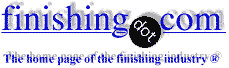
-----
Preserving heat coloring of copper when clear coating
Q. ".. It does 'tone' down the colors a little bit (depending on how/when you apply) but if done right NO color is lost."
Hi, Frank.
Could you explain the "how/when" CBS "done right" comments? Specifics?
Thank you
- Columbus Georgia
June 8, 2024
Ed. note: Frank's posting was from a very long time ago, so we may not be able to reach him or he may not reply. But if you can relate your own experience with your attempts it may draw other replies.
⇩ Related postings, oldest first ⇩
Q. I have tried all forms of heat (oxyacetylene, electric oven and home stove top gas) to produce the effect seen on this butterfly refrigerator ornament, but cannot duplicate the vivid colors.
Courtesy of Mel Owen
Since I have 2 of these I assume it can be duplicated. Is another ingredient (oil?) added or is it a matter of a consistent temperature?
Mel Owen- Texas
1999
A. The coloring produced on the butterfly can be done with heat. You don't have to slather your work in harmful chemicals to get some great coloring. You have to experiment like never before and work with the heat from any torch and "paint" the copper with the flame. You can try working with oils as well. I once was annealing some brass in a kiln and I took it out too soon for annealing but the oil from the factory must have still been on it because it produced some amazing colors and patterns.(The pieces of metal were framed and hung in 'Out of Hand Gallery' in Lunenburgh, Nova Scotia!) Grease may be easier to work with than oil. You have to play a lot with the torch because it is easy to heat the metal too much and the colour will go to a yucky brown. Also try working with folding the piece and annealing it. When you open the work you get some interesting colour patterns due to the amount of oxygen that gets to the metal in the folds.
The trick is to play! Have fun and ALWAYS WEAR PROPER SAFETY GEAR! PROTECT YOURSELF AND YOUR ENVIRONMENT!
M.Jardine- farmington, nova Scotia, Canada
All clear coatings seem to remove the flame colors
Q. I HAVE NO PROBLEM GETTING THE COPPER TO CHANGE TO ALMOST ANY COLOR. This is the copper after heating it.
My problem is losing all the blue, red, and purple colors, When I apply any product to keep the copper from tarnishing. The other photo is after the product is applied.
I have applied a large variety of products and none have worked to my satisfaction. I will be very pleased for any advice you can offer.
SONNY GRAHAM- OZONA, FLORIDA
2002
Q. Yes, I have the same situation as Sonny. I have tried spraying the heat-colored copper with clear Krylon or lacquer, but it seems to oxidize beneath the surface of the clear sealer (about 6 months later). How can I preserve the heat-produced colors without having oxidation? I also often have a roughened, sanded surface, so I'm not sure if wax would be an option.
John Waters- Phoenix, Arizona
A. Unfortunately, I don't have great news for you, Sonny and John :-(
Although some portion of the coloration may be oxides and sulfides and other pigmented colors, most of the pretty coloration is from diffraction patterns like the rainbow sheen of a drop of oil on water, rather than from pigment. Oil isn't really rainbow tinted, it's the way the very thin layer reflects the light; part of the light reflects from the top of the oil, part of it from the bottom, and it's so thin ('partial wavelength') that the two streams of returning light are out of phase with each other, causing amplification of some colors and suppression of others as the thickness of the layer varies, causing irridescense.
As soon as you put a clear coat on your piece, it's rather like trying to lay a sheet of glass over that oil rainbow to preserve it. The colors that are "really there" as pigments will be retained, but the diffraction colors can tend to disappear.
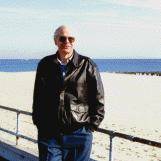
Ted Mooney, P.E.
Striving to live Aloha
finishing.com - Pine Beach, New Jersey
A. Try using OIL-based polyurethane instead of lacquer. Or another oil-based product.
The problem with water based products and many of the lacquers which are acidic is their reach with the copper creating another patina, not necessarily the one you want.
I have not tried this with colors like yours, but I've used it on both bare brushed copper and sulfurated potash patina copper (mostly dark colors) and it preserves most of the color.
I have a copper dining set I made about 7 years ago and it's still pretty much same color (that picture is when it's about 4 years old).
I just experimented with several brands and price does not seem to make a difference. Cheapest worked same. Polyurethane also has the advantage of being flexible, unlike lacquer, which will have hairline cracks after a while for temperature expansion and shrinking of the copper and will lose its protection.
I've tested it by bending a coated piece back and forth and them leaving it in salt water for a month with no visible tarnish while the lacquer piece turned black.
