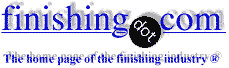
-----
Hex nuts need better corrosion resistance than cadmium plating
We have a customer that is complaining of extreme corrosion of a hex nut. We currently use cadmium plating on the nut. Is there a low cost plating that will resist corrosion better than the cadmium. Possibilities..? Zinc Tin/Zinc Black Oxide ?
Chris RenisEngineer - Chicago, Illinois, USA
2003
Hello Chris. Cadmium is an accumulating biotoxin that is not used anymore except when a special application requires its unique combination of qualities (corrosion resistance, lubricity, freedom from stick-slip, lack of bulky and gummy corrosion products, galvanic compatibility with aluminum).
If your only requirement is corrosion resistance, you should have gotten rid of cad plating years ago, but now is certainly the time. Zinc is the least expensive replacement but may not be satisfactory on several grounds. Tin-zinc may be ideal. But picking a corrosion resistant finish depends on the environment and what is causing the corrosion; and, as alluded to, other factors besides corrosion resistance may need to be considered in picking a finish for the hex nuts.
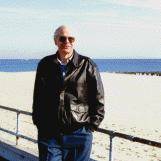
Ted Mooney, P.E.
Striving to live Aloha
(Ted can offer longterm or instant help)
finishing.com - Pine Beach, New Jersey
2003
First of two simultaneous responses --
Depending on strength requirements, stainless steel might be a less painful way to go. I suspect that your Cad plated nuts had a very thin coating. The user might also have been using a pipe wrench or vice grips which no plating will stand up to.
James Watts- Navarre, Florida
2003
Second of two simultaneous responses -- 2003
As Ted already mentioned, choosing an appropriate finish will depend on the environment, among other things. Improvements in corrosion resistance can be obtained by changing to a different coating. The following ranking should give you some idea of typical fastener coatings:
black oxide + oil
heavy zinc phosphate + oil
cadmium plating + chromate conversion coating
zinc plating + chromate conversion coating
zinc alloy plating (zinc-iron or zinc-nickel) + chromate
organic coatings with Al and/or Zn
Organic coatings such as those from Magni and Doerken are formulated to minimize thread fill of internal threads, but this can still be a problem. Zinc-nickel alloy plating is better than zinc-iron, but would likely be the most expensive option. Zinc-iron alloy + chromate + topcoat seal can provide good corrosion performance at a fairly low cost.
Automotive module supplier - Michigan
Q. We are working on a replacement for cadmium plating for some small parts in an aircraft. The plating will be on steel and stainless steel parts. The parts will contact aluminum parts. The aircraft will experience warm and cold environments, and occasionally moisture. These parts will not need the lubricity, conductivity, or malleability of cadmium plating. Based on what I've read on this website, it sounds like Tin-Zinc will provide the best resistance to galvanic corrosion. Is this true?
Carl Soldat- Somerset, New Jersey, USA
October 1, 2012
A. Hi Carl. Unless you are designing the aircraft, you generally don't have the freedom to do anything but follow the specs.
I'm sorry but I don't know which zinc alloy comes closest to galvanic compatibility with aluminum, but it is possible that under the varying conditions of wet/dry, oxygen/anerobic, and hot/cold that none come close enough, and you would be limited to coating with aluminum or staying with cadmium.
Regards,
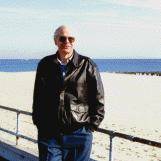
Ted Mooney, P.E.
Striving to live Aloha
(Ted can offer longterm or instant help)
finishing.com - Pine Beach, New Jersey
October 2, 2012
Q. Thanks Ted. The design is an old design, but it is going onto a new aircraft for a foreign company. They insist we avoid the use of Cadmium. I have the freedom to use whatever plating I decide is best, but I would like to find some test data to support my decisions. All the reports I've found regarding Zn-Ni indicate that it is good for corrosion resistance and lubricity, but I have not found anything to indicate it is good for galvanic corrosion resistance. Other postings on finishing.com imply that Sn-Zn is the best plating to prevent galvanic corrosion (aside from Cd). Do you know of any test data to support this?
For example, this report
www.elisha.com/docs/ElishaTech_AlcoaEvaluationofCadmiumAlternativesPhaseIV_VPaper.pdf
shows that for two particular fasteners, Zn-Ni is good for many properties, but it does not address galvanic corrosion.
Thanks again,
Carl.
- Somerset, New Jersey
October 4, 2012
A. Thanks for the helpful link, Carl. The report you seek may exist, and hopefully a reader will steer you to it, but I can't.
If you can re-find the thread on finishing.com that gave you the impression that Sn-Zn is best for galvanic compatibility I'd like to review it. It might either lead us towards the report you seek, or it may require editing or a footnote if you inferred something the poster didn't actually mean to imply. Thanks!
Regards,
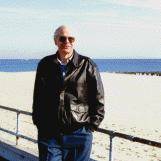
Ted Mooney, P.E.
Striving to live Aloha
(Ted can offer longterm or instant help)
finishing.com - Pine Beach, New Jersey
October 4, 2012
October 8, 2012
Q. Hi Ted,
The link below has several people stating that Tin-Zinc is the best for all-around corrosion protection. Although, none of them stated that it is good for galvanic corrosion, so perhaps I was remembering it incorrectly.
www.finishing.com/130/89.shtml
Some plating companies state on their websites that Tin-Zinc is good for steel parts contacting aluminum. See the links below.
www.roymetalfinishing.com/finishing_tinzinc.php
www.surfacetechnology.co.uk/zinc-alloy-plating/
Was I inferring incorrectly about the galvanic corrosion resistance properties of Tin-Zinc? I'm just hoping to find something that will perform similarly to cadmium for steel parts contacting aluminum.
Thanks again for your help.
- Somerset, New Jersey
A. Hi again, Carl. Despite those links I would be very hesitant to suggest that tin-zinc fasteners can be used in contact with aluminum on airplanes unless you find real evidence. I am quite confident, however, that aluminum applied by ivadizing or non-aqueous electroplating would be compatible.
I would suggest that you try contacting SPS Technologies in Jenkintown, PA as they have long been known as experts in fasteners for aircraft, and they may be able to advise about the availability of aluminum coated fasteners and the suitability of tin-zinc plated ones. Good luck.
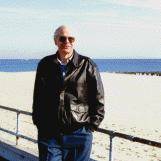
Ted Mooney, P.E.
Striving to live Aloha
(Ted can offer longterm or instant help)
finishing.com - Pine Beach, New Jersey
October 10, 2012

Q, A, or Comment on THIS thread -or- Start a NEW Thread