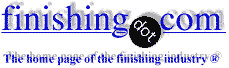
-----
Etch acid for Inconel 718
2003Q. Gents:
Thanks for the reply on my earlier question regarding additives to Anodic Cleaning baths.
I now have a follow-up question...
Background:
There is a "Quality Project" afoot that suggests the use of Anodic Cleaning to remove surface oxides from Inconel 718 (a precipitation-hardenable aerospace nickel alloy). The purpose of removing the oxide layer is to ensure the quality of subsequent welds meet spec (the facility I work in makes parts to aerospace quality standards)...we have intermittent weld quality problems due to inadequate surface preparation (i.e. residual oxide layer not removed during "other" surface preparation methods).
I am concerned that the production of oxygen at the anode during Anodic Cleaning will make the oxide layer even thicker than already exists on the parts (the detail components are procured from another shop) and therefore make subsequent welding even more difficult.
An additional note: our process calls out "alkaline anodic clean" as the first step, followed by "acidic anodic clean."
Question: does the Anodic Cleaning process produce an oxide film on the part? If so, how can the thickness of the oxide layer be approximated? Thanks for the help.
Regards,
David Smith- Beltsville, Maryland, USA
A. First, you must process the parts per the OEM specifications. Second, PWA, GE, RR and a couple of smaller aerospace firms offer a choice of process solutions and frequently a choice of process methods. You have only listed one. There has to be more. Check their standard practices book. Third, Anodic electroclean is not going to add enough of an oxide layer to be found by microscopic methods, The referee method. It also is not going to remove any oxide. Anodic acid etch needs to be handled with extreme care-NO freelancing by the cleaning room operator or you will have scrapped parts-sooner if not later. This does remove metal and oxides. Forth, a moderately standard weld prep includes an abrasive blast or a flap wheel surface prep. Finally, why do you say that the oxide layer is a cause of your weld failures? The vanadium in the alloy gives it very desirable properties and also makes it a bitch to weld by most welders that have not received specific training on that alloy. My money or coffee bets that you also have a microcracking problem that you just have not found. It takes a very good metallurgist to find it.
James Watts- Navarre, Florida
2003
Percentage and quantity of etchants required for Inconel 718
Q. Our project is 'grinding Inconel 718 a small plate'
1. which etchant should we use for Inconel 718?
2. what is the percentage and quantity of the required chemical etchants?
student involved in a project - Lonere, Maharasrta, India
2004
A. One of the best ways to get a good answer is to ask a good question :-)
What is the use of the etch--Metallographic evaluation or for what other purpose. You might include what you are trying to accomplish (depth of etch) as it does make a difference.
James Watts- Navarre, Florida
2004
Multiple threads merged: please forgive chronology errors and repetition 🙂
Q. What would be a good etch acid to use on polished coupons of Inconel 718 and 903 that would show a recast layer in the microstructure where the coupon was cut using an electric discharge machine?
Bob Westonmetallurgy lab technician - Arkansas City, Kansas
2003
A. I would try preparing an Inconel Micro-etch solution that I use myself. For 2.5 lts you require: 1 ltr conc. hydrochloric acid, 50 mls of 40% Hydrofluoric Acid (take GREAT CARE WHEN HANDLING THIS SUBSTANCE), 1.25 lts of de-ionised water and 200 mls of Hydrogen Peroxide (100 vols). Cycle time: 30 secs at 25 °C. This solution is highly acidic and you must observe all relevant Health and Safety legislation applicable to your workplace when using this solution.
Good luck and all the best for the New Year.
Nigel D Gill, B.Sc. MIMF AIEMA MRSC- Blantyre, Glasgow, Scotland
2003
A. Glyceregia is a common etchant for nickel-based alloys. The composition and use instructions are as follows:
15 mL HCl
10 mL glycerol
5 mL nitric acid
Mix fresh for each use -- do not store. Swab the etchant, do not immerse. It has a useful life of < 20 minutes. As it turns color, it becomes overly aggressive. When orange, it can give off Chlorine gas. Do not breathe in the fumes (use under a hood). Discard properly after about 20 minutes.
Toby PadfieldAutomotive module supplier - Michigan
2003
Q. This response is for Nigel Gill, Blantyre, Glasgow, Scotland. Thank you for your response to my question about an Inconel Micro-etch solution. I do not know the meaning of the (100 vols) placed behind the amount of Hydrogen Peroxide in your recipe of the solution. Does it have to do with the strength of the H2O2 or does it mean that you would have reached 100% of the 2.5 lts volume?