Alik Perakh- San Diego, California
Q. I am a hobbyist making copper wind chimes. I am burning the copper chimes with a propane torch to bring out the different colors in the tubing. When I put a finish on the pipe, the colors fade and and some colors, like purple, disappear completely turning to orange. I've used lacquer, Rustoleum products, shellac and a variety of water based (acrylics) clear finishes used for hobbies and purchased at hobby stores all with the same results. Does anyone know of any kind of finish either brush on or spray that will not change the oxidation of the pipe.
Tony Wrighthobbyist - Huntington Beach, California
2004
Q. Hi
I am trying to preserve the color on HEAT patinated copper. I have tried water based Incralac, paste wax, spray lacquer, Krylon 1301 ⇦ on eBay or Amazon [affil links] . The best results have been the Krylon. However it still changes the color. Do you think that a solvent based Incralac ⇦ on eBay or Amazon [affil links] will work better at preserving the color? Thanks for you input.
Bruce MacKimmie- Moss Beach, California
A. Hi. I make penny whistles from copper and heat color them. I have had very good luck finishing them with Brass Lacquer. It is formulated for brass and copper and works well. It is somewhat costly, but it works. Look for it on eBay , sometimes you can find a good deal.
Rick Hinck- Holyoke Colorado
Q. I have tried many things to ensure that my copper fountains remain nice and shiny waxes and acrylic finishes. But unfortunately of all of them the worst thing I have found is putting a lacquered finish on them. Whether it's the combination of outside elements or the water or both I don't know but it begins to discolour after a couple of months and the finish begins to really look drab.
I am experimenting with a company in the UK that works with clear powder coating, and I am trying to get something that is ok to use outdoors with water over a long period. It might be a while till I get a decent result but if it works I'll post the info later in the year.
- London, UK
A. I have had great success keeping the blues, purples, and reds in my flame treated copper. I worked with my local powder coater and found that a clear finish baked at half the time usually required, does the trick. It allows the powder to melt to a clear glaze and give the copper a depth that spray on treatments don't allow, but by leaving it in half time, the copper doesn't heat up too much to change color.
Emily Lewis- Burlington, North Carolina
A. I understand the problems of losing colors after heat coloring. I do steel coloring. The best way is to use cold rolled steel. After you obtain the effect you want, leave it set over night or longer and let it cool down. Then I use a spray called EnviroTex high gloss .
Hold the can at least 18" from the piece working on and spray a light coat. Let this dry and then do the same thing again. Do this several times but DON'T GET TOO CLOSE. You might lose just a little lighter blues but the deep blues and purples will stay. Also the clear powder coat will work at half the baking time. When the powder starts to glaze over I shut the heat off and pull the piece out of the oven There is a new low heat clear powder coat coming out. Don't have the info on it yet.
Mike LeMasterwelding - Delta Colorado
2007
A. Hey, I do a lot of heat coloring on all kinds of metals, the best thing I have found is
RENAISSANCE ⇨
it's a micro-crystalline wax polish. It's a little expensive but the best thing I found that leaves a natural finish (not shiny glossy). It does "tone" down the colors a little bit (depending on how/when you apply) but if done right NO color is lost.
- Glen Burnie, Maryland
January 24, 2008
As we all know, if you put a drop of oil on a puddle of water you'll see a colorful rainbow sheen. The rainbow colors are not the color of oil, they are an interference/diffraction pattern, a prism effect that results when light encounters a very thin film of transparent material.
Some of your heat coloring colors are real pigments and patinas. But some of the colors, especially the more subtle, are not: they are diffraction patterns caused by very thin films of oil or clear oxides on the surface. The clear coating removes these colors not by chemical reaction or yellowing (alone) or filtering, but simply by being there. If you study the subject of carnival glass (which also gets it colors from diffraction patterns, not pigments) you may find something useful about film thickness, etc., that can help you preserve heat coloration. Just a thought, for what it's worth, from someone who doesn't practice the art but believes you that, based on this, the wax is the best bet :-)
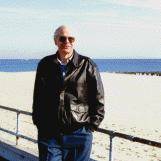
Ted Mooney, P.E.
Striving to live Aloha
finishing.com - Pine Beach, New Jersey
Flame coloring to bring out the colors
This meeting place welcomes Q&As, photos, history, & interesting tidbits.
Please engage with other posters
• When people show interest in each other's situations, the page quickly becomes a fun & informative learning experience for everyone !
• When people show no interest in other people's postings, and just post their own, it often quickly deteriorates into a string of unanswered questions 🙂
Q. Please tell me where I can find help. I want to heat 110 copper sheet .032 gauge .. I want to bring out areas of orange, yellow, red, etc. What common tool can I use and how hot should it be? Is there a website, article or book that you can suggest? THANKS BUNCHES
Dottie Cesariohobbyist Tampa, Florida
2004
Q. I am interested in what you have discovered re: coloring of copper with varying temperatures. For a different reason, though. My apron front copper sink was damaged, and it had a "Fire and Ice" finish on it that was beautiful. It had to be polished off during the repair, and I would like to replicate all the colors that were represented. (I realize I can't replicate it exactly.) Thanks for any info!
