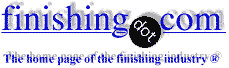
-----
Nickel stamper separate with another nickel plate
2003
Hi,
I am a rookie in electroplating field for several months. I read some interested articles on this website and most of these information are useful and helpful in my subject.
Presently, we face one interesting question. If we want to electroform another Nickel layer upon a original Nickel stamper, we have to passivate the original fresh Ni stamper usually. If we do so, it is easy to separate the original and the new layer. Otherwise if we don't, the new one will grow with the original one and can not be separated.
But our process is quite different than before. We plan to do some experiments on the original Nickel stamper. After that we expect to electroform again for a thicker plate. However, the result is unexpected, the new plate is separated easily with the original one, not our demanding. Some thin layer is formed and it plays a role like passivation. Is it possible a Nickel oxide layer? if it is, how to remove it? Or can we do some procedures to protect the surface to keep it always fresh. To form another thin layer and this one is removable easily. Hoping to get any help in a short time.
associate researcher - Tao-yuan, Taiwan
The conventional separating agent is sodium dichromate. Once you have passivated the surface with this, it may prove difficult to reactivate it, but you should be able to start again with Wood's nickel strike I think.
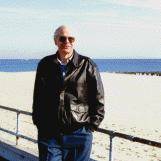
Ted Mooney, P.E.
Striving to live Aloha
(Ted can offer longterm or instant help)
finishing.com - Pine Beach, New Jersey
2003
High nickel alloy and pure nickel will passivate quite rapidly. Yes, it is a very very thin layer of oxide. The oxide layer is hard to remove with out etching the original part.There are lots of approaches that have shown up in print and there is no one way that works for everything. In your case, I would try the reverse in the Woods nickel followed by forward plating. You can find the method(s) in several plating reference books.
James Watts- Navarre, Florida
2003
2003
Hi Ted,
Great thanks for your answering.
But I think the last letter might be misunderstand, it due to my poor English. Actually, our desired process is making the original Nickel plate "can not" be separated. Allow me explain it more clearly.
1. Electroform one Nickel plate.
2. Do some process on its surface.
3. Then electroform the plate again.
Usually, a normal Nickel plate can electroform again for a thicker thickness if the plate is fresh and nothing on it's surface. But after our designed process, the plate would not fresh. Therefore, how to clean the surface or do anything to make the original one electroform with the new one?
Thanks again for your help and expect for more information.
Best Regards,
- Tao Yuan, Taiwan
Just for my clear understanding. Could you explain in your sequence No. 2 what surface do you mean "do some work". Is it the separated electroform face or is it the back of the electroform? Also, where do you want to continue building up more metal. In the copied face or the back?
Guillermo MarrufoMonterrey, NL, Mexico
2003
If you are using nickel with organic additives such as brighteners or levelers, this will make subsequent adhesion of nickel to the original deposit very difficult. Even saccharin can cause problems. I would suggest you reactivate the nickel with a good acid clean and then do a high chloride nickel strike, followed by our electroforming nickel. If you can reactivate the first nickel deposit, you will get good adhesion.
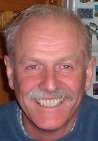
Trevor Crichton
R&D practical scientist
Chesham, Bucks, UK
2003
Q, A, or Comment on THIS thread -or- Start a NEW Thread