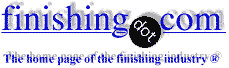
-----
Aerospace test application requires EN not cause loss of spheracity
2003
I've been trying to get a straight answer to this question for some time now. When the talk is of the advantages of electroless nickel, the chief selling points are of two main factors. One, is control over the nominal thickness, that is to say, control over the amount of build-up, if one is interested in achieving certain final dimensions. The second is the uniformity of the build-up independent of the mean amount. Of the two, I am only interested in the second-- the uniformity. As of yet, I am not concerned at all with the overall amount of coating thickness. All websites with regards to EN mention the uniformity as one of the main advantages but none have actually quantified this term. Is this something you can help me with?
My application is a six inch diameter 6061-T6 aluminum hemisphere which is figured to within 0.000050 ½ variation on the spherical radius. Once again, the nominal spherical radius is not important to us, only the relative variation. The hemispheres currently are Hardcoated and refigured afterwards. We are considering changing to EN especially if it means we can eliminate the second shaping process. In the end we want to be within 0.000075 ½ including the coating over the base metal. Along with the first question, can someone verify this? I assume that heavier EN coats will be more prone to uniformity variation. In other words, the thicker the coating, the more uneven. Is this true? Can this relationship be quantified as well? How much variation could be expected in a nominal thickness of 100 millionths inch? How much variation for 0.002-inch thickness coat?
Thanks,
Daniel OtlowskiAerospace Test Equipment - Berlin, Connecticut, USA
Main factor to uniformity is bath stability. This includes prep cycle, bath chemistry, temperature and pH, among other. The last three variables related to the liquid in close proximity to the part surface. You mentioned it very clearly that the thicker the deposit, the longer the plating time and the harder to make sure everything remains unchanged, specially in this thin liquid layer that is supporting the strong reaction to reduce the metal. Yours is a stringent application, but variation in a very well engineered operation should be within your needs.
Guillermo MarrufoMonterrey, NL, Mexico
2003
Strict solution control is essential. The usual cause of non-uniform plating is related to the amount and type of agitation of the plating solution as it is related to solution stabilizers. Stabilizers are in commercial solutions in a few parts per million. They act to poison (prevent plating) of extraneous particle that may get into the solution. They also act upon the surface of the metal being plated. Using the law of mass action, if one part of the surface receives more agitation than other areas, thin deposits may occur in the affected area. Uniform slow agitation, careful control of temperature, pH and solution chemistry can result in nearly perfect uniform thickness on all surfaces of a sphere.
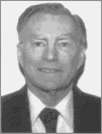
Don Baudrand
Consultant - Poulsbo, Washington
(Don is co-author of "Plating on Plastics" [on Amazon or AbeBooks affil links]
and "Plating ABS Plastics" [on Amazon or eBay or AbeBooks affil links])
2003
We site a +- 0.00005" uniformity on the plating we do. I don't think anyone has ever tried to measure below that. I would not want to try to maintain that over anything thicker than 0.002" of plating, especially on aluminum. Preparation of the aluminum will also be critical so as not to change any dimensions as well.
Michael Zuraw- Georgetown, Ontario
2003

Q, A, or Comment on THIS thread -or- Start a NEW Thread