Peggy Thomas- Amarillo, Texas
Q. I create metal sculpture for patio and poolside with 18 gauge sheet metal. I'd like to add random color (blue and whatever other hue possible) to the sculpture using my oxy-acetylene torch. How is this achieved and what settings do I use on my regulators? Have looked for books on the subject, but can't find any.
Polly Fiskmetal artist - Dallas, Texas
Q. Getting red from copper with a torch. I am new to coppersmithing and have been trying to get the color in my leaves and butterflies when I cut them out with the torch. Does anyone know how to do this? Is it in the regulator settings or what? I have tried everything.
Jeremy Whitmirecoppersmith - Copper Country, Michigan
2006
A. I've managed to produce a wide range of hues on copper with an ordinary propane torch. The trick seems to be in heating the copper to a high temperature and then using the torch as you would a paint brush. Heat one portion of the piece until color starts to appear and then experiment. A long time under the torch close to the heart of the flame produces pale greens, silver, and gold. A quick stroke with the edge of the flame produces blues. A longer time at the edge of the flame produces reds and pinks.
Joe Nicholas- Kansas City, Missouri
A. When I do small projects on copper, I usually get a nice fire-scale effect by "painting" the parts I want to color up with flux (flux for hard solder), letting it dry, then turning the piece over and heating it from the back.
I usually heat it pretty hot to get a nice red color, but keep the flame away or it'll burn the flux and turn a funky color. Use the flux lightly...
- Santa Cruz, California
2007
A. If you want to turn copper red, heat it as hot as you can get it without melting it then dunk or spray it with water. When I make a rose from copper this will make a very bright red rose.
Lyle Wynnblacksmith - Flowood, Mississippi
2007
Using bromide salts or potash for colors
This meeting place welcomes Q&As, photos, history, & interesting tidbits.
Please engage with other posters
• When people show interest in each other's situations, the page quickly becomes a fun & informative learning experience for everyone !
• When people show no interest in other people's postings, and just post their own, it often quickly deteriorates into a string of unanswered questions 🙂
Q. We are trying to create a tropical sunset scene in sheet copper and would like to embellish the work primarily in blue and red hues. A metal worker mentioned applying bromide salts to the metal prior to heating with a propane torch. Has anyone had any success with this method? Any other recommendations?
Thank you!
Bob Yeamans- Columbus, Ohio
2004
Q. I would like to know what process I need to employ in order to discolor either copper or brass. I believe what I want to do is etch the metal, but I don't know what chemicals to use or possibly how to heat it to accomplish this. I'm working on a a logo which will be large and want to use discolored and/or distressed metal. Any help you can offer will be appreciated.
Thanks
Paul Le Painartist - Dunedin, Florida
Q. I would like to know the best way to bring out color in brass using a blow torch. Should I use something in addition to heat. Also, what is the best way to keep the colors? Should I polyurethane it? I want to make art objects with copper and get the beautiful purples and golds from the heat.
Lynn Schmoockhobbyist - Hillsborough, New Jersey
Q. How do I use potash to color my copper project? I'd like to find out what the application is and how and what do I mix the potash with?
Ross D LairdPrimal Iron Originals - San Diego, California
What is the chemistry of heat coloring?
Q. I was trying to form an oxide film on copper by thermal oxidation at 350 °C, in ambient atmosphere. After 10 minutes, there was a gray film on copper, which I assumed was CuO. After about an hour at 350 °C, the surface became multicolored with patches of pink, violet and gray/black! What are the possible compounds that cause these colors?
Nandini VenkataramanStudent Researcher - Tucson, Arizona
2006
Q. I am fairly new to copper work. I do not use sheet copper, but rather cold forge heavy copper wire. I have been experimenting with different patinas and coloring techniques and am very fascinated with heat coloring. I experimented some using the broiler of my oven and achieved a gorgeous hot pink/purple color. However, as soon as the copper cooled, it faded quickly to orange...a very nice bright orange, but NOT the color I wanted. Is there a way to keep that lovely pink color? I had not seen it before in any finished copper work, so I am very curious if it is just a color that shows up when the copper is hot, or if it is possible to keep that particular shade. Any help would be great appreciated!
