have been tested and cleaned. We also tried to plate using (4) each other type of setups, no luck. We have interchanged the electrical boards from another power supply,12kA@15V. We replaced the solution with new material.
The situation now is that we can only get 3.9V, no higher. Even when the current can be raised to 12000A, the voltage only raises to 4.7V. The coating is very poor and non homogeneous, thickness around and along the component, More pronounced near the electrical connection and very low the further away your connection is.
The power supply was tested in the following manner. The unit was analyzed with an oscilloscope and all phases are present. Without a load the voltage can be raised up to max.(9V), and the current only goes to 200A. There has been a plating cycle on a shorter component,plating externally, and all parameters were controllable (including voltage and current. The coating appeared very good. We have loaded the power unit supply using stainless steel bars and have raised the current up to 7000A, and the voltage up to 7.5V. Also the unit had been loaded with regular steel bars and the current went up to 15000A and the voltage up to 2.5V.The process was verified for voltage at both ends of the component.Noticed that at the upper end closest to the connection the power supply indicated 3.9V DC, 0.8v ac, and at the opposite end the voltage was 2.5V DC 0.005V AC.
Charles H.CollinsProduction Manager - Watervliet, New York, USA
2004
Are you using an internal anode? No matter how much current/voltage you put into the job, if it needs internal plating, you must use an internal anode. In fact due to the proximity of the internal anode to the surface to be plated, you will find much higher deposition rates than normal external anode plating. Reduce the current density by about 1/3 for this application. The agitation of the solution is not a problem, because the plating reaction will provide more than enough agitation allowing constant exposure to fresh solution. I think you are on the wrong track electrically testing all your equipment - we found greater than 20% ripple in one of our rectifiers once, through routine maintenance. The jobs were still coming out with no discernible difference in deposit quality!
The tests you performed on externally plated test pieces that came out ok seems to indicate this may be your problem.
Trevor RowlandsAircraft Component Manufacturer - Melbourne, Victoria, Australia
2004
There is an internal conforming anode being used in the process. However, could there be an oxide layer or coating on the anode over a period of many cycles, preventing from, processing the right current density. If so, please advise as to removing this (skin), if in fact this could be the problem.
Charles H.Collins- Watervliet, New York
2004
You might check the current going to the part(s) using an induction ammeter. This will tell you if there is something interfering with current going to the internal anodes. One other thing to look at is the condition of the external and internal anodes; see if there is a difference in appearance.
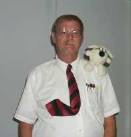
James Totter, CEF
- Tallahassee, Florida
2004
Charles,
If I understand this correctly, you have made up a new solution, and assume that you are measuring the voltage at the vat. The reason for the lower voltage is the electrical resistance of the new solution is lower than that of the old solution, which effectively gives a higher internal resistance to the power supply and hence a larger internal volt drop...Well that makes sense to me... and probably has nothing to do with your problem. I've seen rectifiers with 2 phases missing and they still plate ok.
From your description it sounds like an anode problem. Internal anodes are always a problem, so check them out carefully, I assume you are using lead, they should have a brown film if they are working properly. Even if they don't have a film when you put them in the vat, they soon form one when you start plating. Make sure there is a good electrical contact. Its difficult to get a good permanent contact to lead, so they need cleaning regularly, if they are not good they won't pass the current, so you won't get the expected thickness.
Also check for insulation between the anode and the jig. you could be loosing a lot of current in this area. I once made a fixture that worked well until the vat was topped up, and solution went over the top of the fixture, which wasn't insulated, the fixture plated brilliantly, but the bore was completely bald.
Chrome plating is dead easy, until it doesn't work, like most of my customers say; "don't you just dip it in".
Hope this helps,
Steve Kelsonhard chrome plating - Cheshire, England
2004
Check your plating bath for contamination from trivalent chromium, iron, copper, nickel . If there is more than 1 oz. per gallon of the combined it can cause problems. Running a high cathode to anode ratio can cause trivalent chromium problems. Also check your sulphate to chrome ratio.
Todd Osmolski- Charlotte, North Carolina, USA
2004
Charles,
In a inside " internal" chromium plating will the current get down if you not pump the chrome solution and exchange the solution. Because the high trivalent chromium building.
Regards,
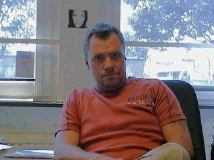
Anders Sundman
4th Generation Surface Engineering
Consultant - Arvika,
Sweden
2004
Q, A, or Comment on THIS thread -or- Start a NEW Thread