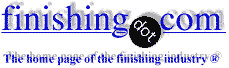
-----
Soldering nickel titanium wire?
Can anyone offer an easy solution for joining nickel-titanium "muscle" wires to copper wire. Are conductive epoxies an option.
Frank MagnarelliMiami Children's Hospital - Miami, Florida
1999
If you're talking about Nitinol wire I know that they are very difficult to solder to because of the TiO2 that is formed on the surface. We have done some PVD work in the past that has applied a layer of stainless steel onto nitinol so it could be soldered to. Before this work a gold or gold/tin (I can't remember) layer was put down electrochemically. If you're interested in the stainless steel coating on nitinol wires I'd be glad to work with you on it.
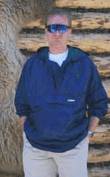
John Davis
- Berthoud, Colorado, USA
1999
2001
Title: Stainless steel & Nitinol & the oxide film relating to welding.
Objective: Recognize and be aware of the importance of the oxide layer in welding.
Stainless steel is a family of alloys made up of iron (Fe) and chromium (Cr). All steels contain mostly iron but must contain at least 11.5% chromium to be a stainless steel. When chromium is added to the iron, a thin, silvery, tightly adherent film of chromium-oxide forms spontaneously on the surface exposed to the atmosphere. This oxide layer is extremely stable and tough. The oxide layer is self-healing in that a new oxide layer will form if the metal is scratched or damaged. It is this corrosion resistant oxide film that make stainless attractive to the medical device designers. These iron-chrome alloys are known as the 400 series. The addition of nickel (Ni) to the iron-chrome alloy results in the 300 series stainless. The 300 series alloys contain different amounts of carbon to control hardness. In the process of welding the carbon combines with the chromium and forms chromium carbides. The process is called °ßcarbide precipitation°® This means that there is little or zero chromium left to form the protective chromium oxide layer.
Nitinol is believed to act the same as stainless. When the titanium oxide is removed from the surface of Nitinol, titanium precipitates to the surface and forms a corrosion resistant oxide film. It is this film that causes problems with the welding of Nitinol.
To minimize the formation of chromium carbides in stainless; a carbon level of .03% or less has been developed. These are known as the °ßL°® or low carbon types, like 304L and 316L. Also, the stainless called °ßVM°® (vacuum remelt) witch minimizes the contaminants or inclusions in the alloy, such as oxides and sulfides. These are known as 304VM and 316LVM.
When welding Nitinol to stainless, it must be a low carbon stainless. The titanium oxide on the Nitinol must be removed. Once the titanium oxide is removed, the surface re-oxides. (Healing) The Nitinol surface oxide needs to be reduced just prior to welding or soldering with an aggressive flux or other means.
INCONEL: A Huntigton Alloys nickel based material with a high chrome content. The material is strong and heat and corrosion resistant.
HASTELLOY: A Haynes International nickel based alloy with molybdenum and chromium. It is known for its high strength, high temperature and corrosion resistance. Good to 2200ÑaF.
NITINOL: A nickel-titanium alloy discovered by the Naval Ordnance Labs. Generally 55% nickel with balance being titanium. It is a shape memory alloy exhibiting superelastic properties.
ELGILOY: Manufactured by the Elgiloy Limited Partnership Company. It is a cobalt-chromium-nickel alloy having high strength, excellent flexibility, (fatigue) and corrosion resistance.
CONICHROME: Made by Carpenter Technology and is the same as Elgiloy.
MP35N: Made by Standard Pressed Steel. It is a Multi-Phase, 35% Nickel alloy. It is 35% nickel, 35% cobalt and 20% chromium with ultra high strength and corrosion resistance.
MONEL: Monel is 65% nickel, 32% copper and 2% iron. The alloy 400 has good weldability and corrosion resistance to 850 ÑaF. It resists hydrofluoric and hydrochloric acids.
Greg Townsend- Minneapolis, Minnesota
Laser weld it with an inert gas(argon'co2?)wash.
Bob Goldsmith- Mpls, Minnesota
2001
Nitinol to copper will be difficult. Use a short length of stainless steel tubing and crimp the two together, then fill the tube with solder. It will be the best bond you can get.
Greg Townsend- Plymouth, Minnesota
2002
We've been working with many Nickel Titanium Wire applications in which people want to solder or weld this wire to a substrate. Many people are having huge successes in placing a barrel crimp or splice on the wire, thus providing an area that they can weld/ solder to. Sizes of splices we've worked with are as large as .330"x.100"x.320" to as small as .012"x.012"x.017" on .0015" diameter wire.
Dave Trail- San Diego, California, USA
2002
2003
Frank:
The best way of soldering this wire to copper is to use Kester # 817 flux and sorder-it silver solder.
Lance Henriques- Tamarac, Florida
Q, A, or Comment on THIS thread -or- Start a NEW Thread