Genevieve Lancasterhobbyist, designer - Atlanta, Georgia
April 30, 2008
A. I've been working with copper for about 13 years and have gotten some beautiful iridescent-like patinas with liver of sulfur
⇦ on
eBay or
Amazon [affil links]
. It's a benign substance, available in crystal form from any chemical supply house or in liquid form from any garden center -it's the orange liquid part of Dormant Oil Spray that's used to spray fruit trees in late spring and cheaper than the crystals. Liver of sulfur is a substance that smells like rotten eggs (remember stink bombs?), so take care where you use it.
It should be mixed with water and makes a very light brown to black patina, depending on the ratio of water to liver of sulfur. Less water = darker color. I get the nicest iridescent coloration when I apply with a brush. Experiment with different ratios on scrap until you get an effect you like. The effect is instant and if you don't like it, clean the copper and try again. The patina isn't stable so it has to be lacquered after the desired effect is achieved. Additionally, the water mixture loses viability fairly quickly, so only mix what you'll use in a few minutes -30 minutes, tops.
I hope someone finds this useful.
Cheers!
- Kingston, Ontario, Canada
June 10, 2008
A. I am currently a student concentrating in metalwork. I have experimented extensively with heat patinas, and I have learned a number of things that I haven't seen addressed on this thread. I use a propane torch with the broadest tip I can find, the heat should be very general and not focused too much. On larger pieces I even use a rosebud tip. To produce an even color you need to heat the copper evenly and in very small increments. The final color will only come out after the copper has cooled, so pull the torch away and just watch the piece. Colors will develop as the copper cools. If the piece was not heated evenly it will have inconsistent color. The trick that I have learned, and have had extraordinary success with, is air cooling (NOT QUENCHING! submerging in water will cause the color to flake) as quickly as possible. I do this by running outside in the winter and swinging the piece through cold air. You can also stick it in a freezer when you see a color you like develop. Don't sit the piece down on the racks in a freezer, though, it will cause the color to be uneven in the places where the metal touched the rack. Using an air compressor [adv: air compressors on eBay or Amazon [affil links] and blowing on the piece is quite effective as well, the compressed air is quite cold. It has taken me many experiments, and many failures, but I am able to pinpoint any color in the color spectrum by heating slowly and evenly, removing heat and observing, and air cooling as quickly as possible. Even though I consider myself quite skilled at applying heat patinas, I still pickle most pieces and start over multiple times to pinpoint the exact color I am looking for, every piece will be slightly different depending on it's size, inconsistencies in thickness, and, sometimes, shape. As far as sealing a color, I have found nothing to be effective, personally I like the idea of an ever-changing piece, if you really want to, you can always clean it up and reapply the patina after it is lost.
Cody Pinnow- Menomonie, Wisconsin
May 4, 2009
A. I make wind chimes with flame colored copper tubes. I seem to get better colors by heating the tubes with the torch until the colors just begin to come out then I let it "rest" and cool for just a couple of minutes then hit it again with the torch and really make the colors come out. I also found a product that really seems to work and not dull the colors. It is called X-I-M 900 clear coat ⇩. It is designed to protect polished nonferrous metals. I holds up extremely well even outdoors and doesn't seem to dull the colors. I found it at my local professional automotive paint supply company. It's made by XIM Products; they sell it online. USE 3 OR 4 LIGHT COATS. It looks a little frosty at first but quickly dries clear. Good Luck.
- Canton, Ohio
December 21, 2009
Ed. update Dec.2023: We strongly doubt that X-I-M 900 clear coat exists anymore. We do not see it listed nor available for sale anywhere.
Protectaclear from Everbrite [a finishing.com supporting advertiser]
Q. Why does the color of pure copper which is used in Cyclotern change to rainbow color by heating with burner?
Can I make an exact duplicate?
employee - Kolkata, westbangal, India
January 12, 2010
A. Hi, Deba. I would assume that the rainbow coloration is oxides of copper as described on this page. I think making a duplicate is more about artistic skill and experience than scientific understanding of the technology. In other words, I doubt that I could make a duplicate, but I believe that a skilled metal artist could :-)
Good luck with it.
Regards,
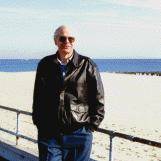
Ted Mooney, P.E.
Striving to live Aloha
finishing.com - Pine Beach, New Jersey
A. Hi All.
I work extensively with Niobium and Titanium patination, so I have some info that might help.
The rainbow colors is light diffraction caused by clear oxides. The color is dependent on the thickness of the oxide.
Scientifically, the ratio of oxide thickness to light wavelength determines the final color you see.
The answer is therefore to wipe the flame across and experiment. There is no way to tell exactly how much.
An atmosphere high in oxygen would help. An oxyacetylene torch would be best, with the oxygen turned up high.
