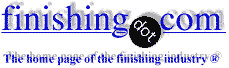
-----
BLACK ANODIZE COLOR PROBLEM
Q. WE HAVE A REQUIREMENT TO PERFORM BLACK ANODIZING PER MIL-A-8625 / MIL-PRF-8625 [⇦ this spec on DLA]E TYPE II CLASS II. THE PARTS ARE CASTINGS AND OUR CUSTOMER TELLS US THAT THE MATERIAL IS 10139101. THE PROBLEM THAT WE HAVE IS THAT WE'RE GETTING A GREY OFF COLOR AND SLIGHT SMUTTING AND OUR CUSTOMER IS DEMANDING BLACK. WE HAVE TRIED SEVERAL DIFFERENT PROCESSES AND STILL GET GREY PARTS.
THE PROCESS THAT HAS GIVEN THE BEST RESULTS IS AS FOLLOWS: 1. SOAK CLEAN 5-20 MINUTES 2. RINSE 3. DESMUT 4. ANODIZE FOR 55 MINUTES @ 69 DEGREES F 5. RINSE 6. BLACK DYE FOR 20-40 MINUTES. 7. RINSE 8. HOT WATER SEAL. OUR ANODIZE IS RUN @ 200 G/L. WE ARE IN JEOPARDY OF LOSING THIS ACCOUNT. IF ANYONE CAN HELP, WE WOULD GREATLY APPRECIATE IT. THANX, JEFF
Jeff Millsmetal finishing shop - Gorham, Maine
1999
A. Jeff, we have had similar problems with A-356 castings. The program that wants the Black Dye insist on the casting coming out black. The problem with castings is the porosity and the silicon content. First I would recommend improving the surface characteristics of the part by glass bead blasting or vibratory deburr, then use a nitric/hydrofluoric mixture as your desmut. If you prefer not to use that as your desmut you can take a brush and hand clean the remaining silicon/smut off the parts.
Best I can do to help,
Dave
David Yarberry- Dallas, Texas
1999
A. Dear Jeff ,
the problem to me sounds like a rinsing problem , I would suggest that you agitate vigorously ( with Air ) the rinse between anodising & Black Dye .
The reason is that if the pH of the Dye varies wildly from the parameters set by your supplier then a loss of absorbency will occur with the resultant "Grey" appearance & the production of a "Smutty" appearance .
I would suggest that it would pay you to dump your Rinse after anodising , your dye solution & Final Boiling water seal, as they are probably all contaminated by now .
tell me what eventuates
regards

John Tenison - Woods
- Victoria Australia
1999
A. The way to get the casting black is to modify the surface of the casting -- increase aluminum content in the surface. How can you do it? --
First you need a good caustic etch to remove the contaminated outer layer, than treat in nitric- hydrofluoric acid mix: 10 - 20% of concentrated hydrofluoric acid in nitric (no water!). The parts surface will lose the silica from the alloy and will become almost pure aluminum. The only problem now - it is way too porous to be anodized. Rinse and dry the parts very well. You are going to have to compact the surface layer by blasting it with fresh clean glass beads. After glass bead blast you shall avoid any etch or strong deoxidize: you do not want to destroy the aluminum shall you have just created. Use a mild non-etching alkaline clean and very quickly dip in nitric acid (50%) prior to anodize. Your anodizing cycle seems to be OK. I would strongly recommend to use nickel acetate or some proprietary seal, otherwise you risk getting parts back after a few months due to a significant colour change.
Hope this helps.
Max
captive metal finisher - Montreal, Québec, Canada
1999
A. Dear sir: firstly check the metal composition; second, decrease the time of anodizing; thirdly, heat the black dye and check pH after. Then try it; I think colour is ok?
Lokesh Sharma- Faridabad, Harayana, India
January 18, 2013
Black anodize appearance problems
I received parts which have been black anodized per MIL-A-8625 / MIL-PRF-8625 [⇦ this spec on DLA] Type II, Class 2. However, one of the items looks totally different than the others. The black has the appearance of overspray. I know this isn't possible per the process, just the best way to describe the actual look of the part. The anodizer has certified the part to the spec but I am not comfortable due to the appearance. Has anyone seen this type of finish problem or know what would cause this to show up on one part while the others are the typical solid black?
Peggy Nippertaircraft - Cincinatti, Ohio
2005
What type of aluminum is it?
Bryan Parker- New Mexico
2005
How about a photo of the condition? Overspray conjures up all sorts of mental pictures but they relate to paint and organic coating. As a job shop anodizer for better part of 3 decades, I've seen (and created) a lot of problems - a picture of your part condition might recall something one of the finishing.com junkies have seen before. We stay up all night looking for such opportunities!

Milt Stevenson, Jr.
Plating shop technical manager - Syracuse, New York
2005
Q, A, or Comment on THIS thread -or- Start a NEW Thread