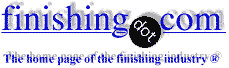
-----
Pitting problems in bright anodizing
Q. You have helped me in the past with my problems concerning custom anodizing of Penn International fishing reels. The past few job's have come out terrible. I provide new gold anodized parts which are stripped by my anodizer. I then take them and wet sand them on a lathe and polish them to a mirror finish. After anodizing them royal blue they come back with a almost frosted look and some white spots about .020 . In my opinion the spots are from acid splash. They say its pitting , but the parts are brand new and each time they try to re-finish the job the spots are in a different place. WHY do I get a satin / frosted finish on highly polished parts? Please help me / them with a solution to the problem. My reputation of providing the best anodizing is excellent and reels from around the world are sent to me for that reason. Now I'm VERY concerned as my reputation is only as good as the finish I provide. I need to retain the luster of my polishing efforts with no spots. Yours truly:
Tom Testa- Deep River, Connecticut
1996
A. Hi Tom. Parts which are to be anodized are routinely "etched" after cleaning and before desmutting. This is probably where the satin/frosted finish is coming from. You can ask your anodizer to go very light on the etch. But if you want a truly bright and specular finish, the parts must be "bright dipped" instead of etched; this is the finish that is used on aluminum reflectors, and may be too bright and prone to fingerprinting for you. Bright dipping is done in a nasty nitric/phosphoric mixture that not all anodizers can do.
In the troubleshooting columns of the trade journals, perhaps no problem is more commonly reported than pitting of anodized parts. It can be caused by trying to anodize an unacceptable alloy where segregation has already occurred, corrosion during storage, re-anodizing without stripping the previous anodized coating, poor rack materials or compatability, chlorides in the anodizing solution, inadequate rinsing, porosity in the material, and other possibilities as well. Good luck.
But really, as the purchaser, your job is to find out exactly what alloy you are trying to anodize, and describe it and your mechanical treatment, and your desires, to the anodizer. His/her job is to give you pit-free anodizing, or tell you what you are doing that is making the job problematical. It probably isn't in your power or ours to troubleshoot a pitting problem solely from the end result. We might be able to help your anodizer fix the problem, but we probably can't help you help him. If your present anodizer doesn't give you good parts, you must find an anodizer who will; one of the anodizers listed in our shop directory may be able to help you.
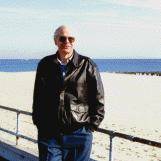
Ted Mooney, P.E.
Striving to live Aloha
(Ted can offer longterm or instant help)
finishing.com - Pine Beach, New Jersey
1996
2003
Q. We need to bright anodize deep drawn (3005 ) components which are mechanically buffed. We have two conditions:
Pass the parts through the bright dip, which results in a lot of pitting marks and the finish is dull.
Skip the Bright dip, which results in no pit marks but still a Dull finish
Our questions are
1. Is 3005 suitable for bright anodizing.
2. How to avoid pit marks .
3. Any suggestion on the chemistry we need to use for bright dip, anodizing. <
4. In some components we need matte gold. Suggest dye manufacturer
director - Bangalore, Karnataka, India
A. Alloy 5252 is probably best; alloy 3005 is probably doable.
As in all metal finishing problems, it is difficult to determine what may be wrong based on a single symptom, and your telling us nothing at all about your process. Typical causes of pitting include high specific gravity, embedded soil, and metallurgical defects. But are the pits in any particular area of the parts? Near the top, near the bottom, on the underside? Pitting in recesses may indicate low concentration of nitric acid or poor agitation.
Please tell us what you are using for bright dip and anodizing chemistry. Thanks :-)
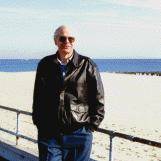
Ted Mooney, P.E.
Striving to live Aloha
(Ted can offer longterm or instant help)
finishing.com - Pine Beach, New Jersey
2003
Q. I am also experiencing pitting in bright dipped 6061 aluminum parts. What I have noticed however is the pitting only occurs in parts that we tumble first before sending them out to be anodized. We tumble all our parts to remove any machine marks but we recently tried polishing some caps we sent up without tumbling. they came back with no pitting whatsoever. Because we need to tumble our parts, I have to find out how the tumbling process is contaminating the parts. I've changed all media and put filters on the water supply and air lines used to blow dry the parts. Our finisher tells us the pitting is occurring during the bright dip process.
Ron DiCostanzo- Stratford, Connecticut, USA
October 26, 2013
A. The tumble media must be designated ALUMINUM ONLY, no exceptions, otherwise you pound iron filings into the soft Kleenex-like aluminum, which plates away in the anodizing tank and leaves a pit. Be sure no one comes in on the night shift and tumbles his gun parts !!