- Wilbraham, Massachusetts, USA
October 23, 2010
A. It is possible to color copper with heat and preserve the colors. I've been doing it since the early 90s. The colors I can achieve are copper, brown, purple, blue, green, yellow, orange, rose, and black. It does however take many, many hours of trial and error.
Verrel Martin- Fulton Missouri
A. I haven't done much with copper, and I've only used a torch on silver in a class, I didn't seem anyone mention using a heat gun ⇦ on eBay or Amazon [affil links] , it's like a super hot hair dryer apparently used for peeling paint, anyway one day I was in my basement and there was the heat gun and a piece of copper, so I turned it on and used it on the copper, it worked very nicely, the copper going through all the color stages as it progressively got hotter, it also seemed very controlled to me. Just thought I'd put that out there!
Logan Swift- Monmouth, New Jersey, USA
April 4, 2011
A. I recommend using an oil based lacquer. A few coats is all you really need. If you want more protection, you can spray one coat of lacquer followed by a self-level epoxy that you can pour on the surface. The combination of the two makes the copper really "pop". The plus side of the epoxy is that you can sand it down and pour a new coat on top after a few years of wear and it will look brand new again. Hope that helps.
Don AngeloSpring Hill, Tennessee
May 19, 2011
A. Another reason why your heat patina might not last or look the same as it did is in the nature of the patina itself. If the piece is going to be outdoors the metal will eventually be heated and change color. I learned this from experience. I had this happen with one of my pieces that got left in the car in the summer for a bit. It looked washed out afterward. Besides being in the car nothing touched it, not even direct sunlight.
I've had another piece that I have sitting inside that I did, I haven't put a clear coat on it of any sort and it's fine. The heat patina will last a long time, but it's in no means a completely permanent coloring eventually it will fade and tarnish clear coat or no.
- Lubbock, Texas, USA
December 10, 2011
Q. I am just starting out soldering copper. I make jewelry. I saw a clasp that I was told was copper with a layer of gold over it, and it had the rainbow colors in various places. Does anyone know what this technique is called and how I can achieve it?
Thank you,
Verlynda
- Charlotte, North Carolina, USA
November 26, 2011
Q. I have copper chimes that when new were multi-coloured. I hung them outside and now the colour has gone. The tubes are dark brownish now. How do I bring them back to the original state?
judi
- Gabriola Island, BC, Canada
June 10, 2012
Q. I frequently use fire on my copper artwork and have also tried everything to preserve all the colors, especially the pinks, to no avail. Recently I put a piece in our campfire and the result was just beautiful after a quick dowse in cold water. Not wanting to lose all those colors, I tried something different....a clear semi-gloss polyurethane which dried rather quickly and left a nice shine. I did not lose any color at all!
I still need to test it and see if it will stay on the copper and not yellow. I also use solvent inks in my work and need to test the urethane with that. Anyone see any issues with this?
Kim KellerCopper artist - Franklin, Pennsylvania, USA
September 18, 2012
Q. I create copper art and have the problem with color loss after applying polyurethane. It doesn't sound like there is any solution to this. My question is:
If I put my copper art in a frame behind glass which is sealed from the elements and indoors will it still oxidize?
I'm wondering if I can not coat it. leave it the beautiful colors, or will it tarnish and look bad in future years?
Anyone not coat their copper? What are you results?
Thanks.
- Brush Prairie, Washington
May 29, 2013
A. Hi Paula. It seems to me that there would be museum techniques that would preserve your copper art as it is, probably including either sealing them in a nitrogen environment, or including volatile corrosion inhibitors (VCI) within the framed areas if a real hermetic seal weren't practical. Good luck.
Regards,
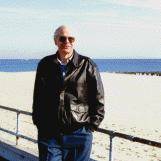
Ted Mooney, P.E.
Striving to live Aloha
finishing.com - Pine Beach, New Jersey
May 30, 2013
Q. Do you think since I frame my copper in frames with glass that it wont patina or tarnish since it is sealed in the frame. I really hate to put anything on it because everything diminishes the colors?
How many years would copper last before it started changing indoors? Thank you.
- Brush Prairie, Washington
May 30, 2013
A. Hi. I'd try applying sodium benzotriazole ⇦ on eBay or Amazon [affil links] as this is a preservative rather than a clear coat, or I'd try incorporating a little VCI (volatile corrosion inhibitor) hidden behind the glass in the frame. Obviously, experiment with scrap rather than precious works.
Regards,
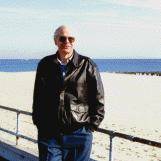
Ted Mooney, P.E.
Striving to live Aloha
finishing.com - Pine Beach, New Jersey
May 31, 2013
A. I clean off my fire painted copper with acetone ⇦ on eBay or Amazon [affil links] Warning! Flammable! . The colors are brighter and deeper and do not fade!
