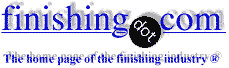
-----
Painting HDG steel for use in salt water
Q. I have had a new mild steel rudder fabricated and flux core welded for my 40' sailboat. The spine of the weldment is a 3" dia. steel pipe with plate welded to it. I have had a local galvanizer in Houston HDG it for me.
The rudder will be used in saltwater with the lower 2/3 submerged at all times. My question is one of finishing. I want to paint the finished rudder asap and am wondering what priming process will be required since the HDG will be fresh. The paint will be a high gloss two part polyurethane. I have no experience using HDG steel since the rest of my boat is of fiberglass covered wood construction. Will I need Zincs for sacrificial purposes? Thanks for your help.
Michael J. Howsleyamateur boat builder - DeRidder, Louisiana
2004
![]() |
A. There are primers for galvanize [Galvanize Primer ⇦ on eBay or Amazon [affil link] [affil link]]. In the dark ages, it contained a lot of zinc chromate which is hard to come by now. Check with several paint stores.You might find some information at major paint manufactures web sites. Sacrificial zinc is normal isn't it? James Watts- Navarre, Florida 2004 A. Michael, l. I sure like your use of a 2 component Urethane. Very high surface finish. Expensive. Very abrasion resistant. 2. Re sacrificial anodes ... not necessary IF, IF, IF the entire surface were painted. I'd be worried/concerned about the spindle holders (I don't know what the right nautical term is) through which the shaft protrudes ... (gudgeon pin?) and would strongly recommend some type of non-metallic sleeve or O-ring set-up to prevent the metal from galling. And painting the fresh surface? I wouldn't worry too much. The Urethane is a fairly flexible paint and should anyhow 'shrink around' any parts as it probably has a l0% shrinkage factor upon curing. ![]() Freeman Newton [deceased] (It is our sad duty to advise that Freeman passed away April 21, 2012. R.I.P. old friend). 2004 |
Q. We will be building a couple of 24' x 6' x 2' pontoons out of 10 gage steel for use in salt water. We are investigating various coating methods including hot dip galvanizing.
Right now we are leaning toward HDG with a zinc phosphate primer
⇦ on
eBay
or
Amazon [affil link] , then an epoxy top coat such as Devoe 235 Bar-Rust.
The immersed surface will need some sort of anti fouling paint. Appearance is not important. But coating longevity is.
Can anyone offer advice on the which coating method would be the most corrosion resistant and abuse tolerant?
Boat builder - Anacortes, Washington, USA
March 30, 2012
Q. I am considering thermal spray as an alternative to HDG on pontoons made of 10 gauge steel due to the possibility of the HDG process temperature distorting the steel.
Surprisingly, when I contacted what seems to be the only thermal spray operation in my area they said that the sandblast cleaning might also distort the 10 gage steel pontoon skins. This is difficult to imagine.
How likely is distortion caused by sandblasting? Should I look elsewhere for thermal spray services? Or switch to another coating option?
- Anacortes, Washington, USA
April 9, 2012
A. Hi, Chris.
Regarding your first posting, I believe the operative answer is "zinc is zinc". By this I mean that each application technology claims they are best, but the lifetime will still more or less be directly proportional to the zinc thickness.
Regarding your second posting, I agree that it sounds unlikely that sandblasting would cause 10-gauge material to distort. Has the shop in question reviewed the item or the drawings and perhaps have more insight than me?
Regards,
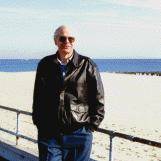
Ted Mooney, P.E.
Striving to live Aloha
(Ted can offer longterm or instant help)
finishing.com - Pine Beach, New Jersey
April 10, 2012
A. Abrasive blast "can" distort thicker material than 10 Ga.
A shop that I worked in had this problem which was aggravated by a rather thick flame spray application.
My solution for them was to blast the desired side the required amount and then turn it over and blast that side as required to obtain the desired flatness.
The reason is that removing an outer layer of metal removes a stressed layer and it will bow away from that side.
- Navarre, Florida
April 10, 2012
Q, A, or Comment on THIS thread -or- Start a NEW Thread