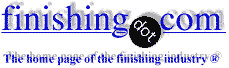
-----
Coating stainless steel for low friction -- DLC vs. Chrome, Electroless Nickel
2003
Q. Hello all!
I am an engineer with an R&D company. Our customer wants us to test some coatings on stainless steel to reduce the friction between steel and sand and determine how long the coating will last. My company is having some 1' X 1' stainless steel plates and short (1" dia) rods coated with four different materials each (chrome, DLC, etc.). We want to test two things:
1) The coefficient of friction between the coating on the plates and sand.
2) How long the coatings will last on a cylindrical part if spun at a low speed immersed in sand.
I have ordered the ASTM standard for testing friction on metal surfaces to give us some guidelines so that we may develop a standard, reliable test for 1). At the very least, we are planning on using a force gauge to push/pull the 1' X 1' plate (loaded with a weight) across sand. We would then divide the static and dynamic force gauge measurements by the total weight of the plate and weight in order to get the static and dynamic coefficients of friction. Ff/Fn = u, where Ff is frictional force (measured with force gauge), Fn is the normal force of the plate (its total weight) and you is the coefficient of friction. Obviously, this isn't a precise method and errors will result due to our hand pushing/pulling and gauging visually when the plate just begins to move or is just moving at a constant speed. Any suggestions on performing a more accurate test to determine the coefficient of friction?
On the wear issue, we are planning on using a micrometer on the rods before and after immersing and spinning them in sand to determine the difference in diameter and thus wear. We are trying to determine how long specific coatings will last. We have also discussed sending out the coated rods to a company that can more accurately measure the surface roughness before and after spinning the rod in sand. Any suggestions on conducting a test to gauge how long a particular coating on a stainless steel rod will last if immersed and spun in sand?
Any help or suggestions is greatly appreciated.
Anthony AbbottR&D - Springfield, Virginia
A. Another method to test coating lifetime is to measure the weight of the rods. Compare weight loss with time of an uncoated rod to a coated rod. If the coating wears less than the SS than when the coating is worn through the mass loss per unit time will increase.
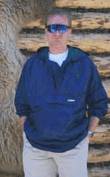
John Davis
- Berthoud, Colorado, USA
2003
A. We process a co-deposit of Electroless-Nickel w/ particles of P.T.F.E.(Teflon) which provides longevity to wear components because of a low co-efficient of friction.
Charlie Camenzind- Phoenix, Arizona, USA
2003
Q. I am a final year B.Eng student of Huddersfield University. I am currently designing a unit that handles sand. I would be very grateful for any information that you could give me on the friction of sand on stainless steel or galvanized aluminium. Any help you could offer would be gratefully received.
Stuart ArmourHuddersfield University - Huddersfield, West Yorkshire, England
2003
2003
A. Re. sand abrasion, why not try out some plastics?
Probably the best one is using a 2 component Urethane ... fantastic elasticity, too.
The mines, conveying metallic slurries, normally always use Polyethylene pipe due to cost, longevity and low slip co-efficient ... but for 'coating' something, I'd consider Polyurethane.
Food for thought, anyhow.
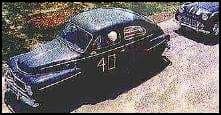
Freeman Newton [deceased]
(It is our sad duty to advise that Freeman passed away
April 21, 2012. R.I.P. old friend).
Q, A, or Comment on THIS thread -or- Start a NEW Thread