Donna HancockJewelry maker / Artist - Corpus Christi Texas
October 5, 2024
![]() |
Q. Has anyone tried the process "Physical vapor deposition"? - Bethpage, New York, USA October 7, 2014
But yes, they are used to apply titanium nitride, zirconium nitride, and similar "lifetime finish" to brass faucets and door hardware. Thanks. Regards, ![]() Ted Mooney, P.E. Striving to live Aloha finishing.com - Pine Beach, New Jersey October 2014 |
Q. I am looking for a coating for copper that has been coloured by heat. Some products will cover to protect but the colours will be darkened. Has anyone any ideas.
Thank you.
Hobby - Northumberland England
November 24, 2014
Q. Is there any reason not to just leave flame patinated copper as it is, without sealing? I haven't been at it long enough to see how it ages if unsealed. It seems to me it would just get more interesting over time if left alone.
Julie White- Avant, Oklahoma, USA
January 28, 2015
A. I have an answer for holding color in torched copper if it has not been answered here already. It's a new product called "ColorLoc" made by Sculpt Nouveau and listed under sealants. It's meant for this purpose. You put a layer of ColorLoc on first and finish it with a layer of Clear Guard.
Hope this helps
Mark
- Lompoc, California
A. I hope that the following information will be useful. It will be most relevant to the subject of copper and patinas changing colour over time. It's a bit long (sorry) but I think, and hope, it contains some helpful bits, or at least interesting. Thank you.
The British Museum in London, UK uses Renaissance Wax
⇦ on
eBay
or
Amazon [affil links]
for much of its metal pieces. For example, when ancient metal (iron or steel) armour plating has been cleaned and restored, Renaissance wax maintains the metal surface in its pristine, restored condition and, if applied correctly, does not alter the degree of shine much.
Also in the UK, local authorities are some of the biggest users of Renaissance Wax. They apply it to bronze statuary, displayed on street pedestals and affixed to exterior building walls, to maintain the patina and protect it from the elements all year round. As you might know, the UK weather is amongst the most changeable on Earth - temperatures from 30+ to -10 or lower, centigrade, and dry, humid, frequent showers and rain, snow, hailstorms. It can change on a daily or weekly basis depending on the jet stream and other factors.
I don't know if there is much copper statuary exhibited outdoors in the UK, so I can't give any information about that.
However, about 10 years ago I did a lot of conservation work on three Nepalese copper Buddhist statues for a UK Buddhist charity. Parts were heavily gold plated using the ancient copper-mercury gilding process. Other parts were beautifully patinated. There was a lot of contamination due to surface etching with nitric acid which had not been properly removed from surface pores. Remnant mercury salts, nitric acid and various compounds were leaching out, threatening to eat the statues from the outside. Inside, "bronze rot" had taken hold and was escalating rapidly in the British humid atmosphere, threatening to eat the statues from the inside. Also, remnant acids trapped in pores inside the states were already eating their way through the statue, causing tiny holes to appear on external surfaces. After removing as much of the corrosion and residual chemicals as possible I sealed the inside of the statue with a "vapour barrier" composed of an acrylic formulation dissolved in acetone; I then loaded the nasty solution with glass "micro balloons" to help the barrier solution work its way into crevices, surface pores and various welding faults. Several layers produced a completely impermeable layer against the atmosphere inside the statue. A similarly treated copper base plate was then resin bonded to each statue, the resins being loaded with mixtures of copper and bronze filings for colour matching. So that fixed the inside. Now for the outside.
First, I filled all holes with my acrylic solution or two-part resins loaded with metal powders and/or earth pigments for colour matching - tricky work. Then I painted the entire surface with an acrylic solution - except the face and other parts that had been mercury-gold plated or painted with a pure 24 carat gold powder "kind of gouache" and precious stone pigments. Then, the entire statues' surfaces, except the precious stone and gold pigment painted areas, were treated with 3 applications of Renaissance wax.
The unpredictable risk was whether there were any chemical contaminants inside the copper casting underneath the painted areas, which I couldn't seal externally. If anything broke throughout these areas, the beautifully delicate painting would have to be removed, then repainted using pure gold gouache, which isn't available, so has to be custom made by experts, and no-one in Europe (and probable the USA) makes gold powder fine enough - the finished gold gouache has the same reflectivity as human skin.
If any atmospheric contamination penetrated the vapour barriers, or if I had trapped any significant amount of humid air in the copper surface defects, patinas would change colour, copper would oxidise - except where I had used metal powder loaded resin fillers - thus, if the copper changed colour, my patch repairs would become increasingly obvious.
