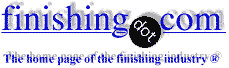
-----
Stress corrosion cracking in 304 SS submersible motors
We use .0050 thick 304 stainless strip steel in our shop. We have seen some stress corrosion cracking in this material. We have looked and looked for the cause but can't find one. We know where the stress and heat are but can't find the corrosive cause. Has anybody had any trouble with this kind of material or a suggestion about changing to another grade of stainless?
Steve Laytonsubmersible motors - Wilburton, Oklahoma
2003
First of two simultaneous responses --
SCC involving austenitic stainless steels is almost always caused by the presence of chloride ions, although other halogen ions can initiate pitting and subsequent SCC as well. Pitting is most frequent in aerated or mildly acidic oxidizing solutions. If you are certain that SCC is the problem, then perhaps a ferritic or duplex stainless steel alloy can provide suitable performance, as these grades are either immune or highly resistant to SCC. Go to the SSINA and Nickel Development Institute websites for more information on stainless steel grades. Another option to consider would be austenitic alloys with higher amounts of Mo, which confers greater passivity in the presence of chloride ions. These grades (316, 317, 904L, etc.) are still susceptible to SCC, but may prove adequate for your application. Good luck.
Toby PadfieldAutomotive suspension modules - Michigan
2003
Second of two simultaneous responses --
Electropolishing relieves stress AND prevents corrosion. Need more info on environment that parts fail in to make any kind of intelligent call.
Dan Weaver- Toccoa, Georgia
2003
Q, A, or Comment on THIS thread -or- Start a NEW Thread