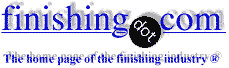
-----
Risk of not phosphating?
Hello,
I will like to know if you can help me about the following question: I work with powder coating, but want to know what are the risks of not using the phosphate in the pretreatment process for metal parts? Thank you very much for helping me.
Eliseo IzquierdoQA Eng. - Juarez, Chihuahua, Mexico
2004
Hi Eliseo. 'Work with' is a little vague -- I'm not sure if you are implying that you are the designer/specifier or the applicator. Without knowing the application and the exposure environment, and the type of powder coating, I really can't tell you whether it NEEDS phosphate or not. But phosphatizing is always a very good idea and should not be omitted unless the item is too difficult to phosphate, and will see only interior exposure, and is otherwise well prepared.
You might want to consult R. Rausch's book "Phosphating of Metals" ⇦[this on Amazon or AbeBooks affil links] or Samuel Spring's Preparation of Metal for Painting ⇦[this on Amazon affil links] for a full list of the many ways in which phosphatizing benefits the parts, but a starter list is: providing good key for paint adhesion, providing undercutting protection, and minimizing galvanic hotspots. Good luck.
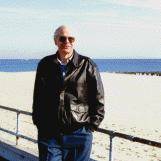
Ted Mooney, P.E.
Striving to live Aloha
(Ted can offer longterm or instant help)
finishing.com - Pine Beach, New Jersey
2004
![]() |
2004 Hi Ted , Hope you can read between the lines & take this in a good spirit, ![]() Atul Bhide jobshop / applicator - Mumbai, India 2004 I appreciate you taking the time to point out your reading of my response, Atul. If Mr. Izquierdo was offended, I heartily apologize! My only point was that I did not understand his situation. We edit typographical, spelling, and grammar errors, etc., so that our readers can read & understand the questions quickly, and so the questions are indexed properly in search engines. We very heavily edited Mr. Izquierdo's inquiry, so what you see here is very different than what he wrote; I was hoping that I did not misunderstand it or change its meaning, and was requesting clarification. I have rewritten my response to him and hope you find it less problematic. I greatly admire people who are multilingual to any degree at all! Anyone's English is far better than my knowledge of any other language :-) ![]() Ted Mooney, P.E. Striving to live Aloha (Ted can offer longterm or instant help) finishing.com - Pine Beach, New Jersey |
2004
Dear Sir,
The general rule of thumb would be as follows to phosphate or not. For powder coated items that are to be sited outside (exterior) you will use a polyester powder. Having paid a little extra (poly vs e/p) it is wise to zinc phosphate. This is a preventative action in case the item gets damage (scratched) the phosphate will then prevent in the short term corrosion (rust creep) between the metal and powder.
For epoxy polyester powder coated items destined for internal use, iron phosphate is sufficient. We class it as a very good surface cleaner -- it will/may improve the adhesion of the epoxy polyester powder (?). Most coaters would only use this treatment if it is specified by the customer - why add to your processing costs?
Hope this answers the question you posted.
Terry HicklingBirmingham, United Kingdom
Can you please clarify the necessity of phosphating before electrocoating of paint in terms of Surface Activation-Phosphating-Electrocoat of Paint.
bhagwat mishrapaint shop employee - amdabad,gujarat , India
July 18, 2009
Sir,
Can you please clarify which of two -- zinc phosphating and iron phosphating -- is preferable for car bodies, and how?
paint shop employee - amdabad,gujarat , India
July 24, 2009
July 24, 2009
Hi, Bhagwat. Zinc phosphating gives a heavier and thus more expensive coating. It also involves more steps. So the short answer is that it's preferable if cost is omitted. You work in the paint shop of one of the world's largest automobile manufacturers, which probably has acquired a lot of data. So, please educate us by telling us which phosphatizing process you presently use, and why you think it is best, or why you wish to consider switching. Thanks!
Regards,
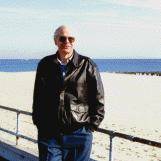
Ted Mooney, P.E.
Striving to live Aloha
(Ted can offer longterm or instant help)
finishing.com - Pine Beach, New Jersey
Q, A, or Comment on THIS thread -or- Start a NEW Thread