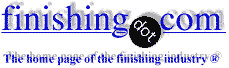
-----
Plating Racks
Everybody at one time or another has heard the statement "the same is not the same". I have a situation which I believe to be in this category. We build our own plating racks and then have another company plastisol coat them. For the past 5 years the copper we are using for the frame and cross members is reasonably hard (rigid) when we receive the raw material. However, after plastisol coating (baked at 360 - 375 F.), the copper loses it's rigidity - can hand bend it with little problem. We used to order this material as B133, Alloy 110 and this material maintained its rigidity and strength even after numerous strip & rework cycles. When we ran into the "soft copper" condition, we notified our supplier immediately and their response was that ASTM B133 had been replaced by ASTM B187 BUT everything was still the same and we were receiving the exact same copper alloy. Based on our evaluations, the material IS NOT the same. Is there anyway I can have this verified - ! I have a section of both the rigid and non-rigid material. Would a chemical analysis verify the difference? What copper alloy is normally recommended for use on electroplating racks? Any information you can supply on this subject would be greatly appreciated.
Rodney Todd- Midland, Ont. Canada
1999
Dear Rodney We also make our own racks and have them plastisol coated. I can't help you with the question about copper because we use brass or stainless steel. We don't have the problems you describe so perhaps you could try changing the material you make your jigs out of.
Regards Simon
Simon Leeelectroplating shop - Auckland (NZ)
1999
The current bake off of Plastisols have changed by many as they try to get around the Lead that was in the "Plastisols of old" . To help you with your problem Copper can withstand 350 degrees for at 25 to 30 minutes before it starts to anneal. This problem can be corrected if they raise the oven to temperature before putting the racks inside. Therefore they do not need to be in the oven longer than necessary for the "bake" of the plastisol. Oven temperature during a bake off should not exceed 340-350 degrees during this time. I hope this helps.
Joshua Swanson- North Providence, Rhode Island
2003
A lot of the problem you are having is in the burn off stage your rack repair supplier is not burning them off at the right temp. You need to have them burn them over a longer period and cut down the temp. I am a rack man for a repair shop.
Bill Atley- Jamestown, Ohio
2005
What you may have experienced is a change in the oxygen content of the material. C110 is electrical tough pitch copper and can contain an indeterminate amount of dissolved oxygen. This acts to pin the grain boundaries and prevent grain growth and softening. It can also contain traces of silver which helps in the same way.
Check the composition for these elements and you may find your culprit if you haven't already.
- Charlotte NC
2007
We manufacture plating racks and use 1010 copper.The problem is not the copper type it is the burn off process.The oven temperature setting is not so much the issue.The plastisol will start surface fires during burn off which exceed 1000 degrees.You need to install a water set up to put out the fires.This requires stainless steel components and can be costly.We use liquid nitrogen and freeze our racks to remove the coating.
Don Lang- Waterbury, Connecticut
June 9, 2009
I agree with the last response. Those fires is where you get the extreme temperatures that soften the copper. Water spray is the best way to keep these under control. A furnace with a good control system will automatically monitor the temps and gas release(which proceeds the fire) and then spray to reduce those emissions and keep the fires to a minimum. Good Luck.
Kevyn Coy- Dayton, Ohio
July 22, 2009
Q. We assemble auto fan clutches and we moved from a phosphate coating to zinc chromate. Our plating company is having issues with the shaft because before the entire surface could be plated but now we need to keep our bearing surface free of the plating. So we are helping them design some racks because he is having issues with his current rack maker.
This will be my first attempt at this sort of job so I was looking for guidance with the material of the rack. Can we use stainless steel and leave it uncoated or do we need to use mild steel and use a Plastisol coating on it? This is a pretty low volume job of about 50K/yr but these racks need to last awhile and we could triple volume.
Project Engineer - Cincinnati, Ohio, United States
January 11, 2013
A. Hi Dustin. There are several major plating rack manufacturers if you are having difficulty with the present one. And you can also review the plating rack design chapter of the Electroplating Engineering Handbook ⇦ this on eBay, AbeBooks, or Amazon [affil link] if you wish.
I'm not quite sure what you mean by "zinc chromate" in this context, but if you mean zinc electroplating with a chromate conversion coating, then plating racks are generally made of plastisol coated copper with stainless steel tips. You can't use an uncoated stainless rack for electroplating, and neither steel nor stainless steel will usually carry sufficient current. Best of luck.
Regards,
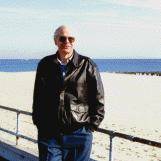
Ted Mooney, P.E.
Striving to live Aloha
(Ted can offer longterm or instant help)
finishing.com - Pine Beach, New Jersey
January 14, 2013
Q, A, or Comment on THIS thread -or- Start a NEW Thread