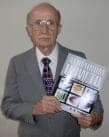
Robert H Probert
Robert H Probert Technical Services

Garner, North Carolina
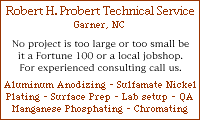
October 29, 2013
October 30, 2013
A. Hi Ron,
A description of the pitting would be helpful in trying determine the source. Are they deep/shallow, rounded/jagged, large/small? Are they more numerous on surfaces depending on the orientation in racking? - one for the anodizer.
I suggest 3 possible causes:
1. Corrosion of the aluminium during the tumbling.
2. Insoluble solids left on the surface after drying.
3. particles embedded in the surface during tumbling.
Look closely at the parts after tumbling and drying. You may see small, maybe black, spots. These spots often appear black because they are narrow and deep and no light is reflected back. The bright dip opens up the hole and makes it more obvious. Also the brighter, smoother surface makes the pit easier to see.
Curiously clean water is often troublesome in creating rapid corrosion. Also some batches of aluminium are much more prone than others. A small addition of nitric acid, say 1ml/l, or a trace of chromic acid will usually prevent this corrosion: please consider the effect of these additions on the equipment and waste water disposal!!!
If you get insoluble materials on the surface then you may get the reverse of a pit - a bump. This is caused by the surface contaminant resisting chemical dissolution in the bright dip and so standing proud. It looks very much like pitting! The bright dip will usually remove the contaminant eventually but the damage is then done. The bump is often surrounded by a shallow pit - commonly, in the UK, called castle and moat pitting.
A soak in a nitric acid dip - perhaps a desmut tank - will sometimes remove surface contamination.
My actual experience of 3 is limited to embedded particles from mechanical polishing with contaminated mops.
Harry
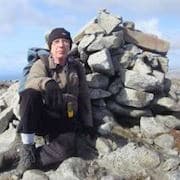
Harry Parkes
- Birmingham, UK
Q. Some identical parts show no pitting while others have pitting throughout. My anodizer suggested that some of the parts may be oxidizing after they come out of the tumbler and sit a while. (they come for pickup once a week)Possibly the first parts done are sitting much longer than the latest parts before anodizing. They suggested I dip the parts in a water soluble oil right after rinsing the parts out of the tumbler. I'm going to give this a try this week.
I'm posting photos of the pitting issue.
- Stratford, Connecticut, USA
October 31, 2013
Pitting in gold anodized 6061-T6 parts
February 11, 2015Q. We recently received a batch of 140 parts that have pitting covering the entire part. The material is 6061-T6 aluminum with a gold anodize. The pitting is on the inside diameter and on the outside surfaces. We have been producing these parts for the last 10 years and have never had this issue.
We contacted the anodizing vendor, they state that the pitting problem is the material and not their process. We have very little to go on, so any advice we can get on how to determine the cause would be very helpful.
EMILIO RAVELOMANUFACTURING - CINCINNATI
A. That resembles severe chloride contamination in the anodizing process. I've seen something very similar 2 times over the years. Once was when an operator mistakenly added HCl instead of H2So4 to the anodizing tank, and the other was when an operator on night shift thought he was doing day shift a favor by pre-treating some parts to be anodized, and left them in a tap water rinse tank overnight.
Is it possible it's a material issue...yes, I suppose something could have gone terribly wrong in your finishing process prior to anodizing (some type of metallic contaminate being embedded into the substrate during surface finishing...are these parts tumbled?), but to me, this looks like something went very wrong in the anodizing process.
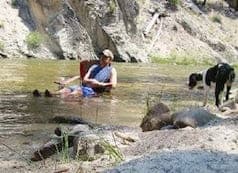
Marc Green
anodizer - Boise, Idaho
February 12, 2015
A. I think it seems corrosion effect. I can say some reason because I see this problem sometimes on our product. So that, we can see rack of good another bad as a corrosion defect. We can see this problem between etching and anodizing baths.
1- all rinses especially neutralization (acid) bath's should be clean enough
2- if you use sulfuric acid in neutralization you should be nitric acid as a oxidizing agent (and hydrogen peroxide)
3- if this problem occur often,you should check your baths ground connections. All baths should be ground connection for electrical aspect
4- except these reasons(except chemical proses); it can occur atmospheric condition. For example;if your product which can be anodized wait long time somewhere it can be possible.and of course it can occur in extrusion + design of dies.
akpa aluminum - sakarya,turkey
February 18, 2015
Q, A, or Comment on THIS thread -or- Start a NEW Thread