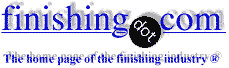
-----
6061 part anodizes well, same part in 7075 burns
Q. We are a small shop that does some anodizing on the side. We generally do type II anodizing on 6061. Have been trying to do some 7075 at the same voltage (11.00 volts), temp (70-72 deg), and time (15 min) as the 6061 (exact same part just different material). When we do the 7075 it comes out with a burnt finish. This is noticeable as soon as the part is removed from the anodize tank and the part dries off. Tried dyeing and sealing the part but same result occurred. We didn't know if we need to reduce the time in the anodize tank or the voltage. Any help would be appreciated.
Andy McClellanmachine shop - Blountville, Tennessee, USA
2003
A. I assume your unit of temperature is in Fahrenheit, else no wonder it burns. I wonder if you are just misjudging the resulting color of anodic coating as "burnt color". Different alloys produce different color after being anodize. As a matter of fact, we anodize the 7xxx series at higher voltage than you do and at longer time.
Ciraco Dipaloloco- Toronto
2003
![]() |
2003
Alcoa in 1956 recommended in 15%/weight Sulfuric Acid at 70 F, to get 12 ASF, 6061 needs 15 volts on the part and 7075 needs 16 volts on the part. Now on most rectifiers 15 volts and 16 volts is close enough to the same but 11 volts is not enough. Whereas it seems to you to be enough on the 6061 the 7075 is loaded with about 5% zinc which not only imparts a more gray color but also stays down in the pores with low voltage. Further if you run much 7075 the zinc is soluble in your cleaner and your etch and your deox and your anodizing tank, hence all must be dumped more frequently. Finally how about the dissolved aluminum (and zinc) in the anodizing solution. Try 16 volts (17 if thru titanium racks), then add a 5% nitric acid dip between the anodizing and the dye. Meanwhile find out the dissolved aluminum and come back to us with updated data. ![]() Robert H Probert Robert H Probert Technical Services ![]() Garner, North Carolina ![]() Q. The color of the part is not where the problem is. When the part is dry you can touch it and the coating is soft and will wipe off. If the part is blue then when you wipe it, what ever you use to wipe it will be blue. We tried anodizing for half the time and the part came out fine and didn't burn, but the coating is very thin. Just wondering what would cause this. Andy McClellan [returning]machine shop - Blountville, Tennessee, USA 2003 |
A. Electricity converts the aluminum to aluminum oxide at a given rate for that voltage. The acid slowly eats the formed oxide away. At 12 volts, you are barely forming a layer and what is formed is going to be very soft as it is more like a mush of oxide. 7075 is not liked by most anodizers as it contains about 10% alloying materials that are soluble in the acid. This means that when you form an oxide layer slowly, it is going to be like swiss cheese (10% holes). If you want a nice layer, try 18 volts and lower the temperature by 2 to 4 degrees.
As you have found out, there is no way to repeatedly form a good layer on 7075 at 12 volts. Buy a [higher voltage] power supply and you will have better anodizing, even on the 6061.
James Watts- Navarre, Florida
2003
My anodizing is soft and mushy
Q. This explains my soft mushy oxide layer on 7075 (anodizing at 12 volts). I calculated the amperage for 1.22 sq ft, at current density of 6 amp = about 7.3 amps. When I ran the power supply at 7.3 amps the voltage starts off around 8 or 9 and slowly ramps up to 12 or so volts over 90 min. I know my area is very close.
My question is: why could the voltage be so low other than area being off? Not using power supply correctly? Bad (eBay $60) power supply?
Interestingly, 6061 hanging wire and test piece seemed to have a good oxide layer at 12 volts, 90 min, 6 asf.
Thank you in advance.
- Woodstock, Illinois, USA
February 7, 2018
A. Hi Jim. When you speak of a $60 power supply, I assume you are a hobbyist, not a professional anodizer? One reason I ask is that I've heard that hobbyists sometimes try to use a more forgiving low current density approach to anodizing which I don't know the details of. To my understanding, professionals would use 12 ASF and 15-16 volts for 7xxx alloys.
Perhaps your power supply is only a 12-volt one and can't go higher? What is its rating?
Regards,
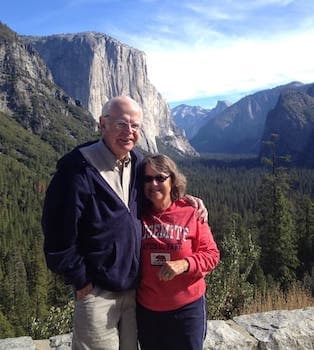
Ted Mooney, P.E. RET
Striving to live Aloha
(Ted can offer longterm or instant help)
finishing.com - Pine Beach, New Jersey
February 2018
Yes Ted, I an definitely not a professional! I was attempting the LCD method. I can in fact achieve 15 volts with my power supply. I read others places to set the amperage and the voltage will take care of itself. I'll do another run at 12 ASF. Thanks for the input. I have learned a lot from this forum!
- Woodstock, Illinois USA
February 10, 2018
Q, A, or Comment on THIS thread -or- Start a NEW Thread