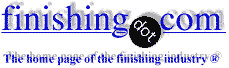
-----
NaOH is attacking 316 Stainless Steel tank
Q. I am a technical services scientist at a vaccine production facility. We use a lot of 316L stainless steel in our processes. One of our 2000 Liter tanks has been found with a large discoloration on the tank's sidewall. The discoloration is a long white streak running almost the entire length of the tank. There is a large black spot in the middle of the white streak. During the process, 10 N NaOH is added directly above where the discoloration is present. Can NaOH have this kind of effect on 316L SS? The tank is old and it is feared that electropolishing the tank might damage it further. We are thinking of trying hand polishing and passivation but are unsure if that will have any effect.
Anne TaylorTechnical Services Scientist - Raleigh, North Carolina
2003
A. Stainless steel alloys are resistant to general corrosion in NaOH up to about 65 °C, regardless of the concentration. What is the temperature in your application? SCC can occur at temperatures ~ 100 °C. If I understand 10N correctly (it's been too long since high school chemistry!), then this is very concentrated stuff. Type 316L may not be the most appropriate grade. More corrosion resistant grades like 7-Mo from Carpenter have better resistance to concentrated NaOH at high temperature. I would discuss this application with them for further assistance.
Toby PadfieldAutomotive module supplier - Michigan
A. Look for galvanic voltages all around and inside the tank. And be aware that just bending a piece of stainless steel sets up a galvanic potential. What is the drag-in? Is it acid? Is the drag-in containing any chlorides? Is the caustic soda ⇦liquid caustic soda in bulk on
Amazon [affil link]
pure (Like PPG "pels") or is it dirty and loaded with Sodium Chloride when it first comes in?
adv.
Call me, I am right here in town.
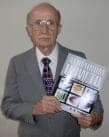
Robert H Probert
Robert H Probert Technical Services

Garner, North Carolina
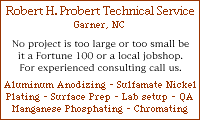
A. NaOH can cause it. Since you mention a long white streak, it might be that that is due to a weld seam. A weld causes less Chromium to be on the surface and is therefore less chemically resistant. The weld seam might not have been properly passivated. The quickest and cheapest solution is passivating that streak with a kind of gel paste especially for passivating stainless steel.
Tjerk de Vries- Weesp, The Netherlands
August 18, 2008
A. Regarding "white stains" and black spot where 10N NaOH is added. I suspect the black spot is due to elevated temperature. A black rouge (magnatite) will form on, and tightly adhere to 316 SS even with exposure to WFI if temperature routinely exceeds 90° C. The white streak is usually micropitting caused by galvanic corrosion in an electrolyte (salt solution qualifies) where the naturally occurring passive surface has failed. Mechanical polishing will damage the 316 down into the material for some depth .0003-.0006" leaving a surface more susceptible to corrosion than the surrounding material (even if passivated). You mentioned not wanting to electropolish an old vessel for fear of doing further damage? In fact just the opposite is true. If properly mechanically polished (sanded) to remove any corrosion damage and micro pitting (primarily to achieve a pre-determined Ra is required)a GOOD electropolish will optimize the corrosion resistance of the 316 perhaps extending the time before corrosion can re-start. Electropolishing offers no risk of damage regardless of equipment age as it is a surface treatment that exposes new alloy with minimal material removal (<.001"). Simply mechanical polishing & passivating will most certainly insure corrosion will begin immediately after placing the vessel back into service due to the damaged (Belby) layer present after any mechanical operation including "buffing".
R. Keith Raney- Houston, Texas, USA
July 1, 2011
Q. Dear sir,
Can we use stainless steel tank to store NaOH solution?
Hossein Parsastudent - Tehran, Iran
2004
A. As per the Erich Rabald Corrosion guide 2nd Edition.
we can use SS-316 up to 100° up to 65% Concentration if there is no stirring (only storage).
Technical services, DRL - Hyderabad, AP, India
July 22, 2010
What grade of stainless for caustic cleaning tank?
Q. I need to build a larger caustic tank that we use to dip our core boxes in to clean them. The caustic is heated to about 40 °C with electric immersion heaters. I need to know what the best type of stainless would be for this application.
Mario RicciNemak of Canada - Windsor ontario Canada
February 14, 2018
A. Hi Mario. I have personally designed many dozen of caustic cleaning tanks used in the electroplating industry made of plain steel. I have seen hundreds of decades-old ones in production. Although I prefer fiberglass these days, if you're going to make the tank of metal, I'd say just use plain steel.
Regards,
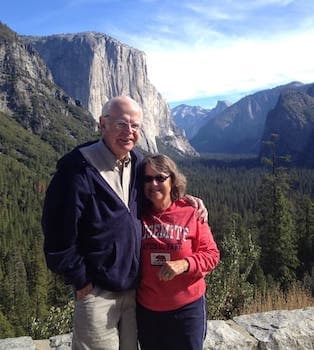
Ted Mooney, P.E. RET
Striving to live Aloha
(Ted can offer longterm or instant help)
finishing.com - Pine Beach, New Jersey
February 2018
Q. Can we accumulate NaOH at 40 °C and 35% concentration in stainless steel pipe 316L. If no, what is the bad effect?
mohamed bakry- egypt,cairo
January 7, 2019
A. Hi Mohamed. I think it will be fine, although I've heard that caustic can leach a bit of Chromium out of stainless steel; but plain steel pipe would be just as good. Aqueous NaOH solutions are not corrosive to steel.
Regards,
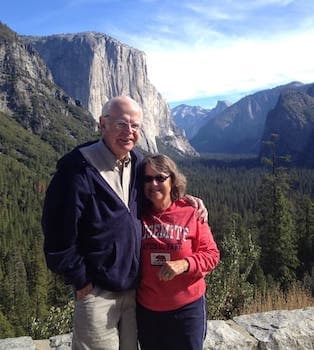
Ted Mooney, P.E. RET
Striving to live Aloha
(Ted can offer longterm or instant help)
finishing.com - Pine Beach, New Jersey
Q. Hello, I am trying to perform an experiment in a 316 stainless steel vessel, involving NaOH pH: 12.8 and 360 °C at 128 bar. Do you think the vessel will be damaged?
Thanks!
- Madrid, Spain
June 3, 2019
A. Meet pressure safety requirements for your industry. This could be dangerous.
(Maybe people stopped posting here because of this?)
- Aiken, SC
February 26, 2024
Good point, Craig. I don't even like to think about 128 bar tanks (operating at hydraulic pressures), but containing molten caustic-- I'm good with laying it on the standards writers.
Regards,
Ted Mooney, P.E. RET
Striving to live Aloha
(Ted can offer longterm or instant help)
finishing.com - Pine Beach, New Jersey
Q, A, or Comment on THIS thread -or- Start a NEW Thread