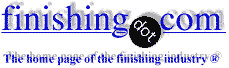
-----
Any Electropolishing cathode material better than lead?
[an error occurred while processing this directive]We perform large scale electropolishing on stainless steel wire products, grade 304 (18/10) and we would appreciate it if you could advise us which cathode material is the most suitable/economical according to your experience. We are currently using a H2SO4 and H3PO4 solution with lead cathodes.
Thanks for taking the time to assist us.
Mario VortserS/Steel wire product manufacturer - Cape Town, Western Province, South Africa
2003
That's a good question, Mr. Vortser. I've never seen other than lead myself.
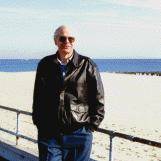
Ted Mooney, P.E.
Striving to live Aloha
(Ted is available for instant or longterm help)
finishing.com - Pine Beach, New Jersey
2003
I've only ever seen lead as well. It is cheap, inert(ish) and easy to clean down.
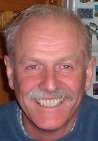
Trevor Crichton
R&D practical scientist
Chesham, Bucks, UK
2003
We use Nickel, Lead is not popular in Denmark. I have no knowledge about lead cathodes, but our is now 6 years old.
Bo Kønig- Odense, Denmark
2003
First of two simultaneous responses --
The use of lead is on the way out due to environmental reasons. All the electropolishing shops I have seen in California use copper. It is the best choice for carrying current, especially when constructing a conforming cathode inside a tank: A framework of barstock, bent to shape, distributes the electricity, while copper mesh, stood off 1€ from the surface, does the work and allows gases to escape.
For electropolishing tubing interiors, a copper wire, insulation stripped off in the working section, is slowly drawn through the electrolyte-filled tube.
For general purpose work, copper sheet is hung from movable copper cathode bars spanning the tank. While Cu does tend to dissolve in the electrolyte, this is limited by a protective slime, so replacement is less frequent than might be expected. Also, cathodic protection can be used (with a graphite anode) when the tank is idle.
Ken Vlach [deceased]- Goleta, California

Rest in peace, Ken. Thank you for your hard work which the finishing world, and we at finishing.com, continue to benefit from.
2003
Second of two simultaneous responses --
We electropolish 300 series stainless steel in a Phosphoric/Sulfuric acid solution and have been using 316 stainless cathodes for approx. 8 years. They work fine and have held up well. The only concern is that periodically the cathodes must be cleaned to remove scale that forms on them.
Thomas Kemp- Erie, Pennsylvania, USA
2003
In electropolishing process, so many people using lead cathode, but this is not correct one. the better one is platinum plating. this make very good conductivity and this avoid the dissolution of cathode.
R.S.ThangappanTi.anode - Chennai, Tamilnadu, India
2007
Q, A, or Comment on THIS thread -or- Start a NEW Thread