After a couple of years or so, I returned to apply more Renaissance Wax, "to be sure to be sure". Everything seemed to be good.
I have checked with my client, now and again over the years, the last time, after 10 years, in July 2015. There has been no noticable change. I know 10 years is nothing in the world of renovation, conservation and art, but the statues have been displayed in a bright, well light room, handled on a regular basis by non-experts for regular dusting and cleaning, and have been transported often around the country to be displayed in all sorts of well lit environments. Transportation has usually been simply wrapped in silk and put in a box.
So ... I know the details of vapour barriers inside the statues are of little relevance to jewellers and surface-artists, but I thought I'd describe in detail the problems I faced, which you will probably agree were extreme to say the least. I think the processes most relevant to this thread are:
1. If an effective vapour barrier is not applied, chemical change and discolouration will happen.
2. If any residual chemistry is not washed out - and that means washing chemicals out of the tiny surface pores created by acids and other corrosive chemicals - then chemical process will continue below an effective vapour barrier until the chemistry has "run out". In this case colour change is likely - but will continue if corrosion causes a chain reaction - that is, where a chemical process causes by-products that are also corrosive. For example "bronze rot" is a chain reaction wherefrom the atmosphere must be completely removed unless your piece can be expertly treated by lengthy chemical deep soaking. I couldn't deep soak the statues because I had to retain delicate gouache paint decoration. In your case you want to retain the patinas, which deep chemical soaking usually removes.
3. An acrylic vapour barrier is effective, theoretically - it requires very painstaking application. Usually, however, it is not sufficient to apply just one layer. In my case, several layers would completely destroy to external appearance. In any case my reason for using acrylic solutions was to try to completely real most surface defect. So I opted for final treatments with Renaissance wax.
In conservation a general rule is, "every process must be reversible". As I mentioned, many of the British Museum's metal artifacts, and bronze street sculptures in the UK, are treated only with Renaissance wax.
All my formulations were considered in consultation with the metals conservation department of the British Museum, and the wonderful experts at Conservation Resources Ltd, in Abingdon-on-Thames, Oxfordshire, UK, from whom I purchased all the necessary chemistry except resin fillers and metal powders which I purchased from from a sculpture materials supplier, Alec Tiranti in Thatcham, Berkshire, UK. Please note that The British Museum is not chartered to provide free consultancy for businesses or individuals who sell their products. A Registered Charity number for a non-profit organisation is required.
There will be good materials suppliers in your own countries. I have found them to be happy to examine artifacts and discuss solutions; just find one that is not just a retail outlet, but which has in-house expert conservation chemists.
- England, UK
Q. Hey George
I want to use this coloring for a drinking cup, do you know which cover / lacquer to use so the patina won't change its color after painting and will be food safe?
All the covers I tried to use changing the colors of my project
Thanks a lot :)
Yael
- New York USA
January 28, 2017
A. Hi Yael. I don't know who George is, since there are no postings with that name on this page, but I don't think it is wise to try to make a patinated copper vessel food safe with a clear coat.
I've tried to explain why every clear coat will always change those patina colors: it's because the colors result from light bouncing off the outer surface of the flame patina, and also bouncing off the inner surface (or copper surface below the flame patina) and the two reflected lights interfering with each other. When you add a clear coat layer, now there is another surface the light is bouncing off of, so the result will always be different than before the clear coat.
Regards,
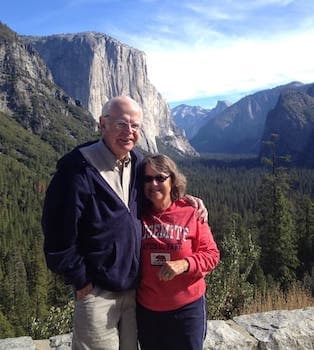
Ted Mooney, P.E. RET
Striving to live Aloha
finishing.com - Pine Beach, New Jersey
Q. I have also been working with flame painted copper. I have done several pieces for a local pub and my largest piece is for a cooler door. The colors were beautiful, although as others have said, they were a bit muted after I applied a finish. I used lacquer initially, since many folks seemed to feel that was appropriate for color maintenance.
It worked well, but within about a month, there were sparkly spots. I assumed that it was some sort of oil from the hands of the fabricator who did the wrap on the door, so I cleaned it with alcohol, and reapplied another layer of lacquer. It occurred again, now also on another piece, which I also recoated. It was effective for a week or two, then it began to appear again. It wasn't from handprints this time, just random areas.
I did some research and found that acrylic could be coated over the lacquer, and did that. It worked beautifully...at first. Now there is another sparkly area beginning again on the door, not in any hand-touching area. Has anyone else had an issue with sparkles appearing in the finish? I plan to re-coat with acrylic again, but am wondering why this is happening only on this door and not the other pieces which were done in exactly the same way. Any help would be wonderful! Thanks.
