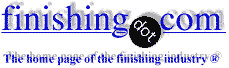
-----
Nickel plating vs zinc plating on air/oil separators
My company manufactures air/oil separators for the air compressor market. All of the steel endcaps are zinc plated (commercial grade) but we encounter customers who want more corrosion resistance and request nickel plating instead. Why is nickel plating better and what can I supply for technical data to support this extra expense. The answer I keep hearing is that nickel is thicker than the zinc with a clear chromate finish.
David P [surname deleted for privacy by Editor]Filter manufacturer - Chicopee, Massachusetts, USA
2003
2003
Hi David. Yes, the nickel plating probably is thicker than the zinc plating, but that may not have too much to do with anything. Nickel is a more corrosion resistant finish in some environments, but is usually not as helpful a finish. It's not really particularly complex to explain, but it does require the introduction of the concept of sacrificial protection ...
Zinc is a sacrificial plating; it does its job not just by coating the steel but by corroding in lieu of the steel corroding. You've probably heard of zinc anodes being used to sacrificially protect the steel hulls of ships, etc. When oxidizing conditions try to steal electrons from the steel, which will make it dissolve or corrode, the zinc will provide those electrons and corrode instead. That makes zinc plating ideal for many applications because it cathodically protects the steel even if the coating is scratched. But zinc has no acid resistance at all, and little alkali resistance, and if the plant environment has acidic vapors (as for example in a plating shop), the zinc will do no good at all. You might also have the issue of sulfurous content in oils, to which zinc plating is not very resistant.
Nickel is a "barrier layer" coating. it protects steel by enveloping it and keeping the environment away. But nickel is not sacrificial to steel; in fact the opposite is the case! So if there is any breach in the plating, from a scratch or pinhole or porosity, there will be accelerated corrosion at the breach as the nickel plating forces the steel to corrode in order to protect it. So nickel is probably only better where zinc has proven itself ill suited.
Electroless nickel is another story, more corrosion resistant than electrolytic nickel plating, but quite expensive.
Luck and regards.
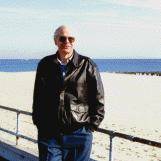
Ted Mooney, P.E.
Striving to live Aloha
(Ted can offer longterm or instant help)
finishing.com - Pine Beach, New Jersey
Q, A, or Comment on THIS thread -or- Start a NEW Thread