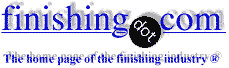
-----
FeCl lack of depth-of-etch on brass plates
2004
Hi all,
S-C-O-T-L-A-N-D calling here!
I've been in the engraving industry for 14 years now and have been experimenting on newer ways of marking brass plates.
I've been using a pcb-etching method (FeCl fluid etchant) which works fine,but lack-of-depth of etching seems to be a problem.
Great if anyone can help.
Regards,
Darren
Metal/plastic engraver venturing into additional methods of marking brass & steel. - Glasgow, Strathclyde, Scotland
Chemical etching with ferric chloride ⇦ on eBay or Amazon [affil link] is a messy job and not for the faint of heart. Unfortunately you do not say how much experience you have with the technology (some would say "art", but I prefer the precision of the sciences!). Etching brass requires a solution of 2-3M ferric chloride ⇦ on eBay or Amazon [affil link] (equivalent to 30-42Be) and an operating temperature of no more than 45C. To prevent the whole surface being dissolved, you need to generate a mask on the surface of the brass. The width of the exposed metal lines will influence the depth to which the etch will go; this is called the "etch factor" or aspect ratio. As a guide, the narrower the line width, the deeper (relatively) the etch will go. This is because the etching process takes place both into the metal and along the underside of the mask. The etch factor can be increased (i.e., get a deeper etch) by jetting the ferric chloride ⇦ on eBay or Amazon [affil link] directly at the metal face, thereby focusing the attack in the direction of the jet and hopefully minimising any dissolution on the sides of the etching hole. This single suggestion, unfortunately, is not going to provide you with a good deep etch. Etching rates can also be enhanced by using a slightly more dilute solution, but this jeopardises the lifetime of the solution. The trick to getting as deeper etch as possible is to minimise the thickness of the Helmholz layer and this is simplest done by having a high velocity jet at the metal/etchant interface. Depending how deep you want to etch, you may have to consider mechanical methods prior to chemical etching.
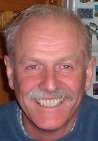
Trevor Crichton
R&D practical scientist
Chesham, Bucks, UK
2004
Q, A, or Comment on THIS thread -or- Start a NEW Thread