Debbie Burns- Lenoir, North Carolina, USA
May 31, 2017
A. Hi Debbie. Paints and lacquers are generally not water proof, but slowly breathe moisture in and out. In fact, if they are too waterproof, that can be one cause of blistering.
I'm not sure that I fully understand your description, and don't really have experience with this, but a cooler door is cool and is constantly pulling moisture out of the air as condensation. This probably is the cause of those sparkles appearing on the cooler door and not elsewhere. I am not familiar with commercial coolers as in your question, but home refrigerators have tiny heating coils in the door which you can turn on to stop this condensation.
Regards,
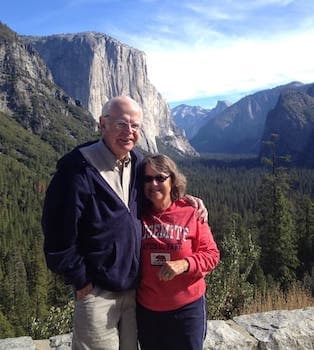
Ted Mooney, P.E. RET
Striving to live Aloha
finishing.com - Pine Beach, New Jersey
A. I flame torch copper and have had luck with ColorLoc by Sculpt Nouveau; it locks in those blues and purples. It's expensive, not the product, but it costs the same amount to ship as the price of the product -- but worth it.
Jude LobeOsprey Studio - Mebane, North Carolina, USA
A. Hi I have just finished torching some copper sheets to use as decorative risers on a staircase. Got those great blue sand gold tones that I was looking for. Then wiped over with CorrosionX and retained almost 100% of the colouring. A lot easier than half time powder coat clear mentioned above.
robert humphris- fawkner Victoria Australia
Hi Robert. I suspect that your process is not only easier and cheaper, but works better initially. The test will be how long it lasts. Try to remember to get back to us in a year or so. Thanks!
Regards,
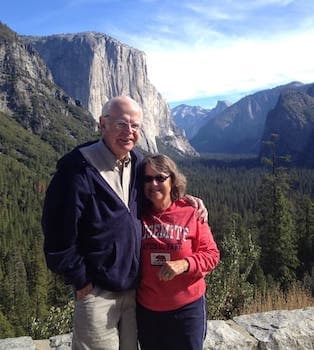
Ted Mooney, P.E. RET
Striving to live Aloha
finishing.com - Pine Beach, New Jersey
September 2018
A. I put a clear coat on my torch painted copper today and it works!
It was on my shelf in my craft room. I think I purchased it at a store that sells silver, chains, findings and tools years ago. Can't believe I had something since torch colored fish and hummingbirds turned dark with powder coating.
The name of the product is ProtectaClear by Everbrite, Inc.
Website is www.everbritecoatings.com/ProtectaClear.htm
Phone # 916-852-0200
Hope this helps someone. I spent lots of time reading this site, learned a lot but had my own answer! Lol
- Sun City Arizona
December 14, 2020
A. Hi Kim, I've been using the Protectaclear from Everbrite [a finishing.com supporting advertiser] for a number of years now. It works very well. I apply two or three coats. I use an artist's paintbrush to apply it and then dry the pieces in a dehydrator. You will notice that some of the colors will change when you apply the coating which is normal as the coating blocks out the UV rays of light. The reds and yellows will become more vibrant and other colors will turn a warm brown, etc.
Connie Tyler- Crossville, Tennessee
June 21, 2023
![]() |
A. Thanks, Kim and Connie! We don't normally post brand suggestions or sourcing or we'd drown under spam, but Everbrite is a supporting advertiser of this site, so we're certainly delighted to offer your postings as an infomercial :-) Luck & Regards, ![]() Ted Mooney, P.E. RET Striving to live Aloha finishing.com - Pine Beach, New Jersey |
Q. I got a tough one for you:
Is there a coating or wax on the market to preserve the reds and purples and blues on a billet of heat-treated copper that could withstand kiln-firing temperatures for purposes of making makume gane? If not, do you have proposed workaround for that? If so I would love to hear any suggestions you may offer!
Andrea McClellan- Columbus, Ohio USA
October 22, 2018
Torch blackening of brass
Q. Has anyone used a kiln or torch to blacken brass. I use it on copper, then eliminate some and patina, there remains a great look on copper. So wondering if any one tried this for brass. Of course wear a mask, ventilation, etc. Look forward to any heat treat patina responses.
Peter Smarshjewelry, Florida Usa
May 17, 2019

Q, A, or Comment on THIS thread -or- Start a NEW Thread