Bob Weston [returning]Coating Metallurgy - Arkansas City, KS, USA
2004
A. Bob,
The Hydrogen Peroxide that I use has a strength of 30%, here in Britain it is sold in 1 litre bottles with the term 100 vols added in brackets thus: 30% Hydrogen Peroxide (100 vols) I hope this clears up any uncertainty for you. Good luck with your Inconel etching but please do take care if using Hydrofluoric Acid.
Nigel D Gill- Glasgow, Scotland
2004
A. Regarding hydrogen peroxide, the term "volume" refers to concentration (strength) in the following manner. Example - 100 volume: The quantity of oxygen gas evolved from the liquid upon complete decomposition occupies a volume(at room conditions) 100 times greater than that of the liquid. 100vol. peroxide is 30% H2O2 in water. Drugstore variety (3%) is therefore 10 volume. I hope this helps.
Greg Petersonchemical engineer, aerospace - Anaheim, California, USA
June 11, 2009
Bob,
Has the Inconel Micro-etch solution I mentioned worked for you?
Nigel D Gill, B.Sc. MIMF AIEMA MRSC- Glasgow, Scotland
2004
Q. Could Mr. Nigel Gill please tell me where he acquires 100 vols. hydrogen peroxide in the U.K., as I need a very small amount for cleaning cracks in old china and chemists are unable (or unwilling) to supply it?
Lindsay Lock- Norwich, Norfolk, UK
2004
Q. What would be a good etchant acid to use on polished coupons of Inconel 718 and 903 that would show a recast layer in the microstructure?
Bala Pratapstudent for project - Vellore, India
2007
Hi Bala. Sorry, but I can't understand what you are asking people to do for you! You've cut & pasted, word-for-word, the original inquirer's question that has already been answered with detailed followups :-)
What is it that you want people to do for you? Please spend a few sentences of your own creation, and remember forum netiquette: Always spend longer on your question than you would ask a stranger to spend on it for you. Thanks.
Regards,
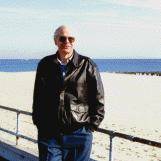
Ted Mooney, P.E.
Striving to live Aloha
(Ted can offer longterm or instant help)
finishing.com - Pine Beach, New Jersey
Q. The Inconel etching discussions previously posted cover a flat coupon, with no corners, or trapped spaces. We are looking for a pre-etch, to prepare for an epoxy bond, a specimen with an inside corner, and many possible entrapment spaces.
Any thoughts on using plain Muriatic Acid - 50% diluted (yielding around 5% concentration), applied to a heated specimen with Q-tips
⇦ on
eBay or
Amazon [affil link] , left to sit for a few minutes, washed off with a water bicarbonate soda mix, DI water rinse, and dried, as a possible process for pre-etch in preparation for an epoxy bond?
shop engineer - Upland, California, USA
December 28, 2011
Q. How to identify whether there is recast layer in the splines made by EDM on inconel 718 material?
suneel kumar- Bangalore, Karnataka, India
January 31, 2014
Hi Suneel. Please clarify how your situation differs from Bob W's, and why the excellent answers provided to him have not helped you. Thanks!
Regards,
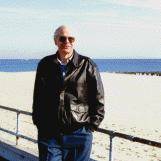
Ted Mooney, P.E.
Striving to live Aloha
(Ted can offer longterm or instant help)
finishing.com - Pine Beach, New Jersey
Inconel 718 drive cones etching issue
from Amazon
on AbeBooks
(affil link)
Q. Having issues with etching of aerospace Drive Cones. Material is Inconel 718. Components are processed through a anodic sulfuric etch. On completion areas of the component are displaying signs of what looks like small blisters on the surface.
Not really sure what we're dealing with here. Is this an etching problem or is it a machining problem that's manifesting itself after etching. Nothing visible prior to etch. Can attach photos for perusal . Any advice appreciated
James FinlayEngineering - Scotland
August 20, 2016
Q. Hi, I tried to perform electro chemical machining on inconel 718 with NaNO3 solution and it leaves a black residue/particles on top. I tried cleaning it with acetone but doesn't go away.
Any suggestion if I can any any mild acids to clean it?
Thanks!
- College Station, Texas US
November 1, 2017
Etching acid for removing possible oxide layer on shot-peened IN718
Q. I am trying to remove a bluish green oxide layer formed on a shot-peened precipitate hardened IN718 thermally exposed to 600 °C for 100 hours. I understand that the oxide layer must have formed due to the surface not being clean or the furnace not being properly vacuum sealed. The objective is to characterize the near-surface residual-stress and cold work using electromagnetic NDE techniques where current injecting electrodes are in contact with the shot-peened surface.
Dheeraj VelichetiResearch assistant - Cincinnati, Ohio, USA
September 26, 2018
Q, A, or Comment on THIS thread -or- Start a NEW Thread