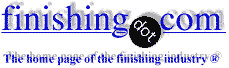
-----
Nickel color stability: yellowing
I have heard/read that electroless nickel will tarnish over time and turn "yellow". Can someone elaborate upon this? How long does this take in an office environment and what is the extent/limit to the yellowing? How does the color shift affect electrical conductivity? Anywhere online I can see pictures or find information? Is this why "Baldwin" locksets in nickel (don't know if they are electro or electroless) have a clear coating over them? Thanks!
Richard Huangmechanical designer - Silicon Valley, California, USA
2004
Most non signal-level contacts are electroless nickel: the charging contacts on your cordless phone, the plug-in charger for your cell phone and laptop, the jacks and plugs for AC adaptors, etc. So you can see plenty of examples and see how 'yellow' they are or aren't. It is common to apply a tarnish-fighting top coat onto electroless nickel to help it retain its brightness; these may be chromate based or organic, but if organic they are very thin and do not interfere with conductivity.
Sorry I'm not familiar with your reference to Baldwin lock sets.
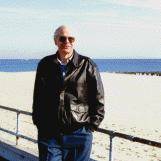
Ted Mooney, P.E.
Striving to live Aloha
(Ted can offer longterm or instant help)
finishing.com - Pine Beach, New Jersey
2003
I agree with the suggestion that you examine an EN plated part to see if it meets your criteria for "white" or "yellow" With most electroplated nickel, we have put a topcoat of Chromium Plating on to keep the part a nice blue chrome color. The Baldwin locksets you mention has me scratching my head. If they are from Baldwin Hardware, they are located in Reading, Pa. Perhaps a phone call or a check on their website would enlighten you. Now, let's suppose that a company is mandated to get rid of Hex Chrome Plating, what can they put on the part surface to prevent yellowing? The obvious answer is an organic topcoat or a lacquer.
Several decades ago, Nickel metal was in short supply. Platers in desperation used Cobalt sulphate in lieu of Nickel sulphate. Much to everyone's surprise, the deposits came out with a gorgeous Blue bright finish. Since then, Cobalt has seen many price rises, and today could well be prohibitive to use for this purpose.
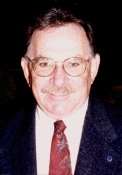

Ed Budman [dec]
- Pennsylvania
With deep sadness we advise that our good friend Ed passed away Nov. 24, 2018
2004
Q, A, or Comment on THIS thread -or- Start a NEW Thread